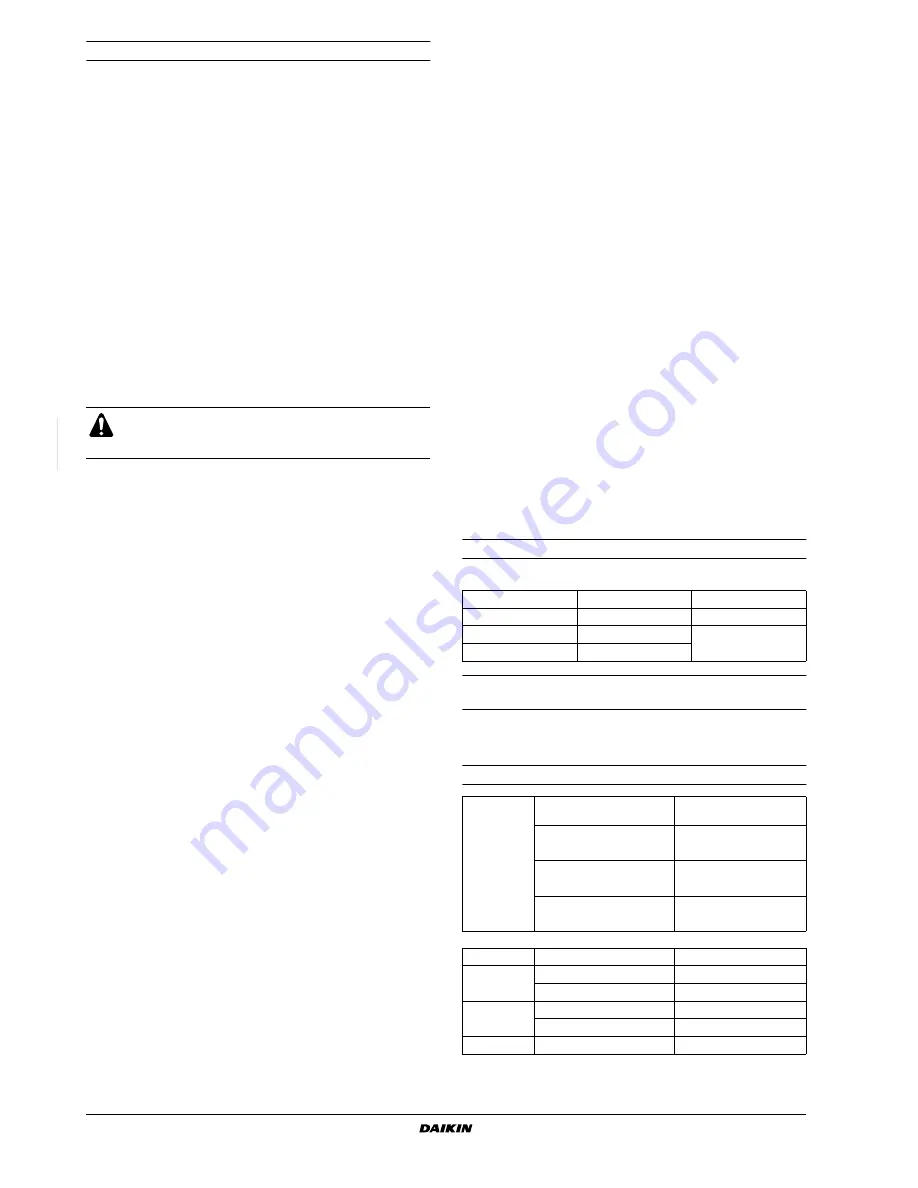
Installation manual
5
R(Y)(P)71~125B7
Split System air conditioners
4PW10931-1B
In case of simultaneous operation system
■
Upward and downward piping should be performed at the main
piping line.
■
Use branch piping kit (optional) for branching refrigerant pipes.
Precautions to be taken. (For details, refer to the manual attached to
branch piping kit.)
-
Install the branch pipes horizontally. (Maximum inclination:
20° or less)
-
Length of branch pipe to the indoor unit should be as short as
possible.
-
Try to keep lengths of both branch pipes to the indoor unit
equal.
E
VACUATING
The units were checked for leaks by the manufacturer.
The refrigerant lines fitted in site are to be checked for leaks by the
fitter.
Confirm that the valves are firmly closed before pressure test or
vacuuming.
Air tight test and vacuum drying (take special care for R407C units):
see
figure 7
■
Air tight test: make sure to use nitrogen gas. Pressurize the
liquid and gas pipes to 3.3 MPa (do not pressurize more than
3.3 MPa). If the pressure drops, check where the nitrogen
comes from.
■
Vacuum drying: use a vacuum pump which can evacuate to
-100.7 kPa (5 Torr, -755 mmHg).
-
Evacuate the system from the liquid and gas pipes by using a
vacuum pump for more than 2 hours and bring the system to
-100.7 kPa. After keeping the system under that condition for
more than one hour, check if the vacuum gauge rises or not.
If it rises, the system may either contain moisture inside or
have leaks.
-
Following should be executed if there is a possibility of
moisture remaining in the pipe (if piping work is carried out
during the raining season or over a long period of time,
rainwater may enter the pipe during work).
-
After evacuating the system for 2 hours, pressurize the
system to 0.05 MPa (vacuum break) with nitrogen gas and
evacuate the system again using the vacuum pump for
1 hour to -100.7 kPa (vacuum drying). If the system cannot
be evacuated to -100.7 kPa within 2 hours, repeat the
operation of vacuum break and vacuum drying. Then after
leaving the system in vacuum for 1 hour, confirm that the
vacuum gauge does not rise.
Leak test
1
Evacuate the pipes and check vacuum. (No pressure increase
for 1 minute.)
2
Break the vacuum with a minimum of 2 bar of nitrogen.
3
Conduct leak test by applying soap water, etc. to the connecting
part of the pipes.
4
Discharge nitrogen.
5
Evacuate and check vacuum again.
6
Open the stop valve and inject the refrigerant into the refrigerant
pipe and into the indoor unit.
7
Leak test must satisfy EN 378-2.
C
HARGING
REFRIGERANT
This unit requires additional charging of refrigerant according to the
length of pipe connected at the site. Concerning R407C refrigerant:
charge the refrigerant to the liquid pipe in its liquid state. Since
R407C is a mixed refrigerant, its composition changes if charged in a
state of gas and normal system operation would no longer be
assured.
Concerning L1~L4 (see following tables), refer to
figure 2
~
figure 4
.
Additional charging of refrigerant
Find the correct amount of additional refrigerant to charge 'G' (kg)
using one of the following formulas.
Pair system: see
figure 2
L1 (m) .................... one way length of liquid pipe
Simultaneous operation system
(Twin: see
figure 3
, Triple: see
figure 4
)
L1 (m) .................... one way length of main liquid pipe
L2~L4 (m) .............. one way length of branched liquid pipes
R407C:
Do not purge the air with refrigerants. Use a vacuum pump
to vacuum the installation. No additional refrigerant is
provided for air purging.
A
Pair system
B
Simultaneous operation system
1
Pressure gauge
2
Nitrogen
3
Refrigerant
4
Weighing machine
5
Vacuum pump
6
Stop valve
7
Main pipe
8
Branched pipes
9
Pipe branching kit (optional)
R407C
R22
R(P)71~125
G = (L1-30) x 0.025
G= (L1-7.5) x 0.03
RY(P)71
G = (L1-30) x 0.045
G= (L1-7.5) x 0.05
RY(P)100,125
G = (L1-30) x 0.07
R(Y)P71-
100-125
L1
≥
30 m
G = (L1-30 m) x A + L2
x A +L3 x A + L4 x A
L1< 30 m
G = (L1+ L2 - 30 m) x A
(L2) + L3 x A + L4 x A
& L1 + L2
≥
30 m
L1 + L2 < 30 m
G = (L1+ L2 + L3 - 30 m)
x A (L3) + L4 x A
& L1 + L2 + L3
≥
30 m
L1 + L2 + L3 < 30 m
G = (L1+ L2 + L3 + L4 -
30 m) x A (L4)
& L1 + L2 + L3 + L4
≥
30 m
Branched pipe
A
R(Y)P71
Ø 9.5
0.045 kg/m
Ø 6.4
0.03 kg/m
R(Y)P100
Ø 9.5
0.07 kg/m
Ø 6.4
0.03 kg/m
R(Y)P125
Ø 9.5
0.025 kg/m