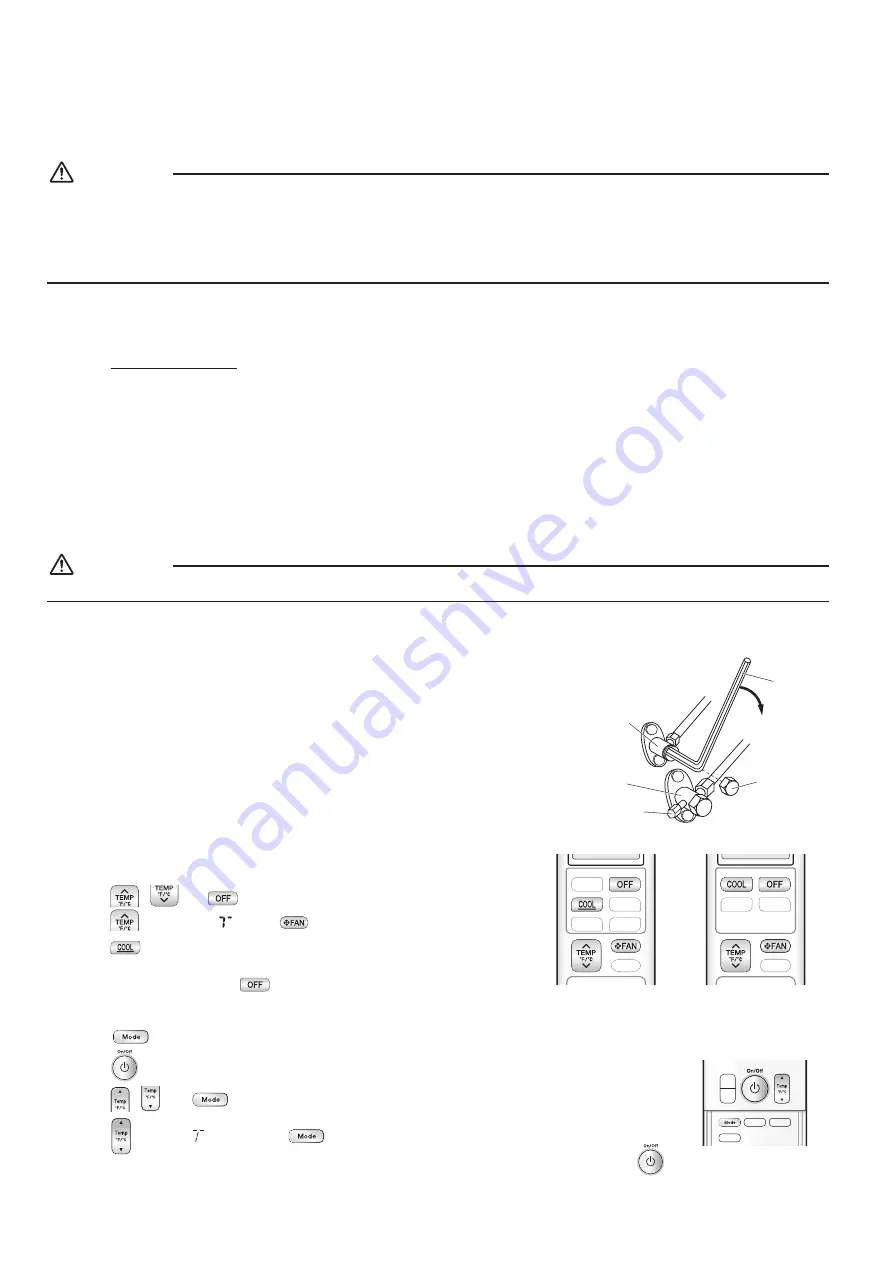
11
■
English
Facility Setting*
(cooling at low outdoor temperature)
CAUTION
• If the outdoor unit is installed where the heat exchanger of the unit is exposed to direct wind, provide a windbreak wall.
• Intermittent noises may be produced by the indoor unit due to the outdoor fan turning on and off when using facility settings.
•
Do not place humidifiers or other items which might raise the humidity in rooms where facility settings are being used.
A humidifier might cause dew condensation from the indoor unit outlet vent.
• Cutting jumper 6 (J6) sets the indoor fan tap to the highest position. Notify the user about this.
This function is limited only for facilities (the target of air conditioning is equipment (such as computer)).
Never use it in a residence or office (the space where there is a human).
*Only for RX, RK, and RXL models.
Cutting jumper 6 (J6) on the circuit board will expand the operation range down to 5°F (–15°C). However it will stop if the
outdoor temperature drops below –4°F (–20°C) and start back up once the temperature rises again.
1) Remove the top plate of the outdoor unit. (09/12 class: 3 screws, 15/18/24 class: 6 screws)
2) Remove the front plate. (09/12 class: 4 screws, 15/18/24 class: 8 screws)
3) Cut the jumper (J6) of the PCB inside.
Pump Down Operation
CAUTION
• When pressing the switch, do not touch the terminal block. It has a high voltage, and touching it could cause electric shock.
In order to protect the environment, be sure to pump down when relocating or disposing of the unit.
1) Remove the valve cap from the liquid stop valve and gas stop valve.
2) Begin forced cooling operation.
3) After 5 to 10 minutes, close the liquid stop valve with a hexagonal wrench.
4) After 2 to 3 minutes, close the gas stop valve and stop forced cooling operation.
5) Attach the valve cap once procedures are complete.
Forced cooling operation
Using the indoor unit ON/OFF switch
Press the indoor unit ON/OFF switch for at least 5 seconds. (The operation will start.)
• Forced cooling operation will stop automatically after about 15 minutes.
To stop the operation, press the indoor unit ON/OFF switch.
Gas
stop valve
Valve cap
Hexagonal
wrench
Close
Liquid
stop valve
Service port
Using the indoor unit’s remote controller
[For wall mounted units]
1) Press
,
and
at the same time.
2) Press
, then select , press
.
3) Press
to turn on the system.
• Forced cooling operation will stop automatically after about 30 minutes.
To stop the operation, press
.
HEAT PUMP model
COOLING ONLY model
[For floor standing units]
1) Press
and select the COOL operation.
2) Press
to turn on the system.
3) Press
,
and
at the same time.
4) Press
, select “
”, and press
for confirmation.
• Forced cooling operation will stop automatically after about 30 minutes. To stop the operation, press
.
01_EN_3P572321-3.indd 11
2019/06/19 14:17:28