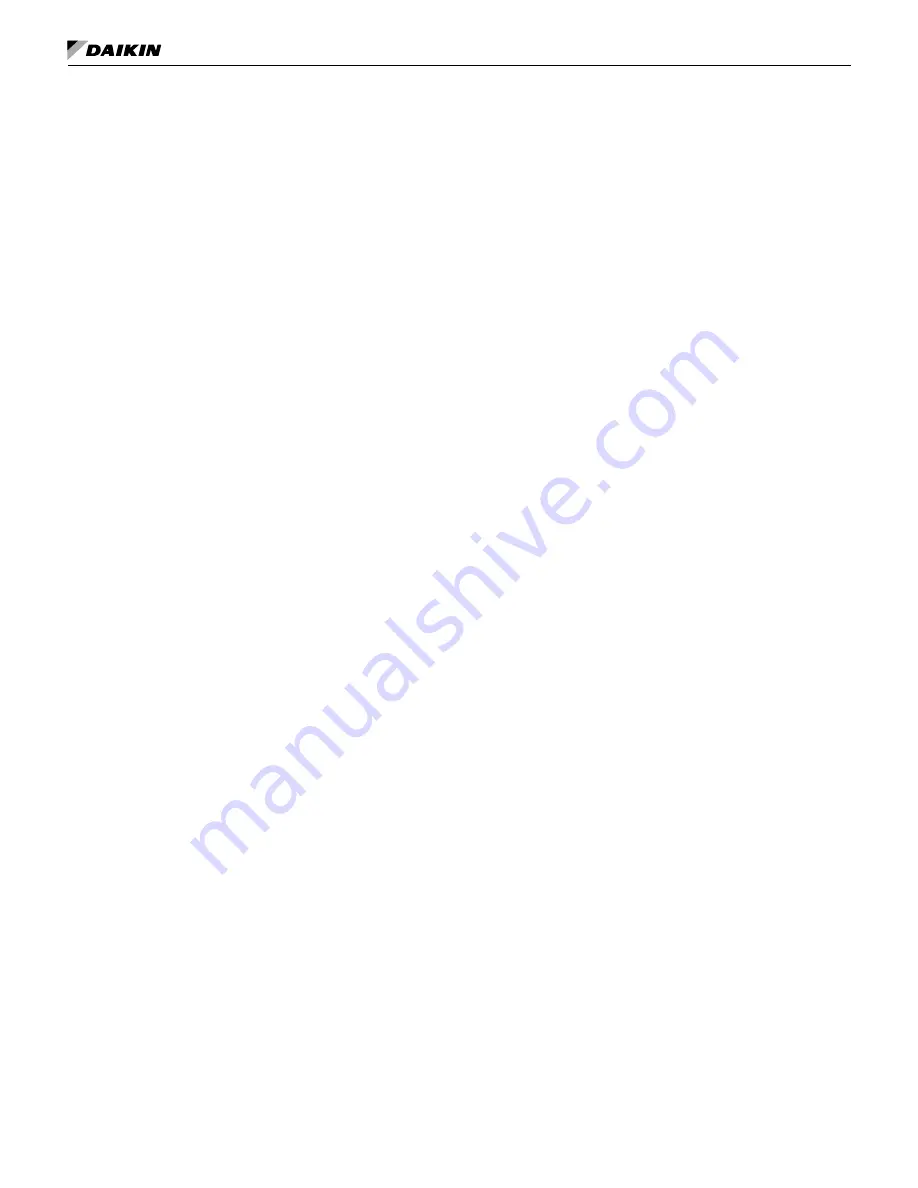
s
tart
-
uP
IM 1049-9
14 www.DaikinApplied.com
Start-up
1 .
Open all valves to full open position and turn on
power to the conditioner.
2 .
Set thermostat for “Fan Only” operation by selecting
“Off” at the system switch and “On” at the fan switch.
If “Auto” fan operation is selected, the fan will cycle
with the compressor. Check for proper air delivery.
3 .
For those units that have two-speed motors,
reconnect for low speed operation if necessary.
4 .
Set thermostat to “Cool.” If the thermostat is an
automatic changeover type, simply set the cooling
temperature to the coolest position. On manual
changeover types additionally select “Cool” at the
system switch.
Again, many conditioners have time delays which
protect the compressor(s) against short cycling.
After a few minutes of operation, check the
discharge grilles for cool air delivery. Measure
the temperature difference between entering and
leaving water. It should be approximately 1½
times greater than the heating mode temperature
difference. For example, if the cooling temperature
difference is 15°F (8°C), the heating temperature
difference should have been 10°F (5°C).
Without automatic flow control valves, target a
cooling temperature difference of 10°F to 14°F (5°C
to 8°C). Adjust the combination shutoff/balancing
valve in the return line to a water flow rate which will
result in the 10˚F to 14°F (5°C to 8°C) difference.
5 .
Set thermostat to “Heat.” If the thermostat is the
automatic changeover type, set system switch to the
“Auto” position and depress the heat setting to the
warmest selection. Some conditioners have built-
in time delays which prevent the compressor from
immediately starting. With most control schemes,
the fan will start immediately. After a few minutes of
compressor operation, check for warm air delivery
at discharge grille. If this is a “cold building” start-
up, leave unit running until return air to the unit is at
least 65°F (18°C).
Measure the temperature difference between
entering and leaving air and entering and leaving
water. With entering water of 60°F to 80°F (16°C to
27°C), leaving water should be 6°F to 12°F (3.3°C to
6.6°C) cooler, and the air temperature rise through
the machine should not exceed 35°F (19°C). If
the air temperature exceeds 35°F (19°C), then the
water flow rate is inadequate.
6 .
Check the elevation and cleanliness of the
condensate line. If the air is too dry for sufficient
dehumidification, slowly pour enough water into the
condensate pan to ensure proper drainage.
7 .
If the conditioner does not operate, check the
following points:
a. Is supply voltage to the machine compatible?
b. Is thermostat type appropriate?
c. Is thermostat wiring correct?
8 .
If the conditioner operates but stops after a brief period:
a. Is there proper airflow? Check for dirty filter,
incorrect fan rotation (3-phase fan motors only),
or incorrect ductwork.
b. Is there proper water flow rate within
temperature limits? Check water balancing;
backflush unit if dirt-clogged.
9 .
Check for vibrating refrigerant piping, fan wheels, etc.
10 .
Do not lubricate the fan motor during the first year of
operation as it is prelubricated at the factory.
11 .
Field supplied relays installed on the input terminals
W1, W2, Y1, Y2 or G may introduce electrical noise.
Never install relay coils in series with the inputs.