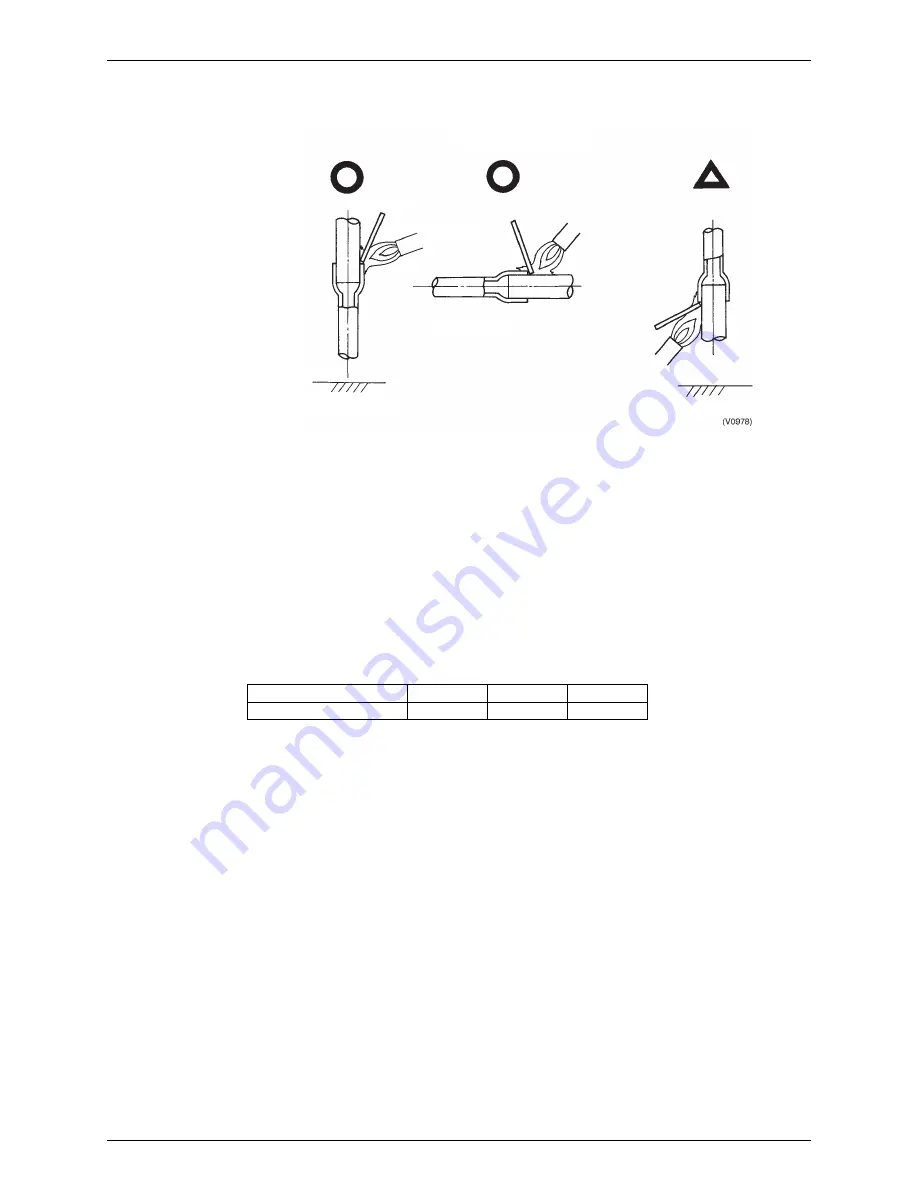
SiEN34-705
Installation
General Information
29
Brazing
a) Brazing work should be carried out such that the final result is directed either downwards or
sideways. An upward direction should be avoided wherever possible. (to prevent leakage)
b) Liquid and gas pipe branches should always be dealt with in the specified way with attention
being paid to the direction of the fitting and its angle. (to prevent oil return or drift)
For example see page 200.
c) It is standard working practice to use the nitrogen replacement method when brazing.
Important points
1. Every effort must be made to avoid fire. (Clean area where brazing is to be performed and
make sure that fire fighting equipment and water are ready to hand.)
2. Be careful of burns.
3. Make sure that the gap between the pipe and the joint is correct. (To prevent leaks)
4. Is the pipe adequately supported?
!
As a rule the gaps between supports for horizontal piping (copper pipe) are as follows:
!
The copper pipe should not be secured directly by metal brackets.
Copper pipe support spacing
(From HASS 107-1977)
Nominal diameter
20 or less
25~40
50
Maximum gap (m)
1.0
1.5
2.0
Recommended method
Downward facing
Side facing
Burner
Solder
Upward facing