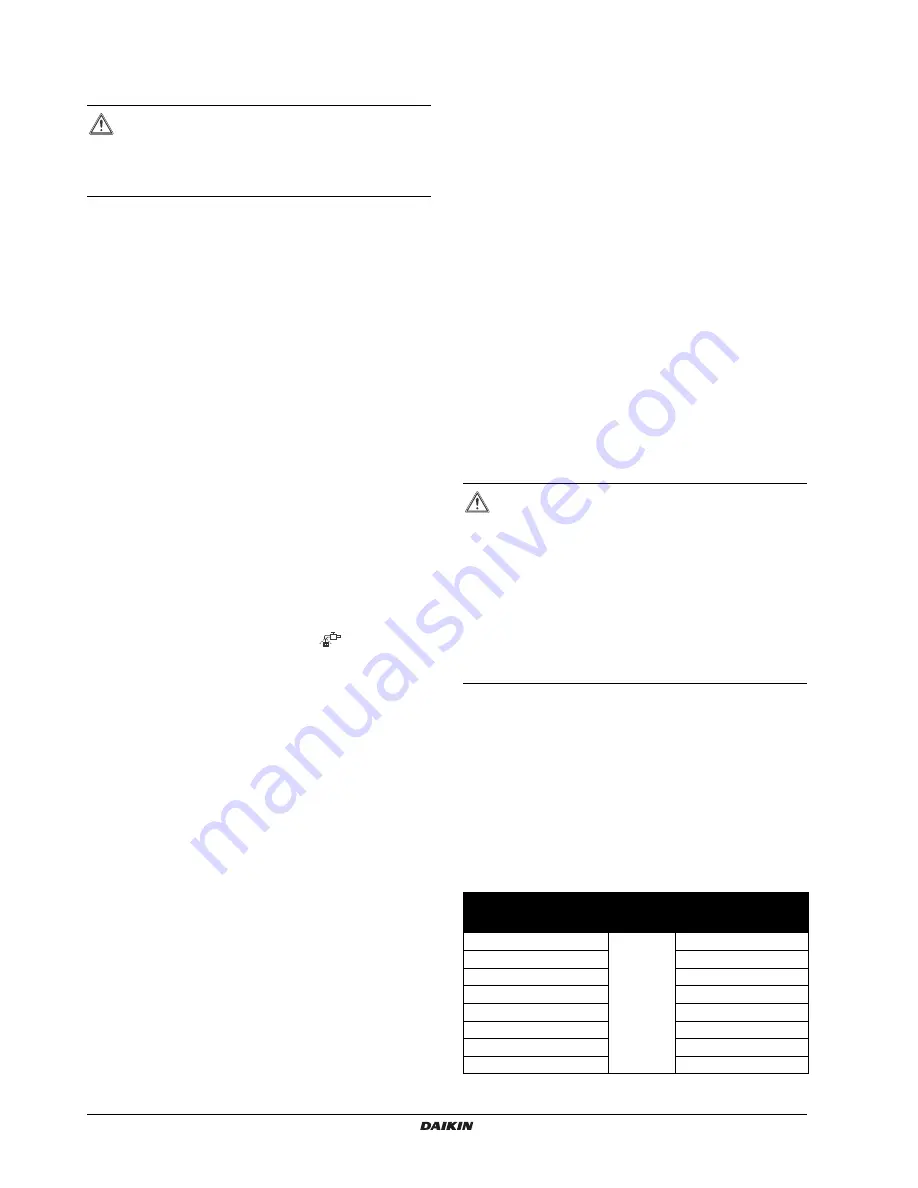
Installation and operation manual
58
RXYQQ8~20T7Y1B
VRV IV System Air Conditioner
4P345099-1 – 2013.04
10. Troubleshooting
If one of the following malfunctions occur, take the measures shown
below and contact your dealer.
The system must be repaired by a qualified service person:
If a safety device such as a fuse, a breaker or an earth leakage
breaker frequently actuates or the ON/OFF switch does not
properly work.
Measure: Turn off the main power switch.
If water leaks from the unit.
Measure: Stop the operation.
The operation switch does not work well.
Measure: Turn off the power.
If the user interface display indicates the unit number, the
operation lamp flashes and the malfunction code appears.
Measure: Notify your installer and report the malfunction code.
If the system does not properly operate except for the above
mentioned cases and none of the above mentioned malfunctions is
evident, investigate the system according to the following
procedures.
1
If the system does not operate at all:
Check if there is no power failure.
Wait until power is restored. If power failure occurs during
operation, the system automatically restarts immediately
after the power supply is recovered.
Check if no fuse has blown or breaker has worked.
Change the fuse or reset the breaker if necessary.
2
If the system goes into fan only operation, but as soon as it goes
into heating or cooling operation, the system stops:
Check if air inlet or outlet of outdoor or indoor unit is not blocked
by obstacles. Remove any obstacle and make it well-ventilated.
Check if the user interface display shows
(time to clean the
air filter). (Refer to
"17. Maintenance and service" on page 46
and "Maintenance" in the indoor unit manual.)
3
The system operates but cooling or heating is insufficient:
Check if air inlet or outlet of outdoor or indoor unit is not
blocked by obstacles.
Remove any obstacle and make it well-ventilated.
Check if the air filter is not clogged (refer to "Maintenance" in
the indoor unit manual).
Check the temperature setting.
Check the fan speed setting on your user interface.
Check for open doors or windows. Shut doors and windows
to prevent wind from coming in.
Check if there are too many occupants in the room during
cooling operation. Check if the heat source of the room is
excessive.
Check if direct sunlight enters the room. Use curtains or
blinds.
Check if the air flow angle is proper.
If after checking all above items, it is impossible to fix the problem
yourself, contact your installer and state the symptoms, the complete
model name of the air conditioner (with manufacturing number if
possible) and the installation date (possibly listed on the warranty
card).
11. After-sales service and warranty
11.1. Warranty period
This product includes a warranty card that was filled in by the
dealer at the time of installation. The completed card has to be
checked by the customer and stored carefully.
If repairs to the air conditioner are necessary within the warranty
period, contact your dealer and keep the warranty card at hand.
11.2. After-sales service
11.2.1. Recommendations for maintenance and inspection
Since dust collects when using the unit for several years,
performance of the unit will deteriorate to some extent. As taking
apart and cleaning interiors of units requires technical expertise and
in order to ensure the best possible maintenance of your units, we
recommend to enter into a maintenance and inspection contract on
top of normal maintenance activities. Our network of dealers has
access to a permanent stock of essential components in order to
keep your air conditioner in operation as long as possible. Contact
your dealer for more information.
When asking your dealer for an intervention, always state:
The complete model name of the air conditioner.
The manufacturing number (stated on the nameplate of the unit).
The installation date.
The symptoms or malfunction, and details of the defect.
11.2.2. Recommended inspection and maintenance cycles
Be aware that the mentioned maintenance and replacement cycles
do not relate to the warranty period of the components.
Table 1: "Inspection Cycle" and "Maintenance Cycle" list
Table 1 assumes the following conditions of use:
Normal use without frequent starting and stopping of the unit.
Depending on the model, we recommend not starting and
stopping the machine more than 6 times/hour.
Operation of the unit is assumed to be 10 hours/day and 2,500
hours/year.
Table 1
WARNING
Stop operation and shut off the power if anything
unusual occurs (burning smells etc.).
Leaving the unit running under such circumstances may
cause breakage, electric shock or fire. Contact your dealer.
WARNING
Do not modify, disassemble, remove, reinstall or
repair the unit yourself as incorrect dismantling or
installation may cause an electric shock or fire.
Contact your dealer.
In case of accidental refrigerant leaks, make sure
there are no naked flames. The refrigerant itself is
entirely safe, non-toxic and non-combustible, but it will
generate toxic gas when it accidentally leaks into a
room where combustible air from fan heaters, gas
cookers, etc. is present. Always have qualified service
personnel confirm that the point of leakage has been
repaired or corrected before resuming operation.
Component
Inspection
cycle
Maintenance cycle
(replacements and/or
repairs)
Electric motor
1 year
20,000 hours
PCB
25,000 hours
Heat exchanger
5 years
Sensor (thermistor, etc.)
5 years
User interface and switches
25,000 hours
Drain pan
8 years
Expansion valve
20,000 hours
Solenoid valve
20,000 hours
Summary of Contents for RXYQQ8T7Y1B
Page 65: ......
Page 66: ......
Page 67: ......
Page 68: ...4P345099 1 2013 04 Copyright 2013 Daikin 4P345099 1 0000000S...