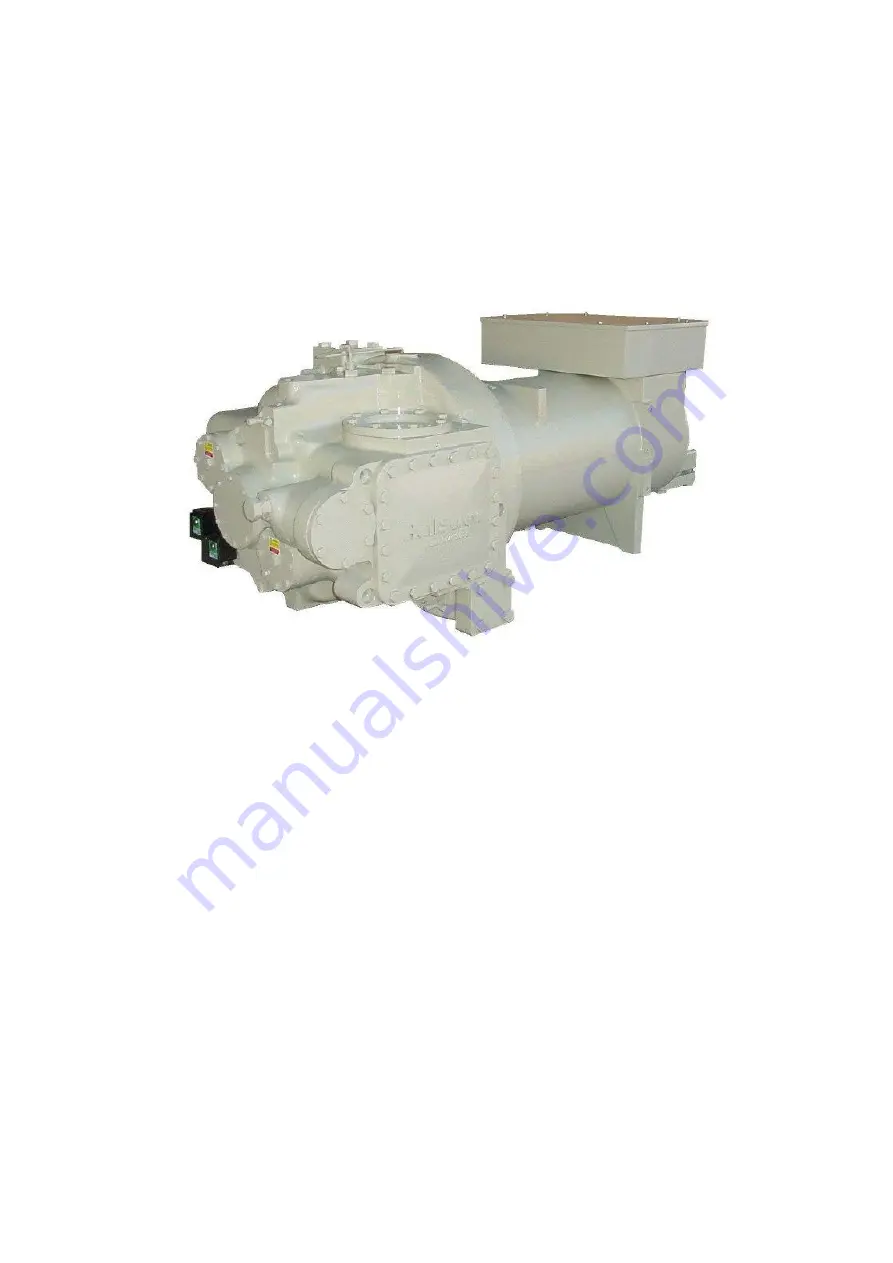
Compressor
The single-screw compressor is of the semi-hermetic type with an asyncronous three-phase, two-pole motor which is
directly splined on the main shaft. The suction gas from the evaporator cools the electric motor before entering the
suction ports. There are temperature sensors inside the electric motor which are completely covered by the coil winding
and constantly monitor motor temperature. Should the coil winding temperature become very high (120°C), a special
external device connected to the sensors and to the electronic controller will deactivate the corresponding compressor.
There are only two moving rotating parts and there are no other parts in the compressor with an eccentric and/or
alternating movement.
The basic components are therefore only the main rotor and the satellites that carry out the compression process,
meshing perfectly together.
Compression sealing is done thanks to a suitably shaped special composite material that is interposed between the main
screw and the satellite. The main shaft on which the main rotor is splined is supported by 2 ball bearings. The system
made up in this way is both statically and dynamically balanced before assembly.
Fig. 24 - Picture of Fr4100 compressor
Compression process
With the single-screw compressor the suction, compression and discharge process takes place in a continuous manner
thanks to the upper satellite. In this process the suction gas penetrates into the profile between the rotor, the teeth of the
upper satellite and the compressor body. The volume is gradually reduced by compression of the refrigerant. The
compressed gas under high pressure is thus discharged into the built-in oil separator. In the oil separator, the gas/oil
mixture and the oil are collected in a cavity in the lower part of the compressor, where they are injected into the
compression mechanisms in order to guarantee
compression’s sealing and lubrication of the ball bearings.