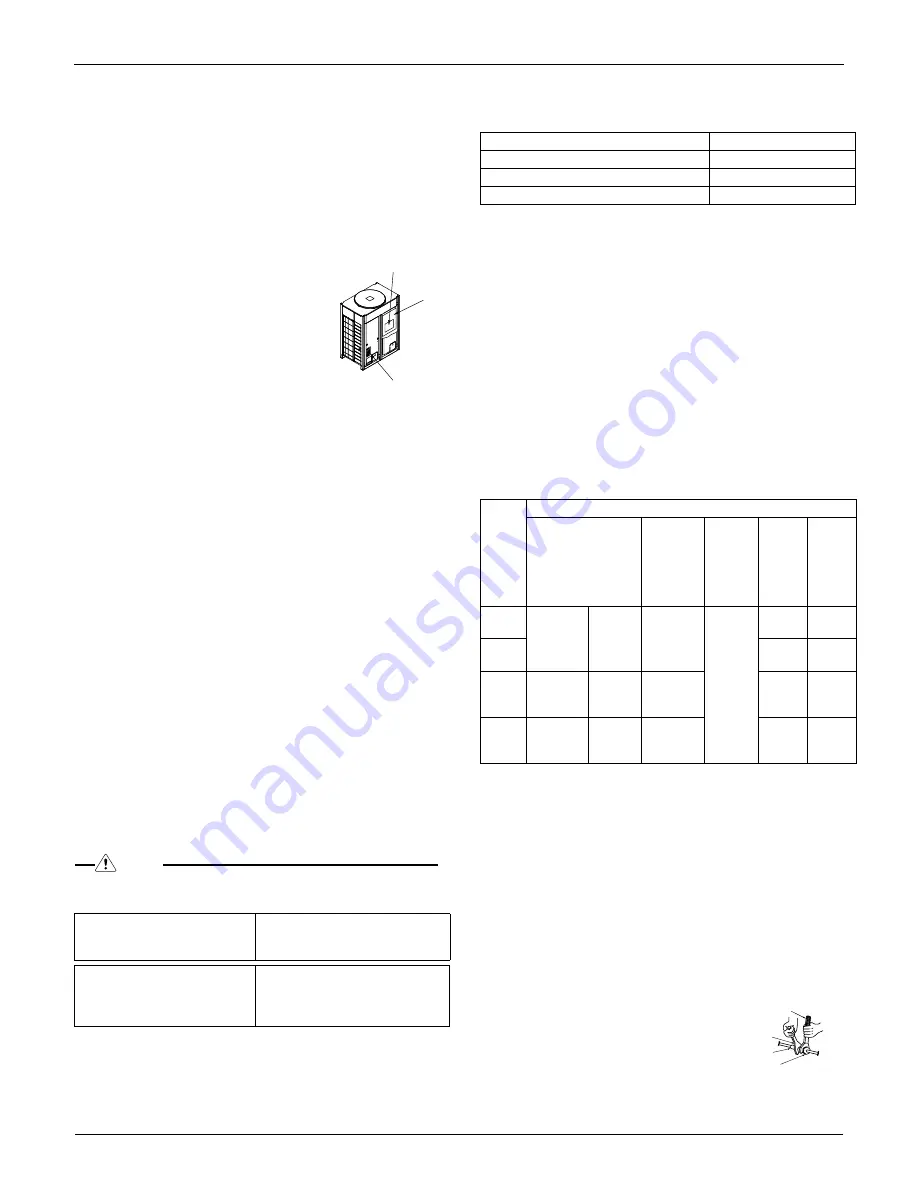
EDUS39-605
Installation
Installation of Outdoor Units
50
7.
Leak test and vacuum drying
Ensure units were checked for leaks by the manufacturer.
Confirm that the valves are firmly closed before pressure test
or vacuuming.
To prevent entry of any impurities and to ensure sufficient
pressure resistance, always use the specific tools for R-410A.
Air tight test and vacuum drying
•
Air tight test: Make sure to use nitrogen gas.
For the service port location, refer to the
[CAUTION]
label attached on the right
front panel of the outdoor unit.
Refer to figure to right:
1.
[
Service precautions
]
Label location
2.
Electric parts box lid
3.
[
Caution
]
Label location
Pressurize the liquid, suction gas, and discharge gas pipes
to 551 psi (do not pressurize more than 551 psi). If the
pressure does not drop within 24 hours, the system passes
the test. If the pressure drops
,
check where the nitrogen
leaks from.
•
Vacuum drying: Use a vacuum pump that can evacuate to
–14.6 psi.
1.
Evacuate the system from the liquid, suction gas, and
discharge gas pipes by using a vacuum pump for more
than 2 hours and bring the system to –14.6 psi. After
keeping the system under that condition for more than 1
hour, check if the vacuum gauge rises or not. If it rises,
the system may either contain moisture inside or have
leaks.
2.
if piping work is carried out during the rainy season or
over a long period of time, rainwater may enter the pipe
during work. Any possibility of moisture remaining inside
the pipe requires the following action:
After evacuating the system for 2 hours, pressurize the
system to 7.25psi (vacuum break) with nitrogen gas and
evacuate the system again using the vacuum pump for 1
hour to –14.6 psi (vacuum drying). If the system cannot
be evacuated to –14.6 psi within 2 hours, repeat the
operation of vacuum break and vacuum drying.
After leaving the system in vacuum for 1 hour, confirm
that the vacuum gauge does not rise.
NOTE
Make sure to perform air-tight test and vacuum drying using the ser-
vice ports of the stop valve shown in the table below.
Stop valve operation procedure:
Confirm the sizes of the stop valves connected to the system referring
to the following table:
Opening the stop valve:
1.
Remove the cap and turn the valve counterclockwise with
the hexagon wrench.
2.
Turn it until the shaft stops.
Do not apply excessive force to the stop valve. Doing so
may break the valve body, as the valve is not a backseat
type. Always use the special tool.
3.
Make sure to tighten the cap securely.
Closing stop valve:
1.
Remove the cap and turn the valve clockwise with the
hexagon wrench.
2.
Securely tighten the valve until the shaft contacts the main
body seal.
3.
Make sure to tighten the cap securely.
Tightening torque:
(Refer to figure 22 page 39)
1.
Service port
2.
Cap
3.
Hexagon hole
4.
Shaft
5.
Seal
CAUTION:
•
Always use a charge hose for service port connection.
•
After tightening the cap, check that no refrigerant leaks are
present.
•
When loosening a flare nut, always use two wrenches in
combination. When connecting the piping, always use a
spanner and torque wrench in combination to tighten the
flare nut.
•
When connecting a flare nut,
coat the flare (inner and outer
faces) with ether oil or ester oil
and handtighten the nut 3 to 4
turns initially.
One outdoor unit installed
Liquid line stop valve
Discharge gas line stop valve
Suction gas line stop valve
Multiple outdoor units installed
Liquid line stop valve
Discharge gas line stop valve
Suction gas line stop valve
Oil-equalizing line stop valve
1
3
2
Q96 type
Liquid line stop valve
φ
3/8”
Suction gas line stop valve
φ
7/8”
Discharge gas line stop valve
φ
3/4”
Stop
valve
size
Tightening torque ft.-Ibf (Turn clockwise to close)
Shaft (valve body)
Cap
(valve lid)
Service
port
Flare nut
Suction
gas line
piping
attached
to unit
(1)
1/4”
3.98-4.87
Hexagon
wrench
4 mm
9.96-12.17
8.48-
10.25
10.3-
12.5
—
3/8”
24.1-
29.4
—
3/4”
9.96-12.17
Hexagon
wrench
6mm
17.33-
20.28
71.6-
87.8
—
7/8”
19.91-
24.34
Hexagon
wrench
10mm
26.55-
32.45
—
16.23-
20.65
Torque wrench
Spanner
Piping union
Flare nut