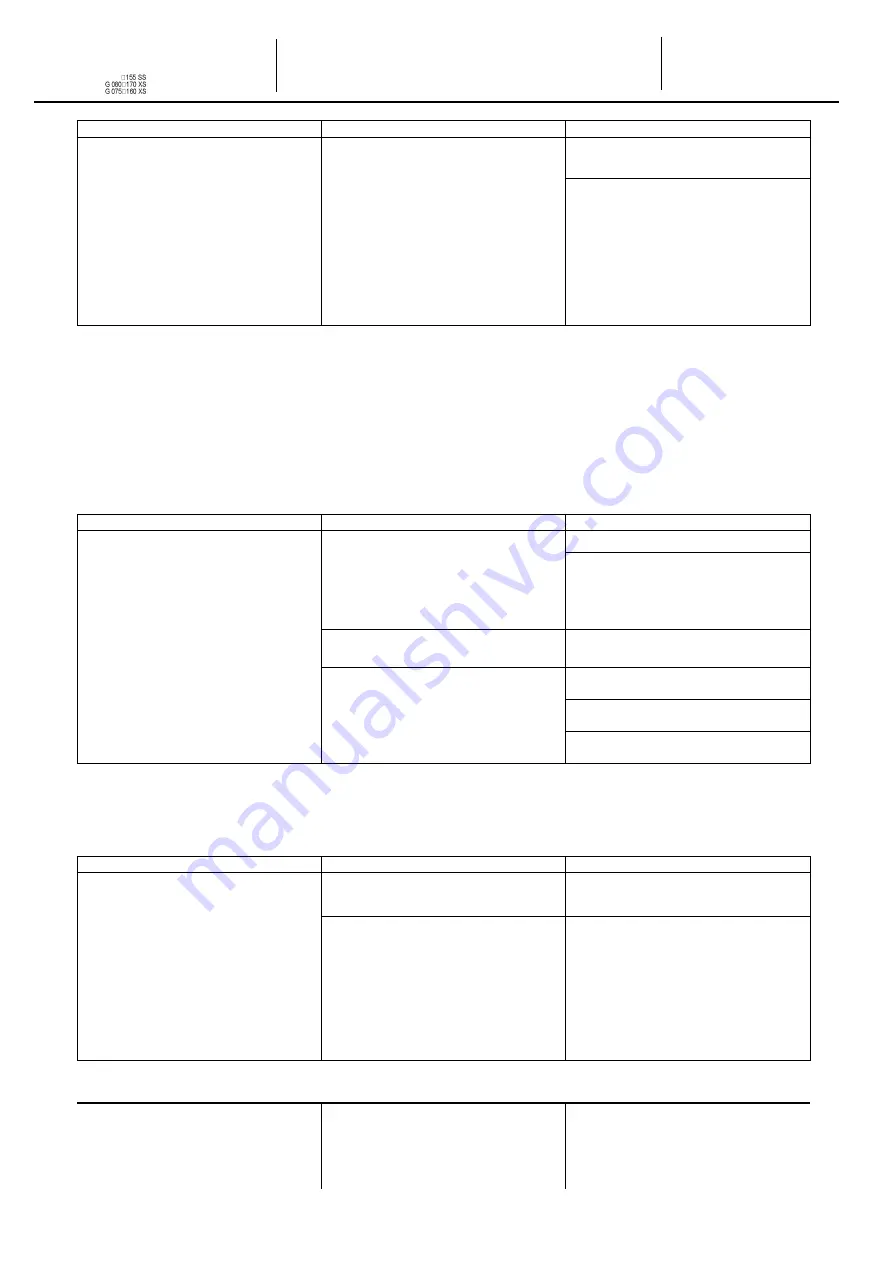
EWWQ090G ÷ EWWQ720L - R410A - Water-cooled scroll chillers
EWLQ090G ÷ EWLQ720L - R410A - Condenser less
EWHQ100G ÷ EWHQ400G - R410A - Heat pump scroll chillers
EWAQ-G 075
- R410A - Air-cooled scroll chillers
EWAQ-
- R410A - Air-cooled scroll chillers
EWYQ-
- R410A - Air-cooled scroll heat pumps
Air and Water cooled scroll chillers & heat pump
Operation
Manual
Operation Manual
72
EWWQ - EWLQ - EWHQ
EWAQ - EWYQ
Air or Water cooled scroll chiller &
heat pump
D-EOMHW00107-15EN
Symptom
Cause
Solution
Unit status is Off.
All circuits are stopped immediately.
B
ell icon is moving on controller’s
display.
Led on the button 2 of External HMI is
blinking
String in the alarm list:
UnitOff ExternalAlm
String in the alarm log:
UnitOff ExternalAlm
String in the alarm snapshot:
UnitOff External Alm
There is an external alarm that has
caused the opening, for at least 5
seconds, of the port on the option
module POL965 with address 18.
Check causes of the external alarm.
Check electrical wiring from unit
controller to the external equipment in
case of any external events or alarms
have been occurred.
6.1.4 Master Slave Alarm
The following alarms are related to the function Master Slave.
6.1.4.1 Common Evaporator Leaving Water Temperature sensor fault
This alarm can occurs when the sensor used to measure the common leaving water temperature is
broken or not connected to the chiller defined master.
Symptom
Cause
Solution
Every unit in the Master Slave
Network works in local mode.
Bell icon is moving on master
controller’s display.
Led on the button 2 of the master
External HMI is blinking
String in the alarm list:
+Common LWTSen
String in the alarm log:
Common LWTSen
String in the alarm snapshot:
Common LWTSen
Sensor is broken.
Check for sensor integrity.
Check correct sensors operation
according information about kOhm
(k
) range related to temperature
values.
Sensor is shorted.
Check if sensor is shorted with a
resistance measurement.
Sensor is not properly connected
(open).
Check for absence of water or
humidity on electrical contacts.
Check for correct plug-in of the
electrical connectors.
Check for correct sensors wiring
according with wiring diagram.
6.1.4.2 Slave X Communication Alarm
This alarm displayed only on the Master unit and occurs every time that there is communication
error between Master and Slave.
Symptom
Cause
Solution
The Slave unit works in local mode.
Bell icon is moving on master
controller’s display.
Led on the button 2 of the master
External HMI is blinking
String in the alarm list:
+Slave X CommAlm
String in the alarm log:
Slave X CommAlm
String in the alarm snapshot:
Slave X CommAlm
Cable broken
Check for cable integrity
Connection wrong
Check the po/- of the
connection cable between Master
and Slave