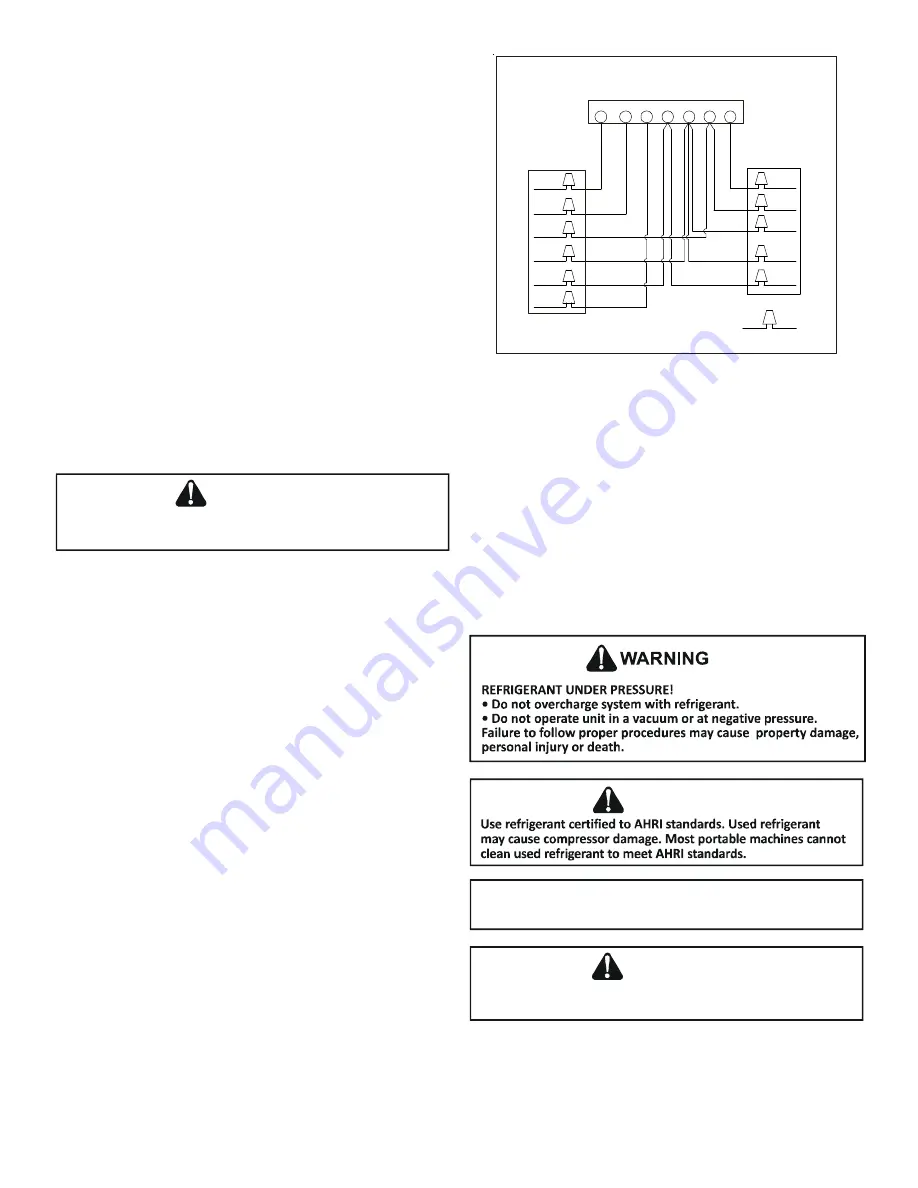
6
OVERCURRENT PROTECTION
The following overcurrent protection devices are approved for use.
•
Time delay fuses
•
HACR type circuit breakers
These devices have sufficient time delay to permit the motor-com-
pressor to start and accelerate its load.
Refer to the unit serial plate for the maximum overcurrent pro-
tection permitted.
Run all line voltage wiring a conduit from the service disconnect
box to the unit. Refer to the NEC (USA) or CEC (Canada) codes for
the correct size conduit based on the wire size. The conduit en-
ters the control box through the hole provided in the bottom.
NOTE:
The control box hole is sized for 3/4” conduit. If permitted
by code, a flexible conduit is preferred to minimize vibration trans-
mission from the unit to the building.
Connect the line voltage wires to the L1, L2, and L3 terminals of
the definite purpose contactor (located in the unit control box).
Refer to the wiring diagram attached to the unit when making
these connections.
THREE PHASE COMPRESSOR ROTATION
Use care when handling scroll compressors. Dome temperatures
could be hot.
CAUTION
Three phase scrolls are power phase dependent and can compress
in more than one direction.
Verify proper rotation for three phase compressors by ensuring
the suction pressure drops and discharge pressure rises when the
compressor is energized.
NOTE:
When operated in reverse, a three
phase scroll compressors is noisier and its current draw substan-
tially reduced compared to marked values.
To correct, disconnect power and switch any two leads at the unit
contactor and re-observe.
HIGH VOLTAGE CONNECTIONS
Route power supply and ground wires through the high voltage
port and terminate in accordance with the wiring diagram pro-
vided inside the control panel cover.
LOW VOLTAGE CONNECTIONS
Condensing unit control wiring requires a five-conductor low volt-
age circuit from the room thermostat (without options). The wires
should be no smaller than 18 AWG and the field connection for
this circuit must be made in the unit control box using solderless
connectors (i.e. wire nuts). See the following diagram for a typical
low voltage hook-up.
TWO STAGE LOW VOLTAGE HOOK-UP
THERMOSTAT
O
W2
C
R
RED
BROWN
WHITE
BLUE
BLUE
WHITE
CONDENSING
UNIT
AIR
HANDLER
YELLOW
PURPLE
RED
Y1
G
GREEN
Y2
WIRE NUT
ORANGE
SYSTEM START UP
Never operate the compressor with the suction valve
closed to
test the compressor’s pumping efficiency. In some
cases, this can
result in serious compressor damage and loss of warranty cover-
age.
For the 7-1/2 ton unit starting charge should be 18 lbs. of R-410A and
20 lbs. for the 10 ton unit. The length of line set, indoor unit air-
flow, condensing unit location and number of tubing fittings will
have an impact on final unit charge amount. Turn the electrical
power on, and let the system run. Wait for the refrigerant pres-
sures to stabilize.
CHARGE VERIFICATION
CAUTION
NOTICE
Violation of EPA regulations may result in fines or other penalties.
Operating the compressor with the suction valve closed will void
the warranty and cause serious compressor damage.
CAUTION