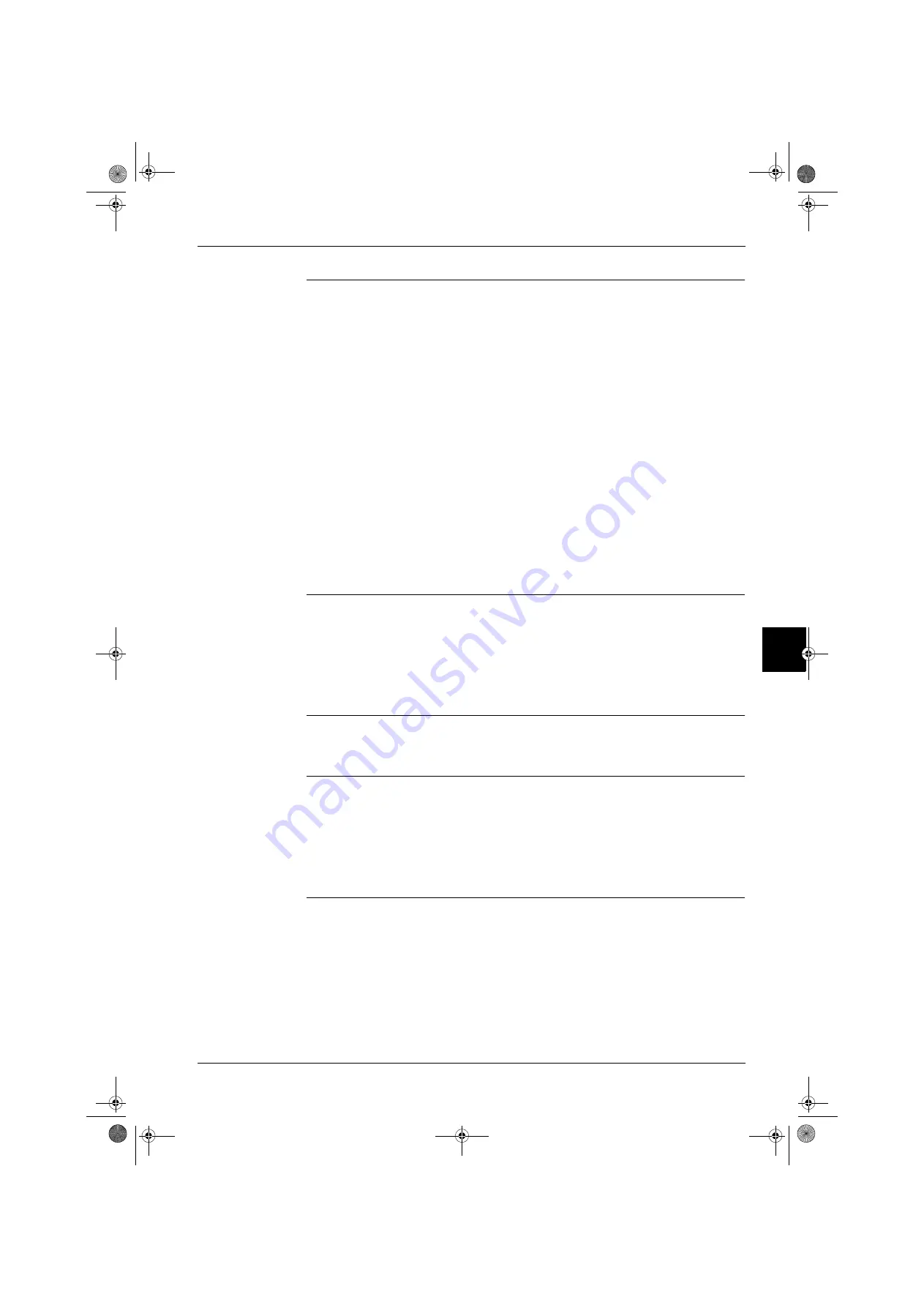
ESIE07-05
Maintenance
5–7
3
5
1
5
Filter-driers
A replacement of the filter-drier is recommended during scheduled service maintenance of the unit,
any time excessive pressure drop is read across the filter-drier and/or when bubbles occur in the
sightglass with normal subcooling. The maximum recommended pressure drop across the filter-drier
at 75% to 100% circuit loading is 70 kPa. The maximum recommended pressure drop across the
filter-drier at 25% to 50% circuit loading is 35 kPa.
The filter-drier should also be changed if the moisture indicating liquid line sightglass indicates excess
moisture by the wet system color indicators. During the first few months of operation the filter-drier
replacement may be necessary if the pressure drop across the filter-drier exceeds the values listed in
the paragraph above. Any residual particles from the unit heat transfer tubing, compressor and
miscellaneous components are swept by the refrigerant into the liquid line and are caught by the
filter-drier.
To change the filter drier, pump the unit down by moving the ON/OFF compressors switches in “off”
position. Move the ON/OFF switch unit Q0 to the “off” position. Turn off all power to the unit and install
jumpers across the terminals. This takes out the low pressure control. Close the manual liquid line
shutoff valve. Turn the power of the unit back on and restart the unit by moving the ON/OFF switch
unit Q0. The unit will start pumping down past the low pressure setting. When the evaporator pressure
reaches 0.3 bar, move switch Q0 to the “off” position. Remove the jumper.
Close the suction line valve. Remove and replace the filter-drier. Evacuate the lines through the liquid
line manual shutoff valve to remove non condensables that may have entered during filter
replacement. Open the suction line valve. A leak check is recommended before returning the unit to
operation.
Electronic
expansion valve
The EWW
Q-A
JYNN water cooled chiller is equipped with the most advanced electronic expansion
valve to achieve precise control of refrigerant mass flow. As today’s system requires improved energy
efficiency, tighter temperature control, wider range of operating conditions and incorporate new
features like remote monitoring and diagnostics, the application of electronic expansion valves
becomes mandatory. EWW
Q-A
JYNN’s electronic expansion valve proposes features that makes it
unique: short opening and closing time, high resolution, positive shut-off function to eliminate use of
additional solenoid valve, highly linear flow capacity, continuous modulation of mass flow without
stress in the refrigerant circuit and corrosion resistance stainless steel body.
Evaporator
The evaporator is a direct expansion type with refrigerant inside the copper tubes and water on the
outside. The evaporators are manufactured with carbon steel shells, high efficiency copper tubes and
polypropylene baffles. The copper tubes are roll expanded into carbon steel tube plates.
Condensers
Condensers are shell and cleanable, through-tube type (1 pass). The unit has independent
condensers, one per circuit. Each condenser has a carbon steel and seamless, integrally finned high
efficiency copper tubes, roll expanded into heavy carbon steel tube sheets. Water heads are
removable and include vent and drain plugs. Condensers come complete with liquid shut-off valve,
spring loaded relief valve.
Note: The units are furnished with 1 pass condensers as standard (water entering a side and water
leaving the opposite side of the heat exchanger).
ESIE07-05.book Page 7 Friday, December 21, 2007 3:21 PM