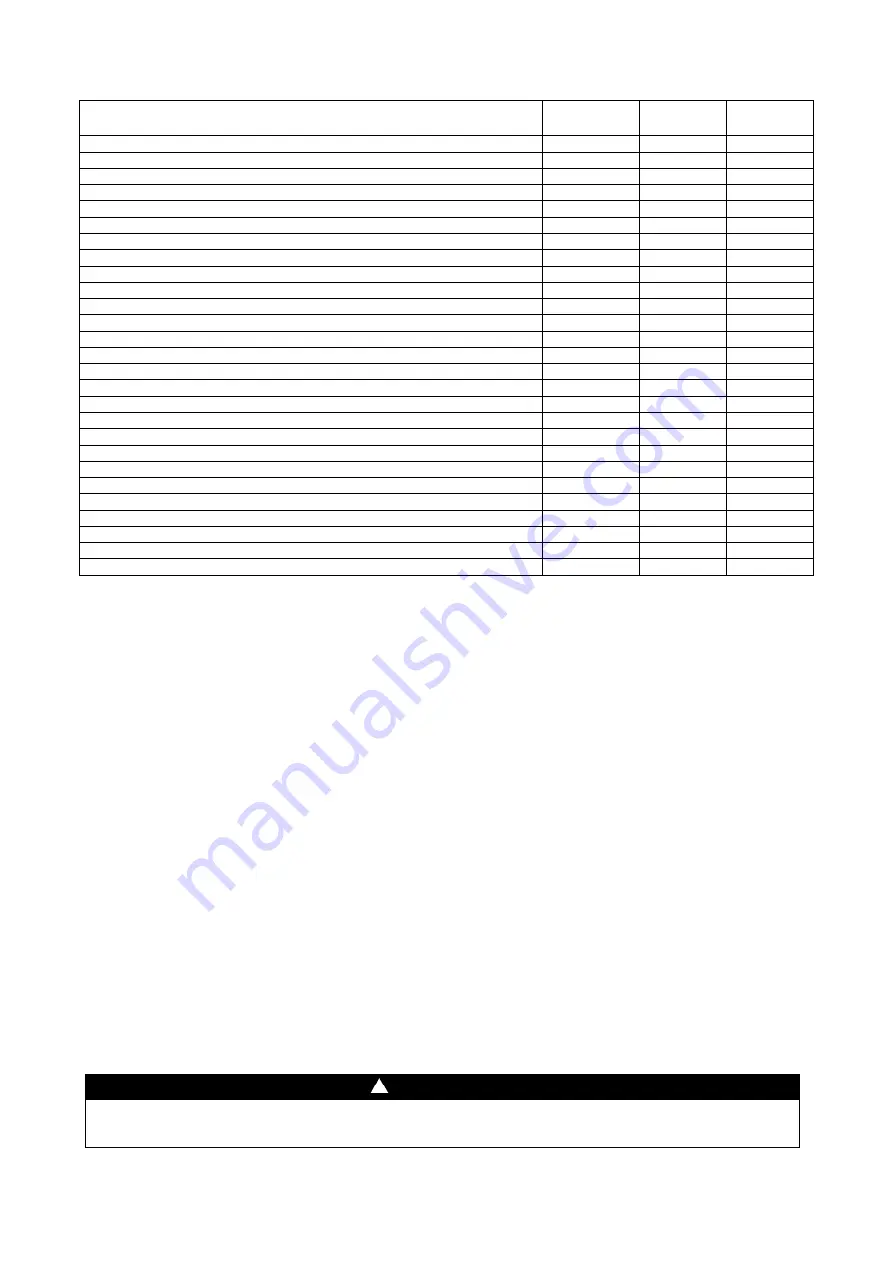
D
–EIMWC00408-16EN - 47/60
Routine maintenance
Table 6
– Routine maintenance programme
(Note 2)
Weekly
Monthly
(Note 1)
Yearly
(Note 2)
General
Reading of operating data (Note 3)
X
Visual inspection of machine for any damage and/or loosening
X
Verification of thermal insulation integrity
X
Clean and paint where necessary
X
Analysis of water (Note 5)
X
Electrical:
Verification of control sequence
X
Verify contactor wear
– Replace if necessary
X
Verify that all electrical terminals are tight
– Tighten if necessary
X
Clean inside the electrical control board
X
Visual inspection of components for any signs of overheating
X
Verify operation of compressor and electrical resistance
X
Measure compressor motor insulation using the Megger
X
Refrigeration circuit:
Check for any refrigerant leakage
X
Verify refrigerant flow using the liquid sight glass
– Sight glass full
X
Verify filter dryer pressure drop
X
Verify oil filter pressure drop (Note 4)
X
Analyse compressor vibrations
X
Analyse compressor oil acidity (Note 6)
X
Check safety valves (Note 7)
X
Condenser section:
Clean the exchangers (Note 8)
X
Notes:
1)
Monthly activities include all the weekly ones
2)
The annual (or early season) activities include all weekly and monthly activities
3)
Machine operating values should be read on a daily basis thus keeping high observation standards
4)
Replace the oil filter when the pressure drop across it reaches 2.0 bar
5)
Check for any dissolved metals
6)
TAN (Total Acid Number) :
0.10 : No action
Between 0.10 and 0.19 : Replace anti-acid filters and re-check after 1000
running hours. Continue to replace filters until the TAN is lower than 0.10.
0.19 : Change oil, replace oil filter and filter dryer. Verify at regular intervals.
7)
Safety valves
Check that the lid and seal have not been tampered with.
Check that the discharge socket of the safety valves is not obstructed by any objects, rust or ice.
Check the manufacturing date shown on the safety valve. Replace the valve every 5 years and make sure it is
compliant with the current regulations in terms of the installation of the unit.
8)
Clean the pipes of the exchanger mechanically and chemically if the following occur: drop in the condenser
water capacity, drop in the differential temperature between inlet and outlet water, high temperature
condensation
.
Replacement of filter dryer
It is strongly advised that the filter dryer cartridges be replaced in the event of a considerable pressure drop across the
filter or if bubbles are observed through the liquid sight glass while the subcooling value is within the accepted limits.
Replacement of the cartridges is advised when the pressure drop across the filter reaches 50 kPa with the compressor
under full load.
The cartridges must also be replaced when the humidity indicator in the liquid sight glass changes colour and shows
excessive humidity, or when the periodic oil test reveals the presence of acidity (TAN is too high).
Procedure to replace the filter dryer cartridge
ATTENTION
Ensure proper water flow through the evaporator during the entire servicing period. Interrupting the water flow during
this procedure would cause the evaporator to freeze, with consequent breakage of internal piping.