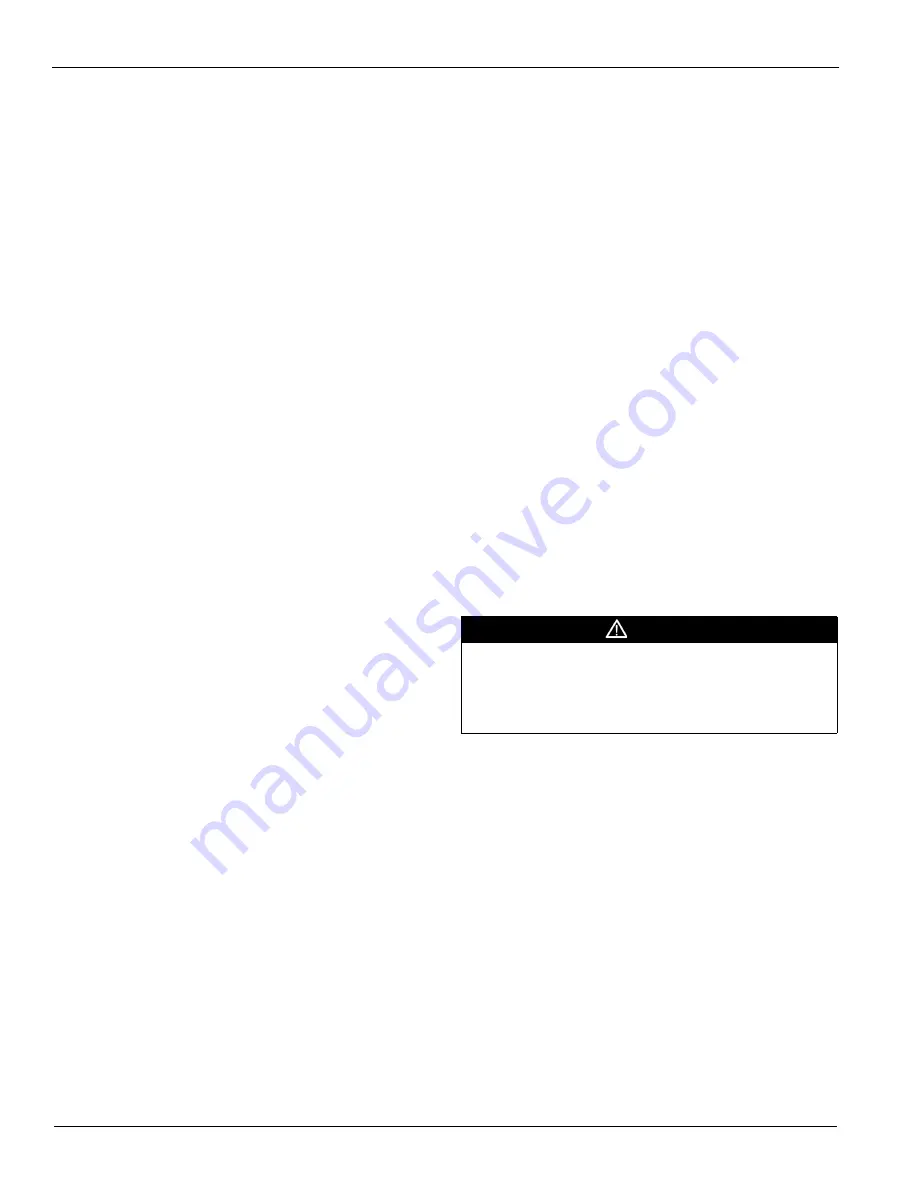
10
IM 1167
Installation and Startup
Chilled Water Piping
IMPORTANT: Piping design must be provided by a
qualified Architect or Systems HVAC Design Engineer
familiar with piping design, as well as local codes and
regulations. The manufacturer recommendations provided
here are to be used as a general guide, but do not replace
system design by a qualified professional.
Design the piping with a minimum number of bends and
changes in elevation to keep system cost down and
performance up. It should contain:
1
Vibration eliminators to reduce vibration and noise
transmission to the building.
2
Shutoff valves to isolate the unit from the piping system
during unit servicing.
3
Manual or automatic air-vent valves at the high points of
the system and drains at the low parts in the system. The
evaporator should not be the highest point in the piping
system.
4
Some means of maintaining adequate system water
pressure (i.e., expansion tank or regulating valve).
5
Water temperature and pressure indicators located at the
evaporator inlet and outlet to aid in unit servicing. Any
connections should be made prior to filling the system
with water.
6
A strainer to remove foreign matter from the water
before it enters the pump. Place the strainer far enough
upstream to prevent cavitation at the pump inlet (consult
pump manufacturer for recommendations). The use of a
strainer will prolong pump life and help maintain high
system performance levels.
Note:
A perforated metal
basket strainer with 0.125-inch perforation, 40% open
area. must also be placed in the supply water line just
prior to the inlet of the evaporator. See “Optional Inlet
Strainer” on following page. This will aid in preventing
foreign material from entering the evaporator and
causing damage or decreasing its performance. Care
must also be exercised if welding pipe or flanges to the
evaporator connections to prevent any weld slag from
entering the evaporator.
7
Any water piping to the unit must be protected to prevent
freeze-up if below freezing temperatures are expected.
8
If the unit is used as a replacement chiller on a
previously existing piping system, flush the system
thoroughly prior to unit installation. Perform regular
chilled water analysis and chemical water treatment
immediately at equipment start-up.
9
In the event glycol is added to the water system as a late
addition for freeze protection, recognize that the
refrigerant suction pressure will be lower, cooling
performance less, and water side pressure drop greater. If
the percentage of glycol is large, or if propylene is
employed in lieu of ethylene glycol, the added pressure
drop and loss of performance could be substantial.
10
Do not use PVC or CPVC piping due to incompatibility
with POE oil in the event of a refrigerant to water leak.
11
For ice making or low temperature glycol operation, a
different freezestat pressure value is usually required.
The freezestat setting can be manually changed through
the MicroTech III controller.
Make a preliminary leak check prior to insulating the water
piping and filling the system.
Include a vapor barrier with the piping insulation to prevent
moisture condensation and possible damage to the building
structure. It is important to have the vapor barrier on the
outside of the insulation to prevent condensation within the
insulation on the cold surface of the pipe.
Chilled Water Pump
It is important that the chilled water pumps be wired to, and
controlled by, the chiller's microprocessor. The chiller
controller has the capability to selectively start pump A or B or
automatically alternate pump selection and also has standby
operation capability. The controller will energize the pump
whenever at least one circuit on the chiller is enabled to run,
whether there is a call for cooling or not. This helps ensure
proper unit start-up sequence. The pump will also be turned on
when the water temperature reaches 1°F below the Freeze
Setpoint to help prevent evaporator freeze-up. Wiring
connection points are shown in
Figure 41, page 65
.
CAUTION
Adding glycol or draining the system is the recommended
method of freeze protection. If the chiller does not have the
ability to control the pumps and the water system is not drained
in temperatures below freezing, catastrophic evaporator failure
may occur.
Failure to allow pump control by the chiller may cause the
following problems:
1
If any device other than the chiller attempts to start the
chiller without first starting the pump, the chiller will
lock out on the No Flow alarm and require manual reset.
2
If the chiller evaporator water temperature drops below
the “Freeze setpoint” the chiller will attempt to start the
water pumps to avoid evaporator freeze. If the chiller
does not have the ability to start the pumps, the chiller
will alarm due to lack of water flow.
3
If the chiller does not have the ability to control the
pumps and the water system is not to be drained in
temperatures below freezing, the chiller may be subject
to catastrophic evaporator failure due to freezing. The
freeze rating of the evaporator is based on the immersion
heater and pump operation. The immersion heater itself
may not be able to properly protect the evaporator from
freezing without circulation of water.