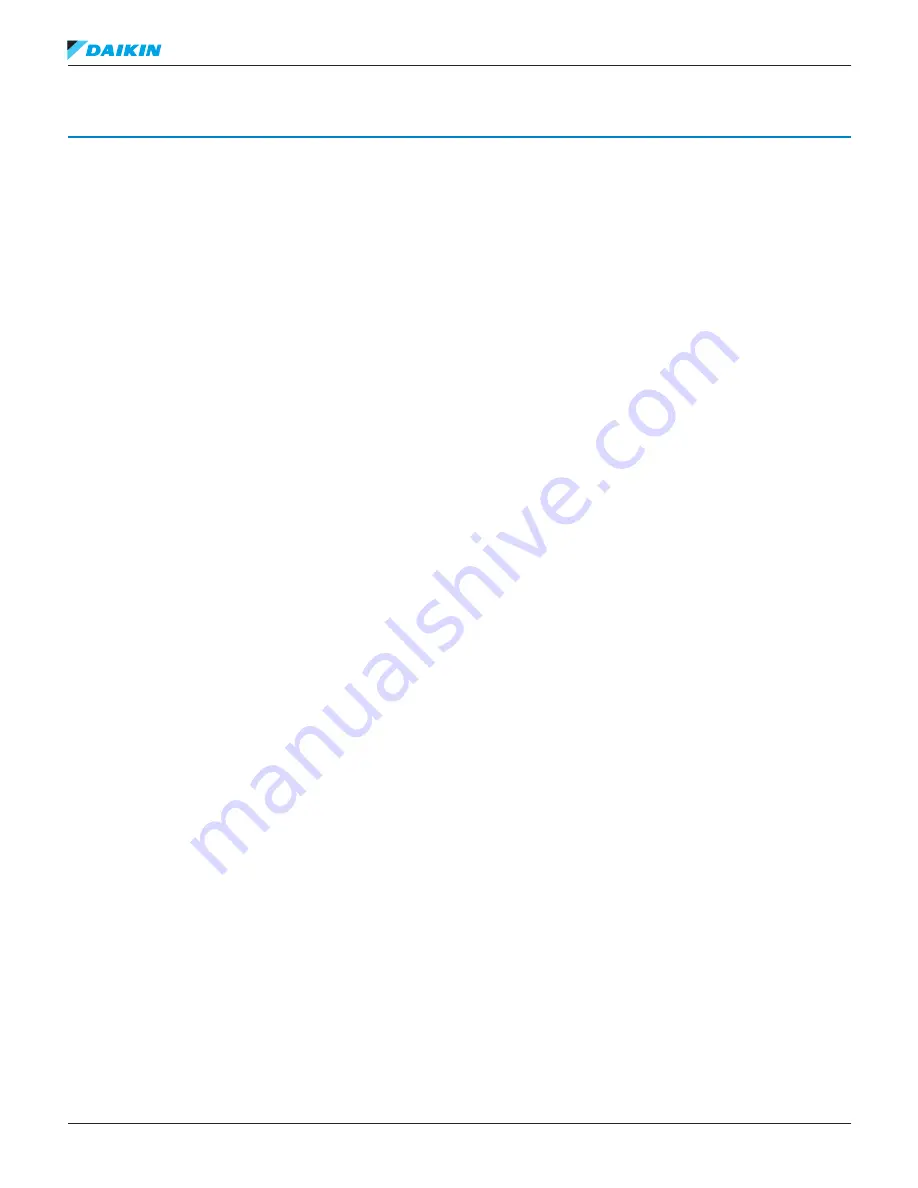
www.DaikinApplied.com 33
AG 31-011 • REFRIGERANT PIPING DESIGN
Installation Details
Pump Down
Some air conditioning systems are designed with either
recycling or a one-time pumpdown cycle. These systems
have a condenser sized large enough to hold the refrigerant
charge. When cooling is no longer required, a solenoid valve
in the liquid line closes. The compressor continues operating
until the suction pressure drops below the suction pressure
cutout switch.Once the suction pressure switch opens, the
compressor stops. One-time pump down systems stay OFF
until there is a need for cooling. Recycling pump down allows
the compressor to restart if the suction pressure switch closes,
even if cooling is unnecessary. The solenoid is still closed
(no cooling required) so the compressor will quickly lower the
suction pressure to where the pressure switch opens again. An
example of this is the Daikin Applied RPS C-vintage Applied
Rooftop System.
The advantage of pump down is that most of the refrigerant
in the evaporator is removed. Without pump down, during
the OFF cycle, the refrigerant may migrate to the evaporator
and/or suction line. On startup, the liquid refrigerant may be
drawn into the compressor and cause slugging. If the casing
of the compressor is allowed to get colder than the rest of the
circuit, refrigerant throughout the circuit may migrate to the
compressor crankcase, condense and cause flooded starts.
Systems that do not have pump down may still have a solenoid
that closes while the compressor is OFF to limit refrigerant
migration. Crankcase heaters may also be added to help
raise the compressor temperature and avoid refrigerant
condensation.
When pump down is part of the equipment design, a solenoid
valve will be required in the liquid line as shown in
. It should be installed as close to the evaporator
as possible, just before the TX valve. With pump down, the
condenser must be able to hold the system charge. Long field
refrigerant piping arrangements may increase the refrigerant
volume above the capacity of the condenser and limit service
pump down. A receiver may be added to store the refrigerant.
Consult the manufacturer if a receiver is required.
Piping Insulation
Suction lines are cold, 40°F (4.4°C) SST, and cause
condensation, even in conditioned spaces. In addition, any
heat that enters the refrigerant adds to the superheat and
reduces system efficiency. For these reasons, suction lines
should be insulated with a vapor proof insulation. This is a
requirement of many building codes. Rubratex
®
is the most
common form of refrigerant line insulation.
Liquid lines generally are insulated. They are warm to hot
(110°F [43.3°C] for air-cooled). If liquid lines pass through
a space that is warmer than the refrigerant (i.e. the roof of
a building at roof level), or if they could be considered hot
enough to pose a safety risk, then insulation should be added.
Discharge lines are generally uninsulated. They may be very
hot, in excess of 150°F (66°C), so insulation may be warranted
as a safety consideration, or if the heat loss from the discharge
gas line would be considered objectionable to the space.
Hot gas bypass lines should be insulated, especially if the runs
are long or if the piping is exposed to cold temperatures.
Refrigerant Line Installation
Refrigerant lines need to be securely installed to minimize
vibration that causes noise and damages piping. Reciprocating
compressors, in particular, cause vibration. Steel braided
flexible refrigerant lines (a must for spring isolated
reciprocating compressors) minimize this vibration. Follow
manufacturer’s instructions when using steel braided lines.
Discharge mufflers are also occasionally used on discharge
lines to minimize gas pulsations.
Refrigerant lines that rub against solid objects wear holes
through copper and create a leak. For this reason, when
refrigerant lines pass through walls, the line should pass
through sleeved openings in such a manner that the lines do
not touch.
There are several commercially available pipe clamping
systems that allow pipes to be held rigid without causing
damage to them. Most include some form of rubber grommet
around the pipe, which is then secured within a bracket. Many
building codes specify minimum support spacing.
Piping should also be protected from mechanical damage.
Where piping is exposed to possible damage, the lines should
be routed out of the way or be protected in some form of
chase. Burying refrigerant lines should be avoided.