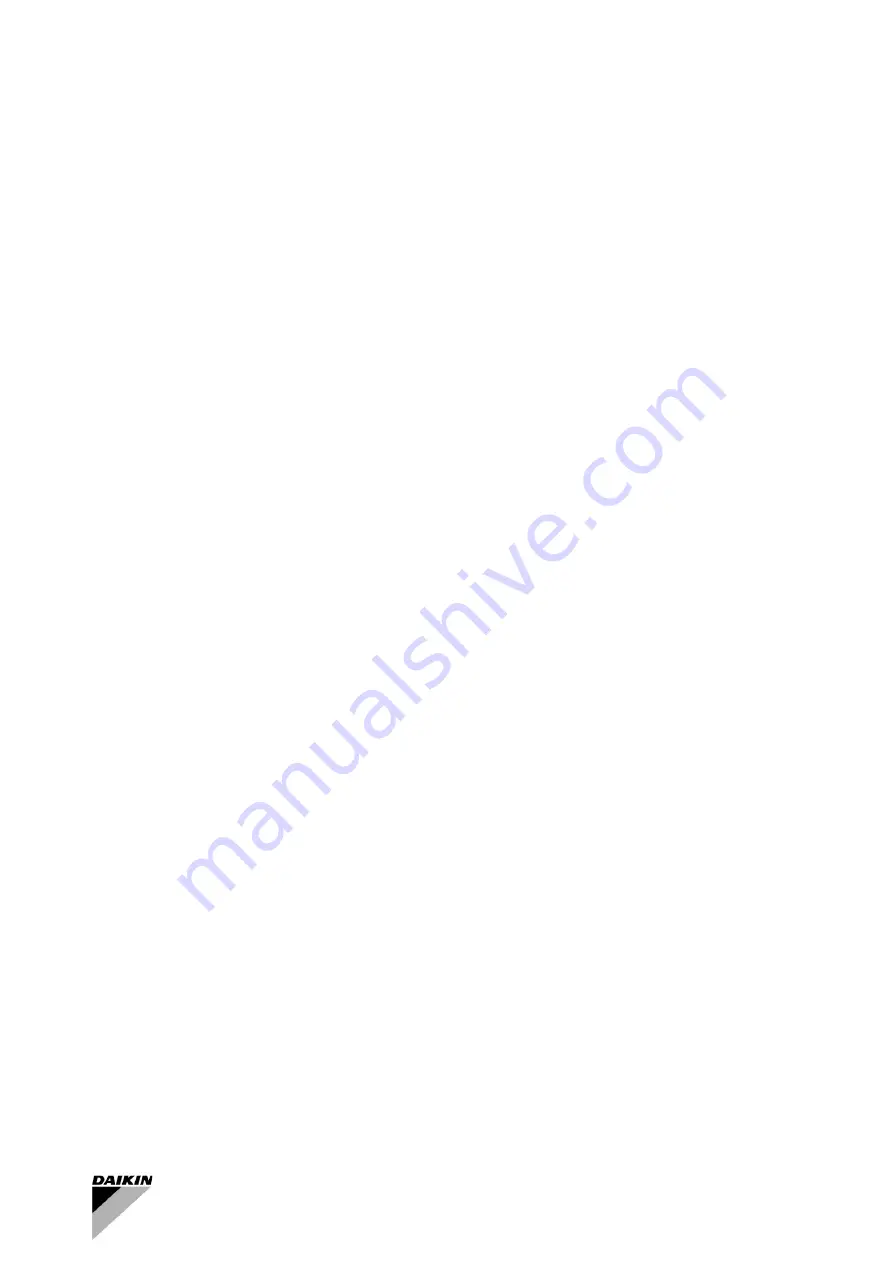
D – 508 C – 07/02 D – EN pag. 7/36
Acoustic protection
When the noise level must meet special requirements, it will be necessary to pay the maximum attention to ensure
perfect insulation of the unit from the support base by applying appropriate vibration-dampening devices, applying
vibration-dampening mounts on the water pipes and on the electrical connections.
Water piping
Due to the variety of piping practices, it is advisable to follow the recommendations of local authorities. They can
supply the installer with the proper building and safety codes required for a safe and proper installation.
Basically, the piping should be designed with a minimum number of bends and changes in elevation to keep
system cost down and performance up. It should contain:
1. Vibration eliminators to reduce vibration and noise transmission to the building.
2. Shutoff valves to isolate the unit from the piping system during unit servicing.
3. Manual or automatic air vent valves at the higher points of the system. Drains at the lower points of the
system. The evaporator and heat recovery condensers should not be the highest point in the piping system.
4. Devices to maintain adequate system water pressure (e.g. expansion tank or regulating valve).
5. Water temperature and pressure indicators located at the unit to aid in unit servicing.
6. A strainer or devices to remove foreign matter from the water before it enters the pump. The strainer should
be placed far enough upstream to prevent cavitations at the pump inlet (consult pump manufacturer for
recommendations). The use of a strainer will prolong pump life and help maintain high system performance
levels.
7. A strainer should be placed in the supply water line just prior to the inlet of the evaporator and heat recovery
condensers. This will aid in preventing foreign material from entering and decreasing the performance of the
heat exchangers.
8. The shell-and-tube evaporator has a thermostat and an electric heater to prevent freeze-up down to -28°C.
Any water piping to the unit must be protected to prevent freezing.
9. The shell-and-tube heat recovery condensers must be empty of water during the winter season, unless you fill
the water circuit with ethylene glycol.
10. If the unit is used as a replacement chiller on a previously existing piping system, the system should be
thoroughly flushed prior to unit installation and then regular chilled water analysis and chemical water
treatment is recommended immediately at equipment start-up.
11. In the event glycol is added to the water system, as an afterthought for freeze protection, recognize that the
refrigerant suction pressure will be lower, cooling performance less, and water side pressure drop greater.
System safety devices such as freeze protection and low pressure protection must be reset.
Prior to insulating the piping and filling the system, a preliminary leak check should be made.
Evaporator/Heat Recovery condenser freeze protection
All evaporators are equipped with a thermostatically controlled electric heater that provides freeze protection down
to -28°C. However, this should not be the only method of freeze protection. Unless the evaporator and heat
recovery condensers are flushed and drained as is described below in note 4, two or more of the remaining three
recommendations must be followed as part of the system design:
1. Continuous circulation of water through the piping and the heat exchanger.
2. Filling of glycol solution in the chilled water circuit.
3. Additional insulation and heating of the exposed piping.
4. Draining and flushing the chiller vessel with air during winter season.
It is the responsibility of the installing contractor and/or on-site maintenance personnel to ensure that this
additional protection is provided. Routine checks should be made to ensure adequate freeze protection is
maintained.
Failure to do so may result in damage to unit components. Freeze damage is not considered a warranty failure.