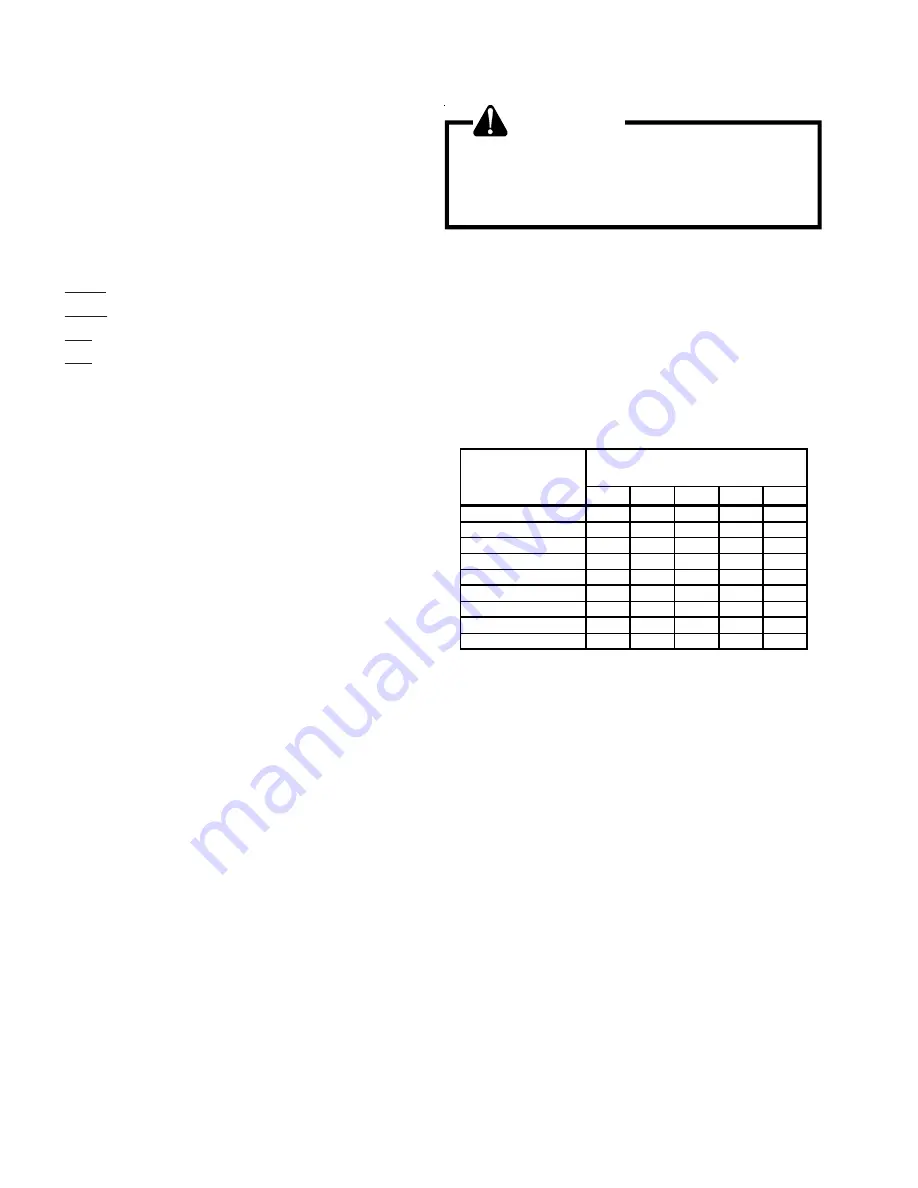
SERVICING
32
The reason for compressor inefficiency is broken or damaged
suction and/or discharge valves, or scroll flanks on Scroll
compressors, reducing the ability of the compressor to pump
refrigerant vapor.
The condition of the valves or scroll flanks is checked in the
following manner.
1. Attach gauges to the high and low side of the system.
2. Start the system and run a Cooling Performance Test.
If the test shows-
⇒
Below normal high side pressure.
⇒
Above normal low side pressure.
⇒
Low temperature difference across coil.
⇒
Low amp draw at compressor.
-and the charge is correct. The compressor is faulty - replace
the compressor.
S-104 CHECKING COMPRESSOR EFFICIENCY
The reason for compressor inefficiency is broken or damaged
scroll flanks on Scroll compressors, reducing the ability of
the compressor to pump refrigerant vapor.
During the "OFF" cycle, the high side pressure bleeds to the
low side through the fixed orifice restriction device. Check
equalization time as follows:
1. Attach a gauge manifold to the suction and liquid line dill
valves.
2. Start the system and allow the pressures to stabilize.
3. Stop the system and check the time it takes for the high
and low pressure gauge readings to equalize.
If it takes more than seven (7) minutes to equalize, the
restrictor device is inoperative. Replace, install a liquid line
drier, evacuate and recharge.
S-106 OVERFEEDING
Overfeeding by the expansion valve results in high suction
pressure, cold suction line, and possible liquid slugging of the
compressor.
If these symptoms are observed:
1. Check for an overcharged unit by referring to the cooling
performance charts in the spec sheet manual.
2. Check the operation of the power element in the valve.
3. Check for restricted or plugged equalizer tube.
S-108 SUPERHEAT
CHECKING SUPERHEAT
Refrigerant gas is considered superheated when its tempera-
ture is higher than the saturation temperature corresponding
to its pressure. The degree of superheat equals the degrees
of temperature increase above the saturation temperature at
existing pressure. See Temperature - Pressure Chart .
CAUTION
To prevent personal injury, carefully connect and
disconnect manifold gauge hoses. Escaping liquid
refrigerant can cause burns. Do not vent refrigerant
to atmosphere. Recover during system repair
or final unit disposal.
1. Run system at least 10 minutes to allow pressure to
stabilize.
2. Temporarily install thermometer on suction (large) line
near compressor with adequate contact and insulate for
best possible reading.
3. Refer to the superheat table provided for proper system
superheat. Add charge to lower superheat or recover
charge to raise superheat.
Superheat Formula = Suct. Line Temp. - Sat. Suct. Temp.
Ambient Condenser
Inlet Temp
(°F Drybulb)
65
70
75
80
85
100
---
---
---
10
10
95
---
---
10
10
10
90
---
---
12
15
18
85
---
10
13
17
20
80
---
10
15
21
26
75
10
13
17
25
29
70
10
17
20
28
32
65
13
19
26
32
35
60
17
25
30
33
37
Return Air Temp. (°F Drybulb)
SYSTEM SUPERHEAT
EXAMPLE:
a. Suction Pressure = 143
b. Corresponding Temp. °F. = 50
c. Thermometer on Suction Line = 59°F.
To obtain the degrees temperature of superheat, subtract
50.0 from 59.0°F.
The difference is 9° Superheat. The 9° Superheat would fall
in the ± range of allowable superheat.
S-111 FIXED ORIFICE RESTRICTION DEVICES
The fixed orifice restriction device (flowrator) used in conjunc-
tion with the indoor coil is a predetermined bore (I.D.).
It is designed to control the rate of liquid refrigerant flow into
an evaporator coil.
The amount of refrigerant that flows through the fixed orifice
restriction device is regulated by the pressure difference
between the high and low sides of the system.
In the cooling cycle when the outdoor air temperature rises,
the high side condensing pressure rises. At the same time,
the cooling load on the indoor coil increases, causing the low
side pressure to rise, but at a slower rate.
Summary of Contents for DCC090 Series
Page 40: ...40 DCC COMMERCIAL 3 6 Ton PackagedAir Conditioner Unit WIRING DIAGRAMS ...
Page 44: ...44 DCH COMMERCIAL 3 6 Ton Packaged Heat Pump Unit WIRING DIAGRAMS ...
Page 90: ...44 DCC COMMERCIAL 7 5 12 5 Ton Packaged Air Conditioner Unit WIRING DIAGRAMS ...
Page 93: ...47 DCH COMMERCIAL 7 5 12 5 Ton Packaged Heat Pump Unit WIRING DIAGRAMS ...
Page 133: ...38 DCC COMMERCIAL 15 25 Ton Packaged Air Conditioner Unit WIRING DIAGRAMS ...