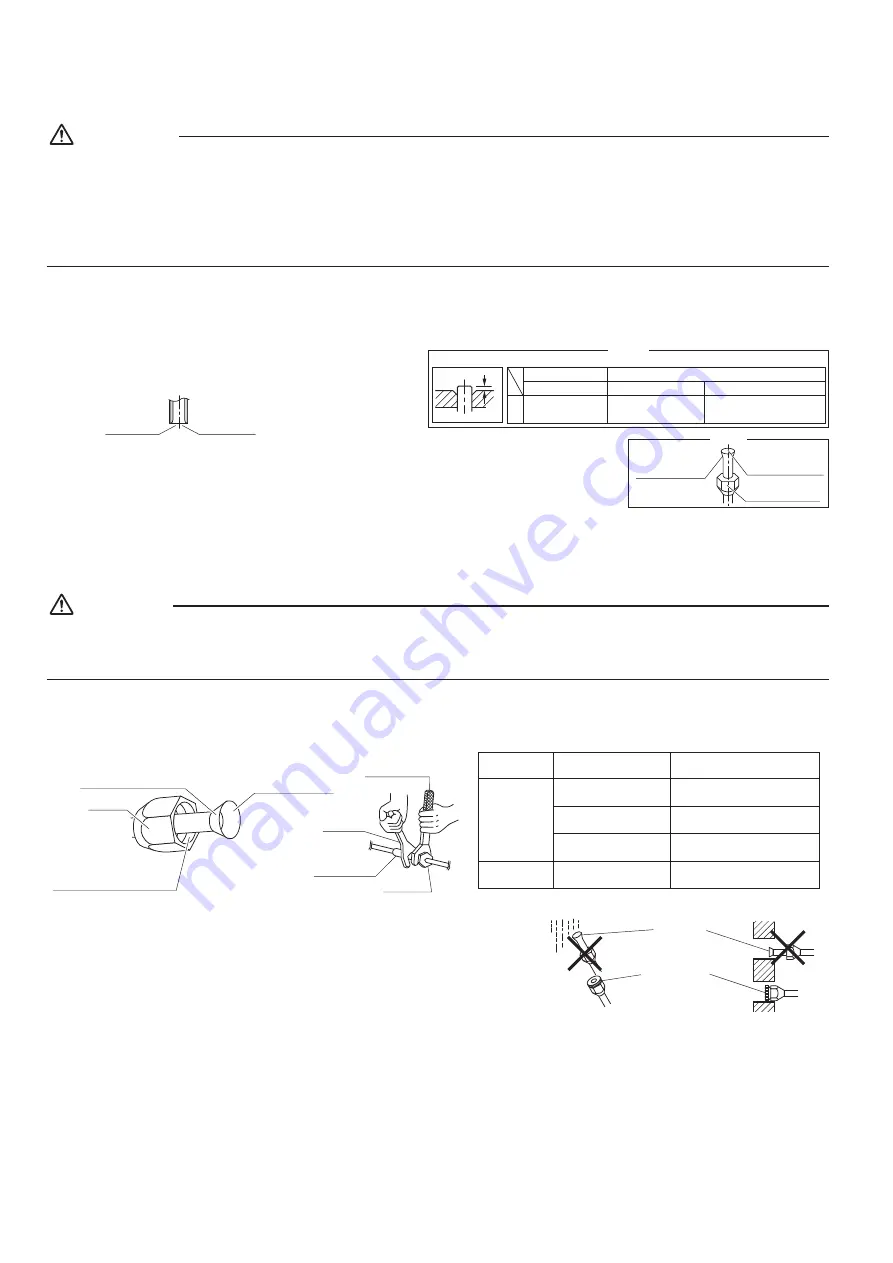
9
■
English
Refrigerant Piping Work
WARNING
•
Do not apply mineral oil to the flare.
• Prevent mineral oil from getting into the system as this would reduce the service life of the units.
• Never use piping which has been used for previous installations. Only use parts which are delivered with this unit.
• Never install a dryer to this R410A unit in order to guarantee its service life.
• The drying material may dissolve and damage the system.
•
Improper flaring may result in refrigerant gas leakage.
1�
Flaring the pipe end
1) Cut the pipe end with a pipe cutter.
2) Remove burrs with the cut surface facing downward,
so that the filings do not enter the pipe.
Remove burrs.
Cut exactly at
right angles.
3)
Put the flare nut on the pipe.
4) Flare the pipe.
5)
Check that the flaring has been done correctly.
Set exactly at the position shown below.
Flaring
A
A
0-0.020 inch
(0-0.5mm)
Clutch-type
Flare tool for R410A
0.039-0.059 inch
(1.0-1.5mm)
Clutch-type (Rigid-type)
0.059-0.079 inch
(1.5-2.0mm)
Wing-nut type (Imperial-type)
Conventional flare tool
Check
The flare's inner
surface must be
flaw-free.
The pipe end must
be evenly flared in
a perfect circle.
Make sure that the
flare nut is fitted.
Die
2�
Refrigerant piping
CAUTION
•
Use the flare nut fixed to the main unit. (This is to prevent the flare nut from cracking as a result of deterioration over time.)
•
To prevent gas leakage, apply refrigeration oil only to the inner surface of the flare. (Use refrigeration oil for R410A.)
•
Use a torque wrench when tightening the flare nuts to prevent damage to the flare nuts and gas leakage.
•
Align the centers of both flares and tighten the flare nuts 3 or 4 turns by hand, then tighten them fully with a spanner and a
torque wrench.
Do not apply refrigeration
oil to the outer surface.
Flare nut
Apply refrigeration
oil only to the inner
surface of the flare.
Do not apply refrigeration oil to
the flare nut to avoid tightening
with excessive torque.
Apply oil
Torque wrench
Piping union
Flare nut
Spanner
Tighten
Gas side
Piping size
O.D.
3/8 inch
(9.5mm)
O.D.
1/2 inch
(12.7mm)
O.D.
5/8 inch
(15.9mm)
O.D.
1/4 inch
(6.4mm)
24-1/8 – 29-1/2Ibf • ft
(32.7-39.9N • m)
36-1/2 – 44-1/2lbf • ft
(49.5-60.3N • m)
45-5/8 – 55-5/8Ibf • ft
(61.8-75.4N • m)
10-1/2 – 12-3/4lbf • ft
(14.2-17.2 N • m)
Flare nut tightening torque
Liquid side
Caution on piping handling
• Protect the open end of the pipe against dust and moisture.
• All pipe bends should be as gentle as possible. Use a pipe bender for bending.
Wall
If no flare cap is
available, cover
the flare mouth
with tape to keep
dirt and water out.
Be sure to
place a cap.
Rain
01_EN_3P654325-1B.indd 9
2021/08/27 13:37:34