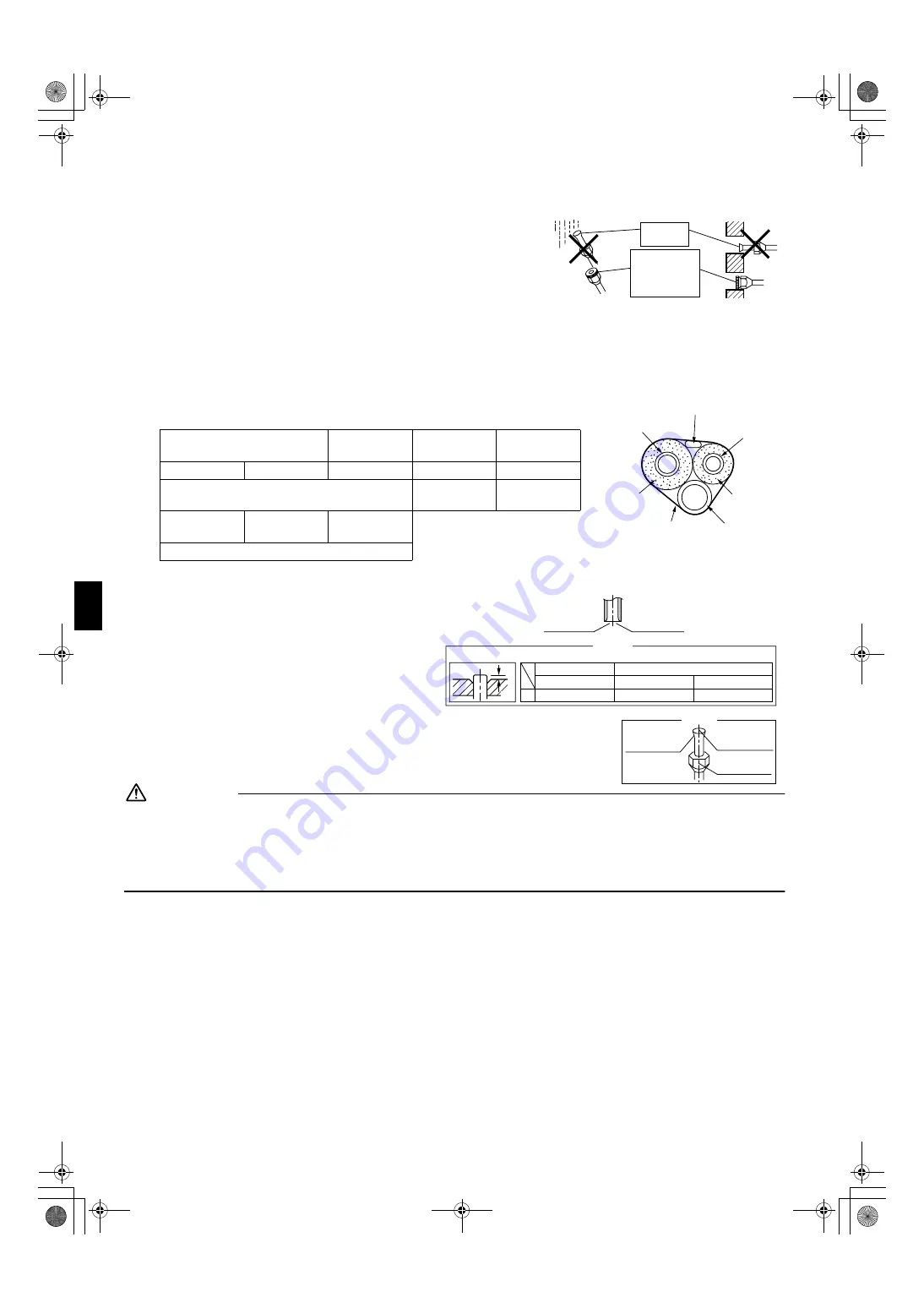
9
■
English
Refrigerant Piping Work
Precautions for Laying Refrigerant Piping
• Cautions on pipe handling
1) Protect the open end of the pipe against dust and moisture.
2) All pipe bends should be as gentle as possible. Use a pipe bender for
bending.
• Selection of copper and heat insulation materials
When using commercial copper pipes and fittings, observe the following:
1) Insulation material: Polyethylene foam
Heat transfer rate: 0.041 to 0.052W/mK (0.035 to 0.045kcal/mh°C)
Refrigerant gas pipe’s surface temperature reaches 110°C max.
Choose heat insulation materials that will withstand this temperature.
2) Be sure to insulate both the gas and liquid piping and to provide insulation dimen-
sions as below.
3) Use separate thermal insulation pipes for gas and liquid refrigerant pipes.
• Flaring the pipe end
1) Cut the pipe end with a pipe cutter.
2) Remove burrs with the cut surface facing down-
ward so that the chips do not enter the pipe.
3) Put the flare nut on the pipe.
4) Flare the pipe.
5) Check that the flaring is properly made.
WARNING
• Do not use mineral oil on flared part.
• Prevent mineral oil from getting into the system as this would reduce the lifetime of the units.
• Never use piping which has been used for previous installations. Only use parts which are delivered with the unit.
• Do never install a drier to this R410A unit in order to guarantee its lifetime.
• The drying material may dissolve and damage the system.
• Incomplete flaring may cause refrigerant gas leakage.
Gas pipe
Liquid pipe
Gas pipe
insulation
Liquid pipe
insulation
O.D.9.5mm
O.D.12.7mm
O.D.6.4mm
I.D.12-15mm
I.D.8-10mm
Minimum bend radius
Thickness
13mm Min
Thickness
10mm Min
30mm or
more
40mm or
more
30mm or
more
Thickness 0.8mm (C1220T-O)
Wall
If no flare cap is
available, cover
the flare mouth
with tape to keep
dirt or water out.
Be sure to
place a cap.
Rain
Gas pipe
Liquid pipe
Gas pipe
insulation
Liquid pipe
insulation
Finishing tape
Drain hose
Inter-unit wires
(Cut exactly at
right angles.)
Remove burrs
Set exactly at the position shown below.
A
Flaring
Die
Check
Flare’s inner
surface must
be flaw-free.
The pipe end must
be evenly flared in
a perfect circle.
Make sure that the
flare nut is fitted.
A
0-0.5mm
Clutch-type
Flare tool for R410A
1.0-1.5mm
Clutch-type (Rigid-type)
1.5-2.0mm
Wing-nut type (Imperial-type)
Conventional flare tool
01_EN_3P210724-1F.fm Page 9 Tuesday, October 30, 2012 10:39 AM