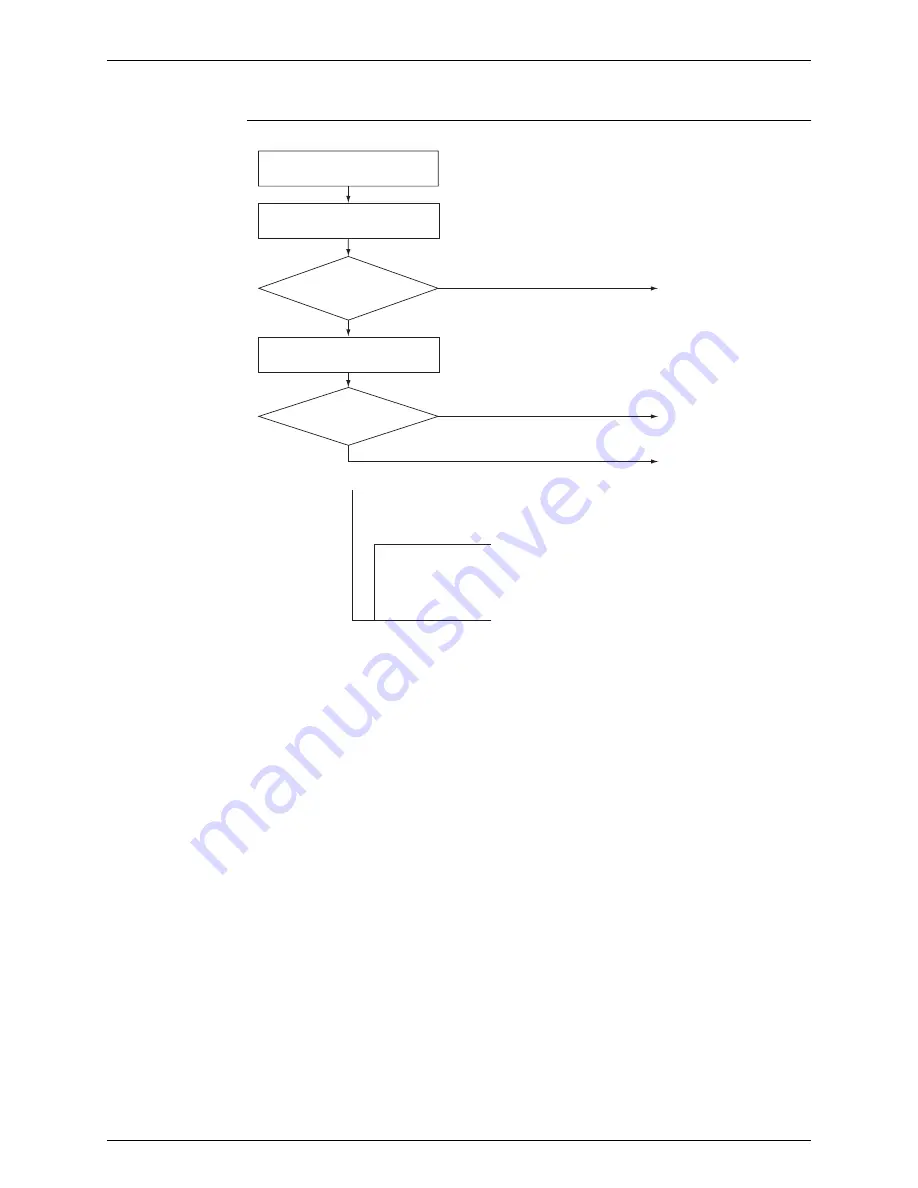
SiENBE04-507A
Check
Service Diagnosis
145
5.1.3 Four Way Valve Performance Check
Check No.5
Turn off the power and turn it on
again.
Start the heating-mode run.
Replace the outdoor unit
PCB.
Replace the four way valve
coil.
Replace the four way valve.
(R3047)
Four way valve
coil resistance at
3k
Ω
±0.5k
Ω
?
S80 voltage
at DC 180-220 V with
compressor on?
(Fig. 1)
Disconnect the four way valve coil
from the connector and check the
continuity.
∗
Four way valve coil
Cooling / dry : No continuity
Heating
:
Continuity
YES
YES
NO
NO
(Fig. 1)
Voltage at S80
DC180-220V
Time
Compressor
ON
Summary of Contents for FTKS20DVMW(L)
Page 10: ...SiENBE04 507A List of Functions 1 Part 1 List of Functions 1 List of Functions 2...
Page 85: ...Control Specification SiENBE04 507A 76 Function and Control...
Page 159: ...Check SiENBE04 507A 150 Service Diagnosis...
Page 215: ...Others SiENBE04 507A 206 Others...
Page 221: ...Wiring Diagrams SiENBE04 507A 212 Appendix...
Page 225: ...SiENBE04 507A iv Index...