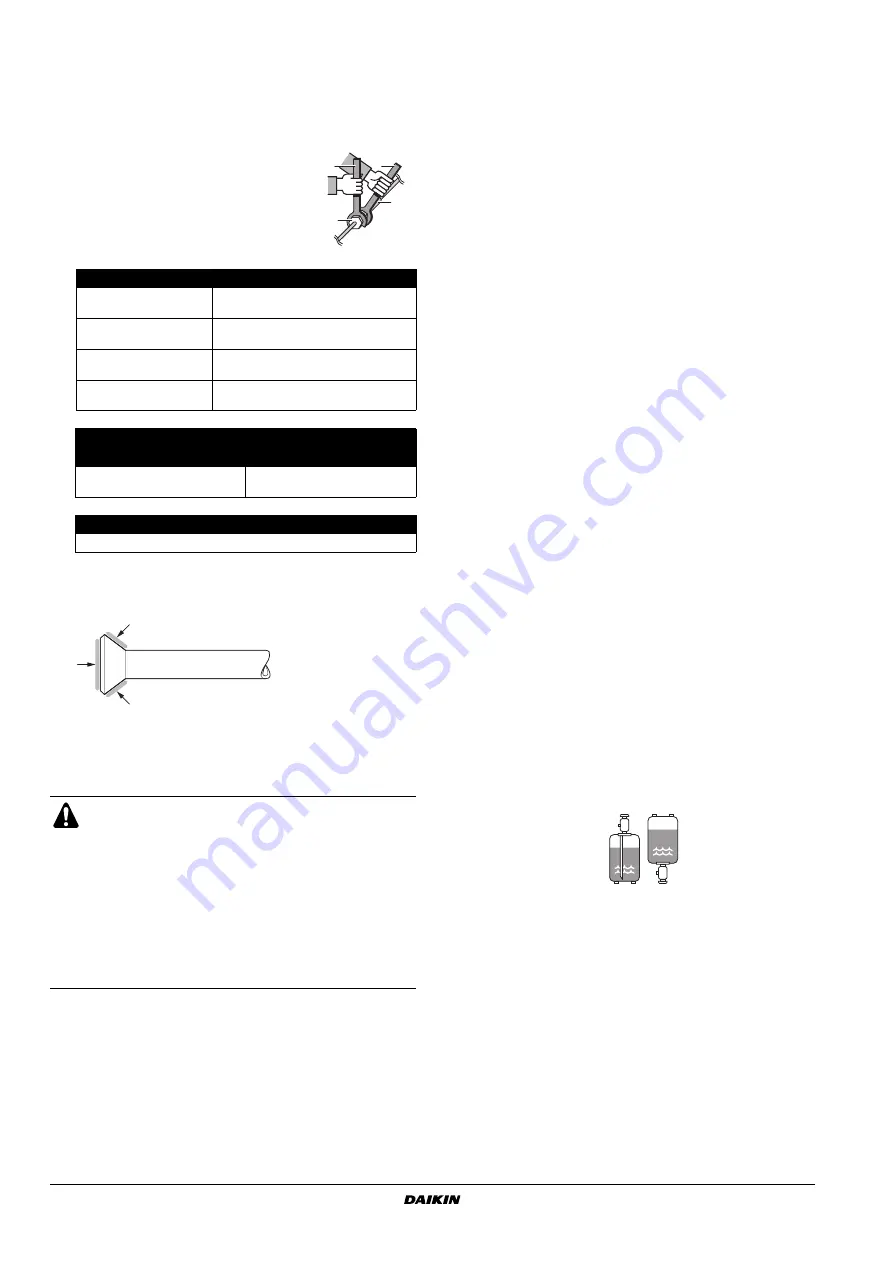
Installation manual
5
4AMX80E7V3B
R410A Split series
4PW38479-1A
Refrigerant piping
1
Align the centres of both flares and tighten the flare nuts 3 or 4
turns by hand. Then tighten them fully with torque wrenches.
Use torque wrenches when tightening the flare nuts to prevent
damage to the flare nuts and to prevent escaping of gas.
2
To prevent gas leakage, apply refrigeration machine oil on both
inner and outer surfaces of the flare (use refrigeration oil for
R410A).
Purging air and checking gas leakage
When piping work is completed, it is necessary to purge the air and
check for gas leakage.
■
If using additional refrigerant, perform air purging from the
refrigerant pipes and indoor unit using a vacuum pump, then
charge additional refrigerant.
■
Use a hexagonal wrench (4 mm) to operate the stop valve rod.
■
All refrigerant pipe joints should be tightened with a torque
wrench at the specified tightening torque.
1
Connect the projection side (on which the worm pin is pressed)
of the charging hose coming from the gauge manifold to the gas
stop valve’s service port.
2
Fully open the gauge manifold’s low-pressure valve (Lo) and
completely close its high-pressure valve (Hi).
The high-pressure valve subsequently requires no operation.
3
Apply vacuum pumping. Check that the compound pressure
gauge reads –0.1 MPa (–760 mm Hg).
Evacuation for at least 1 hour is recommended.
4
Close the gauge manifold’s low-pressure valve (Lo) and stop the
vacuum pump.
Leave as is for 4-5 minutes and make sure the coupling meter
needle does not go back.
If it does go back, this may indicate presence of moisture or
leaking from connecting parts. Repeat steps 2 – 4 after checking
all connecting parts and slightly loosening and retightening the
nuts.
5
Remove covers from liquid stop valve and gas stop valve.
6
Turn the liquid stop valve’s rod 90 degrees counterclockwise
with a hexagonal wrench to open the valve.
Close it after 5 seconds, and check for gas leakage.
Using soapy water, check for gas leakage from indoor unit’s flare
and outdoor unit’s flare and valve rods.
After the check is complete, wipe all soapy water off.
7
Disconnect charging hose from gas stop valve’s service port,
then fully open liquid and gas stop valves.
Do not attempt to turn valve rod beyond its stop.
8
Tighten valve lids and service port caps for the liquid and gas
stop valves with a torque wrench at the specified torques. See
"Refrigerant piping work" on page 4
for details.
Charging refrigerant
This outdoor unit is factory charged.
In case re-charge is required, refer to the nameplate of the unit. The
nameplate states the type of refrigerant and necessary amount.
Precautions when adding R410A
Be sure to charge the specified amount of refrigerant in liquid state to
the liquid pipe.
Since this refrigerant is a mixed refrigerant, adding it in gas form may
cause the refrigerant composition to change, preventing normal
operation.
■
Before charging, check whether the refrigerant cylinder is
equipped with a siphon tube or not.
■
Be sure to use tools exclusively for R410A to ensure required
pressure resistance and to prevent foreign materials from mixing
into the system.
1
Torque wrench
2
Spanner
3
Piping union
4
Flare nut
Flare nut
Flare nut tightening torque
Ø6.4
14.2~17.2 N•m
(144~175 kgf•cm)
Ø9.5
32.7~39.9 N•m
(333~407 kgf•cm)
Ø12.7
49.5~60.3 N•m
(505~615 kgf•cm)
Ø15.9
61.8~75.4 N•m
(630~769 kgf•cm)
Valve cap tightening torque
Liquid pipe
Gas pipe
26.5~32.3 N•m
(270~330 kgf•cm)
48.1~59.7 N•m
(490~610 kgf•cm)
Service port cap tightening torque
10.8~14.7 N•m (110~150 kgf•cm)
WARNING
■
Do not mix any substance other than the specified
refrigerant (R410A) into the refrigeration cycle.
■
When refrigerant gas leaks occur, ventilate the room
as soon and as much as possible.
■
R410A, as well as other refrigerants, should always
be recovered and never be released directly into the
environment.
■
Use a vacuum pump for R410A exclusively. Using the
same vacuum pump for different refrigerants may
damage the vacuum pump or the unit.
1
2
3
4
Charge the liquid
refrigerant with the cylinder
in upright position.
Charge the liquid
refrigerant with the cylinder
in up-side-down position.
Summary of Contents for 4AMX80E7V3B
Page 1: ...INSTALLATION MANUAL 4AMX80E7V3B R410A Split series ...
Page 15: ...NOTES NOTES ...
Page 16: ...4PW38479 1A Copyright Daikin ...