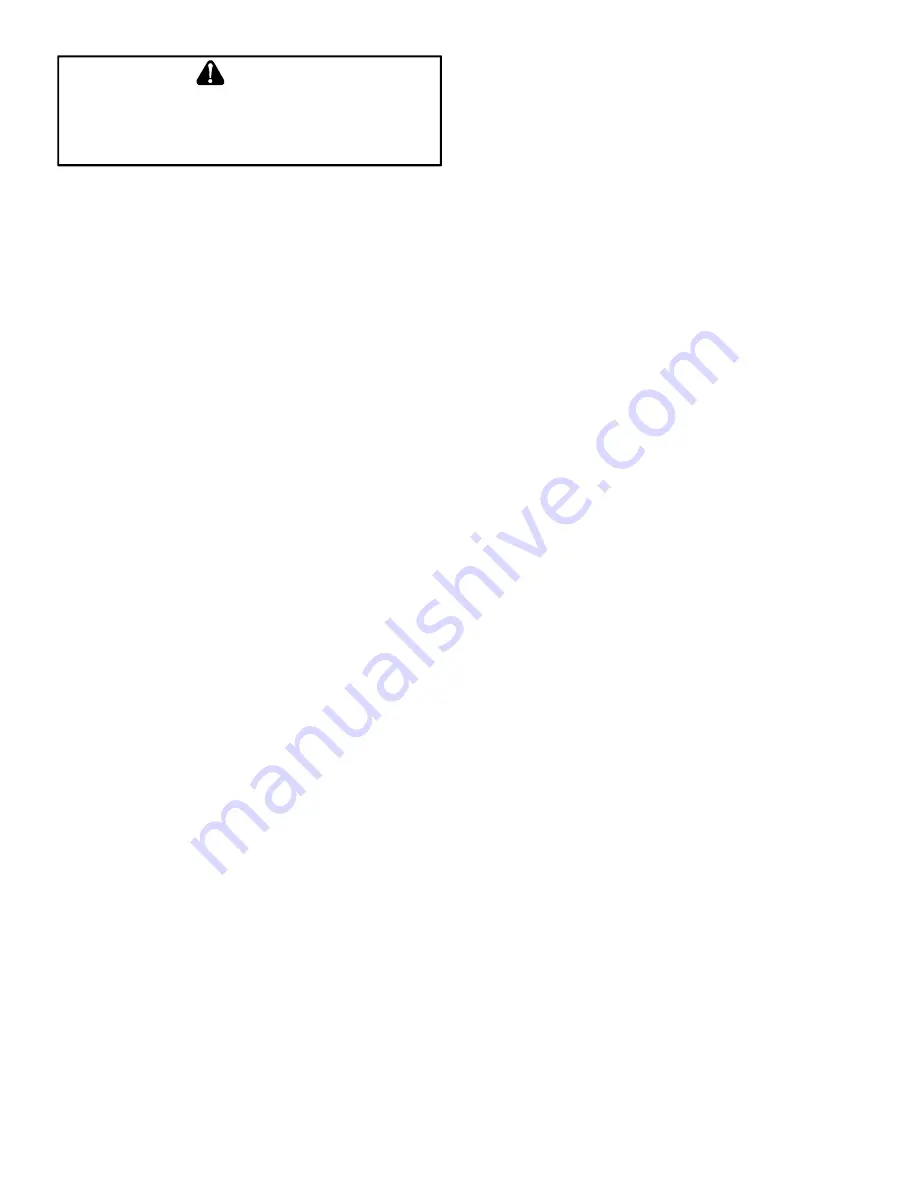
7
P
OSSIBLE
PROPERTY
DAMAGE
,
PERSONAL
INJURY
OR
DEATH
DUE
TO
FIRE
,
EXPLOSION
,
SMOKE
,
SOOT
,
CONDENSATION
,
ELECTRICAL
SHOCK
OR
CARBON
MONOXIDE
MAY
RESULT
FROM
IMPROPER
INSTALLATION
,
REPAIR
OPERATION
,
OR
MAINTENANCE
OF
THIS
PRODUCT
.
WARNING
•
• Centrally locate the furnace with respect to the
proposed or existing air distribution system.
• Ensure the temperature of the return air entering the
furnace is between 55°F and 100°F when the furnace is
heating.
•
Provide provisions for venting combustion products
outdoors through a proper venting system. Special
consideration should be given to vent/flue pipe routing
and combustion air intake pipe when applicable.
Refer to
Vent/Flue Pipe and Combustion Air Pipe
-Termination Locations
for appropriate termination
locations and to determine if the piping system from
furnace to termination can be accomplished within
the guidelines given.
NOTE:
The length of flue and/
or combustion air piping can be a limiting factor in the
location of the furnace.
•
Locate the furnace so condensate flows downwards
to the drain. Do not locate the furnace or its
condensate drainage system in any area subject to
below freezing temperatures without proper freeze
protection.
•
Ensure adequate combustion air is available for the
furnace. Improper or insufficient combustion air
can expose building occupants to gas combustion
products that could include carbon monoxide. Refer
to
Combustion and Ventilation Air Requirements.
•
Set the furnace on a level floor to enable proper
condensate drainage. If the floor becomes wet or
damp at times, place the furnace above the floor on
a concrete base sized approximately 1-1/2” larger
than the base of the furnace. Refer to the
Horizontal
Applications and Considerations
for leveling of
horizontal furnaces.
•
Ensure upflow or horizontal furnaces are not installed
directly on carpeting, or any other combustible
material. The only combustible material allowed is
wood.
• A special accessory sub-base must be used for
upright counterflow unit installations over any
combustible material (including wood). Refer to sub-
base instructions for installation details. (
NOTE:
A
sub-base will not be required if an air conditioning coil
is located beneath the furnace between the supply air
opening and the combustible floor.
• Exposure to contaminated combustion air will result in
safety and performance-related problems. Do not install
the furnace where the combustion air is exposed to the
following substances:
permanent wave solutions
chlorinated waxes or cleaners
chlorine-based
carbon tetrachloride
water softening chemicals
swimming pool chemicals
deicing salts or chemicals
halogen type refrigerants
printing inks
cleaning solutions (such as perchloroethylene)
paint removers
varnishes
hydrochloric acid
cements and glues
antistatic fabric softeners for clothes dryers
masonry acid washing materials
• Enclose a
non-direct vent
furnace if it is installed near
an area frequently contaminated by any of the above
substances. This protects the
non-direct vent
furnace
from airborne contaminants. To ensure that the
enclosed
non-direct
vent
furnace has an adequate
supply of combustion air, provide air from a nearby
uncontaminated room or from outdoors. Refer to
the
Combustion and Ventilation Air Requirements
for
details.
• If the furnace is used in connection with a cooling coil
unit, install the furnace upstream or in parallel with the
cooling coil unit. Premature heat exchanger failure will
result if the cooling unit is placed ahead of the furnace.
•
For vertical (upflow or downflow) applications, the
minimum cooling coil width shall not be less than
furnace width minus 1”. Additionally, a coil installed
above an upflow furnace or under a counterflow
furnace may be the same width as the furnace or may
be one size larger than the furnace.
Example: a “C”
width coil may be installed with a “B” width furnace.
•
For upflow applications, the front of the coil and
furnace must face the same direction.
• If the furnace is installed in a residential garage,
position the furnace so that the burners and ignition
source are located not less than 18 inches (457 mm)
above the floor. Protect the furnace from physical
damage by vehicles.
• If the furnace is installed horizontally, ensure the
access doors are not on the “up/top” or “down/
bottom” side of the furnace.
•
Do not connect this furnace to a chimney flue that
serves a separate appliance designed to burn solid
fuel.
•
On Counterflow Installations, the air conditioning coil
must be downstream on the supply (positive) side of
the furnace heat exchanger.
•
Counterflow Installation over a noncombustible floor.
Before setting the furnace over the plenum opening,
ensure the surface around the opening is smooth
and level. A tight seal should be made between the
furnace base and floor by using a silicone rubber
caulking compound or cement grout.