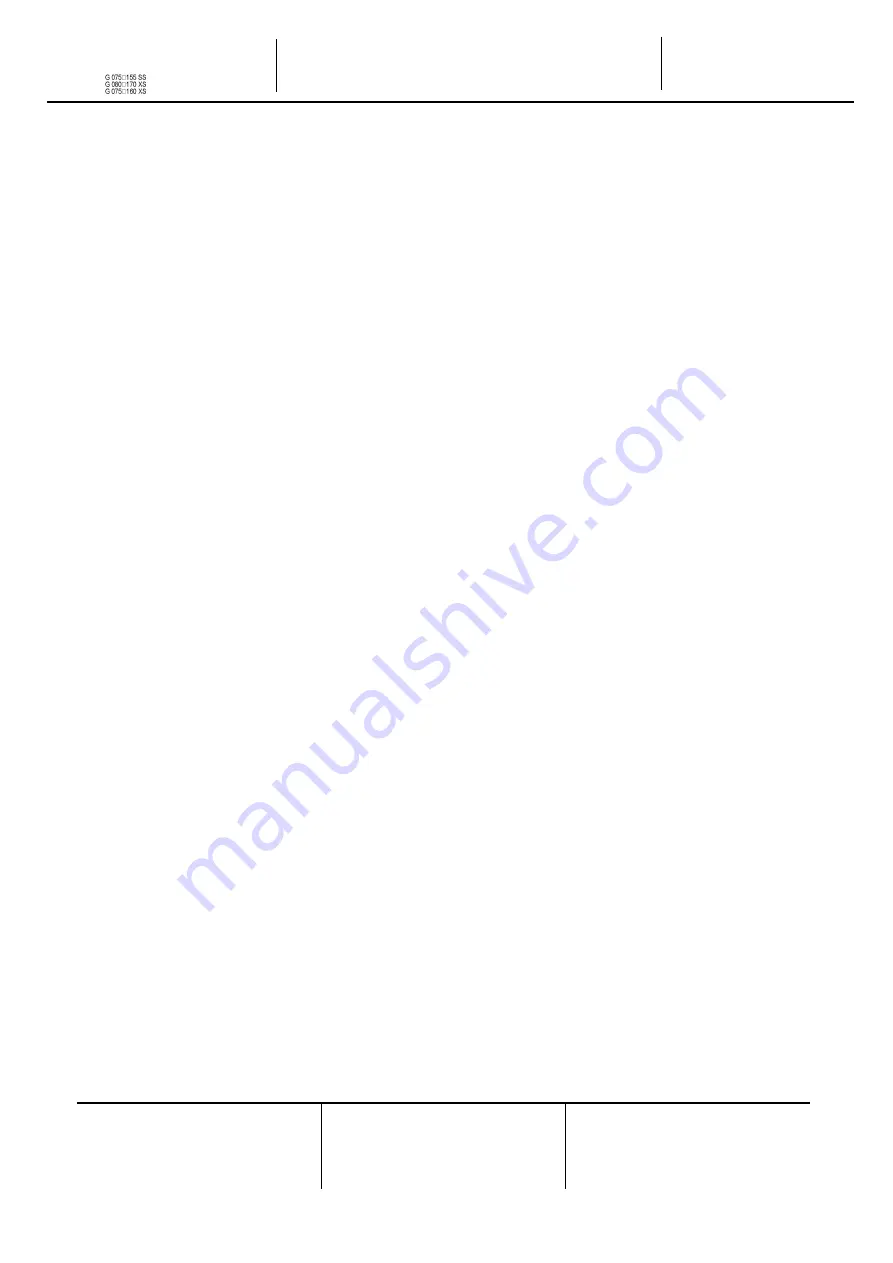
EWWQ090G ÷ EWWQ720L - R410A - Water-cooled scroll chillers
EWLQ090G ÷ EWLQ720L - R410A - Condenser less
EWHQ100G ÷ EWHQ400G - R410A - Heat pump scroll chillers
EWAQ-
- R410A - Air-cooled scroll chillers
EWAQ-
- R410A - Air-cooled scroll chillers
EWYQ-
- R410A - Air-cooled scroll heat pumps
Air and Water cooled scroll chillers & heat pump
Operation
Manual
EWWQ - EWLQ - EWHQ
EWAQ - EWYQ
Air or Water cooled scroll chiller &
heat pump
D-EOMHW00107-15EN
Operation Manual
55
5.6.2 Cond In / Cond Out (W/C only)
These two control modes are available for the following unit type:
-
Chiller
-
Heat pump with gas inversion
In this modes the controller regulates the condenser entering (Cond In) or leaving (Cond Out)
water temperature. Through the menu Unit Cond Ctrl 0 it is possible to set the water setpoints in
cool and heat modes. When one of these condensing controls is chosen the logic checks if the
setpoint is compatible with the operating area (envelope) of the compressors that depending on the
actual evaporating leaving water temperature. If necessary the condensing setpoint set by HMI is
overwritten and displayed in the item
Cnd Act SP
.
When this control is active the controller provides a unique 0-10V signal for the control of one three
way valve or one cooling tower. This means that for the Double circuit unit (Dual) the common
entering/leaving condenser water temperature will be controlled.
5.6.3 Fan Control (A/C only)
Fan control is used to keep the condenser pressure at a level that guarantee the best operation at
any ambient condition both in cool and heat mode.
In cooling mode the fan speed is controlled with a PID regulator in order to maintain the condenser
pressure at a stable value. Depending on the ambient temperature fans may not be able to
maintain the condenser pressure at the setpoint even while running at the full speed. Maximum fan
speed can be lower than 100%, this may depend on the noise class of this unit. In case an high
pressure event will activate the maximum fan speed can be forced to full speed also for low noise
units in order to prevent high pressure trips.
In heating mode the fan speed is controlled with a PID regulator in order to maintain the evaporator
pressure at a stable value. When the ambient temperature is below 15.0°C the fans are forced to
run at full speed independently from the evaporator pressure to keep the circuit operation stable
and avoid as much as possible defrosts. In heat mode the fans can reach the full speed if needed,
no limitation is applied in this case also for low noise units.
5.7 EXV Control
As a standard, the unit is equipped with one electronic expansion valve (EXV) per circuit, moved
by a stepper motor. The EXV controls the suction superheat in order to optimize evaporator
efficiency and avoid at the same time suction of liquid to the compressor.
The controller integrates a PID algorithm which manages the dynamic response of the valve in
order to keep a satisfactory quick and stable response to system parameter variations. PID
parameters are embedded into the controller and cannot be changed. The EXV has the following
operating modes:
Pre-open
Start
Pressure