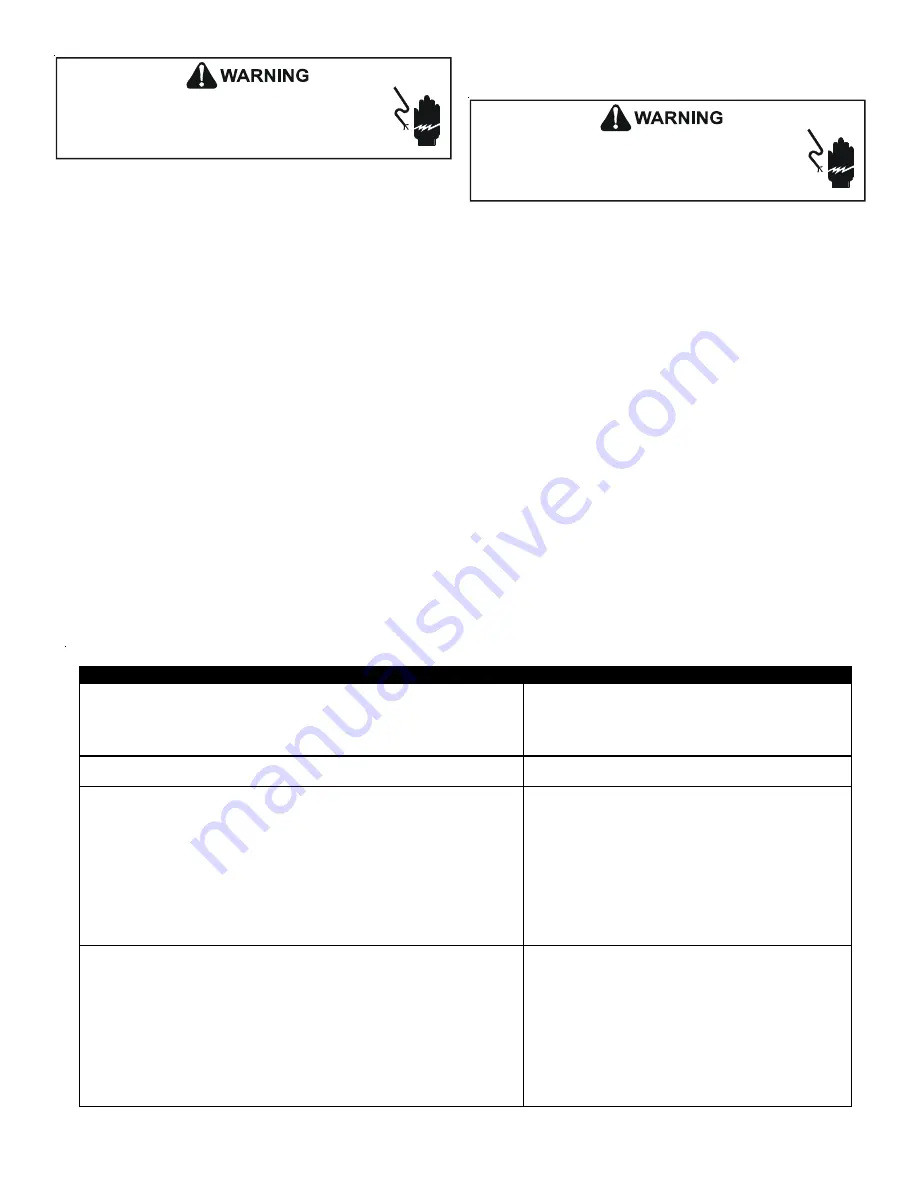
8
HIGH VOLTAGE!
Disconnect ALL power before servicing. Multiple
power sources may be present. Failure to do so may
cause property damage, personal injury or death.
4. Disconnect outdoor fan by removing the purple lead from
the Condenser Fan Defrost Relay.
5. Restart unit and allow frost to accumulate.
6. After a few minutes the defrost thermostat should close. To
verify the position of the thermostat check for 24V between
“DFT” and “C” on the defrost board. Should the defrost ther-
mostat fail to close after a heavy build-up of frost and the
thermostat is less than 28
°
, the thermostat is to be replaced.
7. After the thermostat has closed, short across the test pins
with the a screwdr
iver blade until the reversing valve shifts.
This could take up to 22 seconds depending upon the posi-
tion of the timing setting on the defrost board. Immediately
upon the action of the reversing valve, remove the short.
Note:
If this short is not removed immediately, the defrost
activity will last only 3 seconds.
8. After defrost has terminated (up to 10 minutes) check the
defrost thermostat for 24V between “DF
T” and “C”. This
reading should be 0V (open sensor).
9. Shut off power to the unit.
HIGH VOLTAGE!
Disconnect ALL power before servicing. Multiple
power sources may be present. Failure to do so may
cause property damage, personal injury or death.
10. Replace outdoor fan mo
tor wire removed in Step 4.
NOTE:
The compressor “run time’ is accumulative during multiple
heating cycles. The timer will reset to zero only when the defrost
sensor returns to an open condition. If the room thermostat is
operating in the “EM HT” mode, no accumulation of compressor
time is recorded.
TROUBLESHOOTING
Qualified Installer/Servicer only
When troubleshooting, the first step should always be to check
for clean coils, clean filter(s), and proper airflow. Indoor airflow
should be 375 to 425 CFM per ton of cooling based on the size of
the outdoor unit. The most common way of establishing indoor
airflow is heating temperature rise. Indoor airflow will then be
(Heating output of equipment) / (1.1 x temp. rise). In other cases,
measurement of external static pressure is helpful. For details,
see the Installation Instructions for your indoor unit.
TROUBLE SHOOTING ANALYSIS TABLE
COMPLAINT
PROBABLE CAUSE
REMEDY
1. High Head Pressure
1. Excessive charge of refrigerant in system.
2. Inadequate supply of air across the
condenser coil.
3. Non-condensate gases in the system.
1. Purge or pump-down excessive charge.
2. Make certain that coil is not fouled in any
way, or that air is not re-circulating.
3. Purge these gases from the system.
Recharge system, if necessary.
2. Low Head Pressure
1. System low on refrigerant.
2. Compressor valves broken.
1. Charge system until sight glass is clear of bubbles.
2. Replace compressor.
3. Low Suction Pressure
1. Liquid line valve closed.
2. Restricted liquid line.
3. The bulb of the thermal expansion valve
has lost its charge.
4. System low on refrigerant.
5. Dirty filters.
6. Coil frosted up.
7. Flash gas in the liquid line.
8. Quantity of air through evaporator not adequate.
1. Open the liquid line valve.
2. Replace filter-dryer.
3. Detach the bulb from the suction line and hold
in one hand. If no liquid refrigerant goes through
the valve, replace the valve.
4. Test the unit for leaks. Add refrigerant until sight
glass is free from bubbles, after repairing leak.
5. Clean or replace filter.
6. Defrost and clean coil. Clean or replace filters.
7. Excessive liquid line drop. Check liquid line size.
8. Increase the blower speed.
4. High Suction Pressure
1. Expansion valve stuck open.
2. Expansion valve bulb not in contact with
suction line.
3. Suction and/or discharge valve leaking or broken.
1. Correct valve action or replace the valve.
2. Fasten bulb securely to suction line.
3. Replace compressor.
5. Compressor will not start.
1. Disconnect switch open.
2. Blown fuse or fuse at disconnect switch.
3. Thermostat set too high.
4. Selector switch in "Off" position.
5. Contactor and/or relay coils burned out.
6. Loose or open electrical connection in either
the control or power circuit.
1. Close the disconnect switch.
2. Check the cause of failure and replace the fuse.
3. Adjust to lower temperature.
4. Turn selector switch knob to "Cool" position.
5. Replace contactor and/or relay.
6. Inspect and secure all electrical connections.