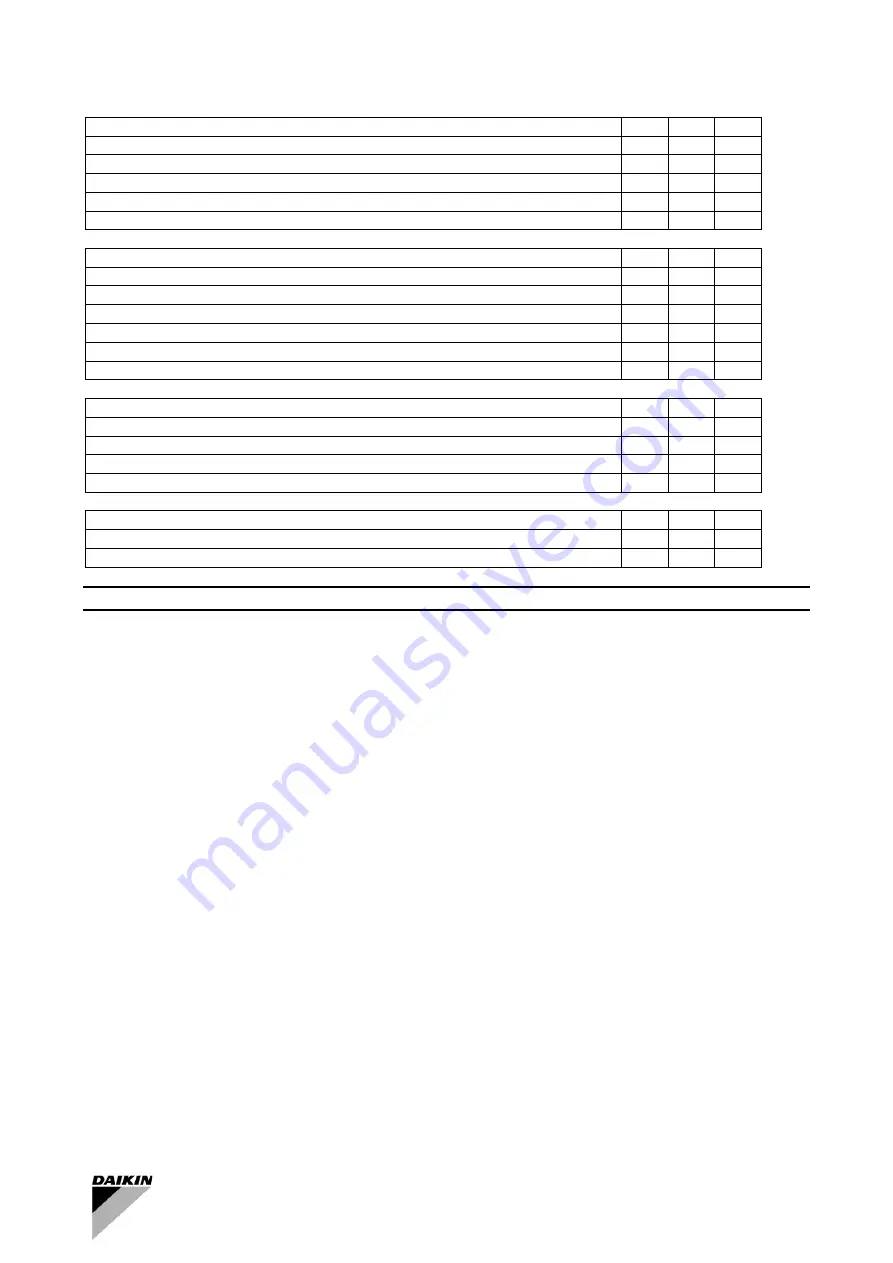
D – 508 C – 07/02 D – EN pag. 22/36
System Pre-start Checklist
Yes
No
N/A
Chilled water
Piping complete
Water system filled and vented
Pump installed, (rotation checked), strainers cleaned
Controls (3-way valves, face and bypass dampers, by-pass valves, etc.) operative
Water system operated and flow adjusted to meet unit design requirements
Heat recovery Condensers
Piping and headers complete
Water system filled and vented
Temperature sensors installed in the water well pockets
Pump installed, (rotation checked), strainers cleaned
Controls (3-way valves, face and bypass dampers, by-pass valves, etc.) operative
Water system operated and flow adjusted to meet unit design requirements
Electrical
Power leads connected to starter
All interlock wiring to the control panel complete and in accordance with specification
Pump starter and interlock wired
Wiring complies with local codes
Miscellaneous
Thermometer wells, thermometers, gauges, control wells, controls, etc., installed
A minimum 60% of system capacity is available for tests and control adjustments
Note: This check list must be completed and sent to the local DAIKIN service center two weeks prior to start-up.
Operation
Operator Responsibilities
It is important that the operator become familiar with the equipment and the system before attempting to operate the
chiller. In addition to reading this manual, the operator should study the operating manual for the control panel (latest
edition) and the electrical wiring diagram furnished with the unit before starting, operating, or shutting it down.
During the initial start up of the chiller, the DAIKIN technician will be available to answer any questions and advise
procedures for a correct operation.
It is recommended that the operator maintain a separate operation log for each chiller unit. In addition, a separate
maintenance log, specific for periodic maintenance and service activities, should be kept in place.
If the operator encounters abnormal or unusual operating conditions, it is recommended that a DAIKIN service technician
be consulted.
Refrigeration Cycle
The low-pressure refrigerant gas from the evaporator enters the screw compressor through the motor, thus cooling motor
windings. The compressor compresses the refrigerant from low to high pressure and during this process oil is injected
into the screw chamber for cooling, lubrication and sealing purposes. As a result of the injection of oil, a mixture of oil and
refrigerant reaches the high efficiency oil separator where both elements are separated by the combined action of
centrifugal force and low velocity,
As the gas leaves from the top of the oil separator, the oil flows down the receiver walls and is forced, by the effect of the
differential pressure between suction and discharge sides, back into the compressor injection port.
After leaving the oil separator, the high pressure and hot gas goes through the “four-way valve” and, depending on the
unit operation mode, enters either the air-cooled coil condenser (cooling mode) or the heat recovery water condenser
(heat recovery mode).
In either heat exchanger, the hot gas is cooled by the ambient air in the first case or by the water in the second case,
changing from gas to liquid phase.