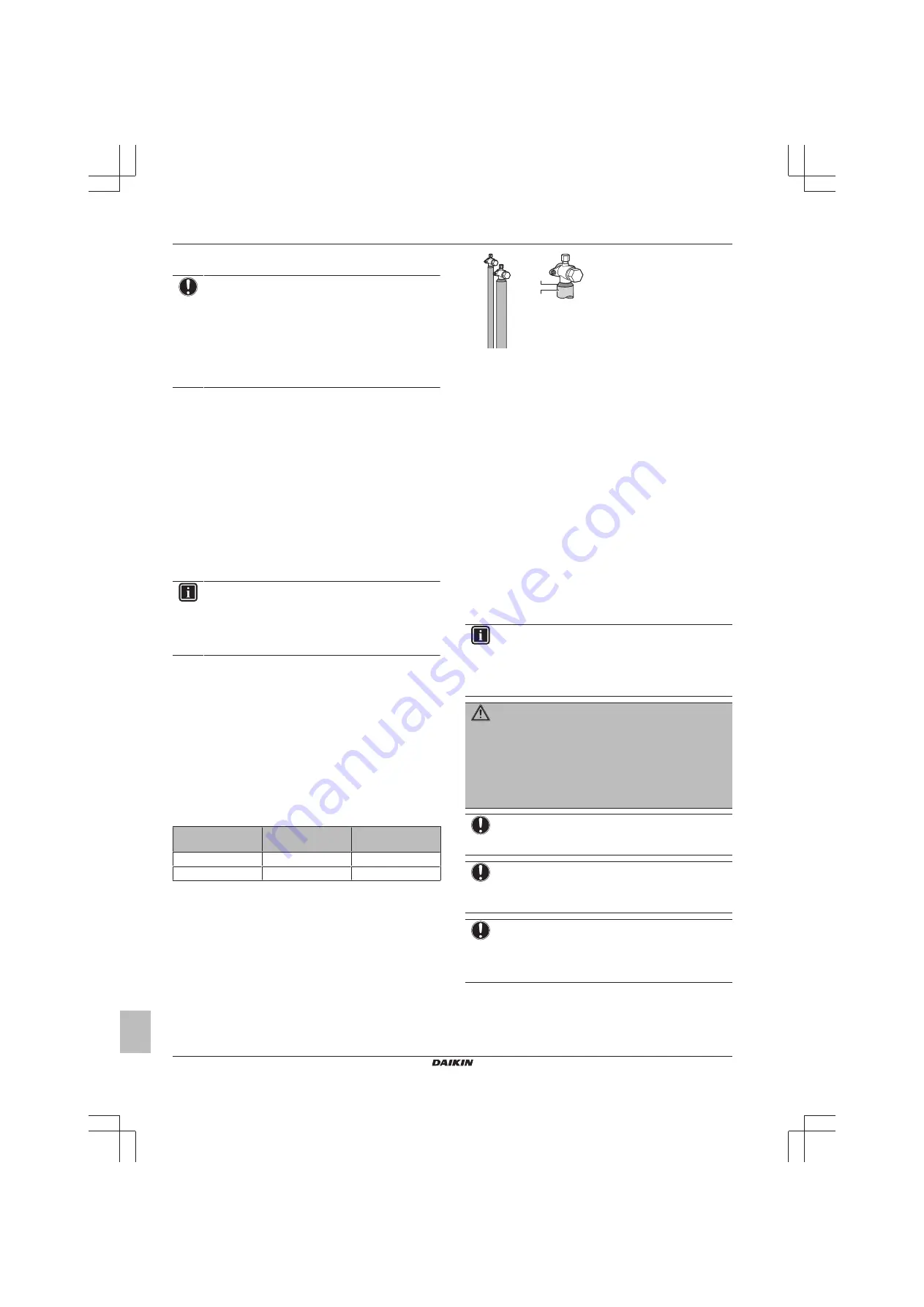
6 Installation
Installer and user reference guide
22
RXYSQ4~Y1B
VRV IV-S system air conditioner
4P404676-1A – 2016.03
6.5.5
To perform vacuum drying
NOTICE
The connections to the indoor units and all indoor units
should also be leak and vacuum tested. Keep, if existing,
all (field supplied) field valves to the indoor units open as
well.
Leak test and vacuum drying should be done before the
power supply is set to the unit. If not, see
checking the refrigerant piping" on page 20
information.
To remove all moisture from the system, proceed as follows:
1
Evacuate the system for at least 2 hours to a target vacuum of
–100.7 kPa (–1.007 bar/5 Torr).
2
Check that, with the vacuum pump turned off, the target
vacuum is maintained for at least 1 hour.
3
Should you fail to reach the target vacuum within 2 hours or
maintain the vacuum for 1 hour, the system may contain too
much moisture. In that case, break the vacuum by pressurising
with nitrogen gas to a gauge pressure of 0.05 MPa (0.5 bar)
and repeat steps 1 to 3 until all moisture has been removed.
4
Depending on whether you want to immediately charge
refrigerant through the refrigerant charge port or first pre-charge
a portion of refrigerant through the liquid line, either open the
outdoor unit stop valves, or keep them closed. See
charge refrigerant" on page 23
INFORMATION
After opening the stop valve, it is possible that the pressure
in the refrigerant piping does NOT increase. This might be
caused by e.g. the closed state of the expansion valve in
the outdoor unit circuit, but does NOT present any problem
for correct operation of the unit.
6.6
To insulate the refrigerant piping
After finishing the leak test and vacuum drying, the piping must be
insulated. Take into account the following points:
▪ Make sure to insulate the connection piping and refrigerant branch
kits entirely.
▪ Be sure to insulate the liquid and gas piping (for all units).
▪ Use heat resistant polyethylene foam which can withstand a
temperature of 70°C for liquid piping and polyethylene foam which
can withstand a temperature of 120°C for gas piping.
▪ Reinforce the insulation on the refrigerant piping according to the
installation environment.
Ambient
temperature
Humidity
Minimum thickness
≤30°C
75% to 80% RH
15 mm
>30°C
≥80% RH
20 mm
Condensation might form on the surface of the insulation.
▪ If there is a possibility that condensation on the stop valve might
drip down into the indoor unit through gaps in the insulation and
piping because the outdoor unit is located higher than the indoor
unit, this must be prevented by sealing up the connections. See
below figure.
b
a
a
Insulation material
b
Caulking etc.
6.7
Charging refrigerant
6.7.1
About charging refrigerant
The outdoor unit is factory charged with refrigerant, but depending
on the field piping you have to charge additional refrigerant.
Before charging refrigerant
Make sure the outdoor unit's
external
refrigerant piping is checked
(leak test, vacuum drying).
Typical workflow
Charging additional refrigerant typically consists of the following
stages:
1
Determining how much you have to charge additionally.
2
Charging additional refrigerant (pre-charging and/or charging).
3
Filling in the fluorinated greenhouse gases label, and fixing it to
the inside of the outdoor unit.
6.7.2
Precautions when charging refrigerant
INFORMATION
Also read the precautions and requirements in the
following chapters:
▪ General safety precautions
▪ Preparation
WARNING
▪ Only use R410A as refrigerant. Other substances may
cause explosions and accidents.
▪ R410A contains fluorinated greenhouse gases. Its
global warming potential (GWP) value is 2087.5. Do
NOT vent these gases into the atmosphere.
▪ When charging refrigerant, always use protective
gloves and safety glasses.
NOTICE
If the power of some units is turned off, the charging
procedure cannot be finished properly.
NOTICE
Be sure to turn on the power 6 hours before operation in
order to have power running to the crankcase heater and
to protect the compressor.
NOTICE
If operation is performed within 12 minutes after the indoor
and outdoor units are turned on, the compressor will not
operate before the communication is established in a
correct way between outdoor unit(s) and indoor units.