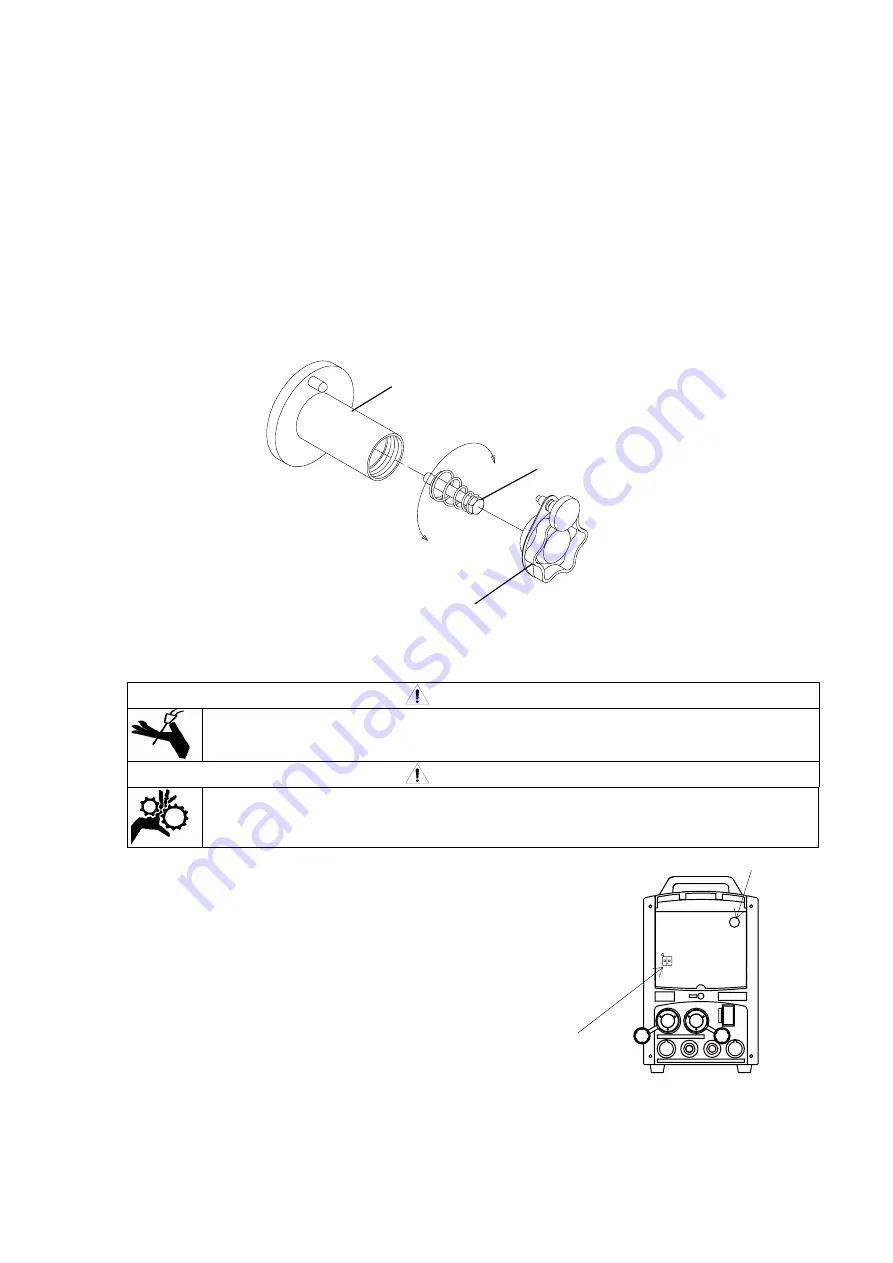
No. U5279
P. 13 / 25
7. WELDING PREPERATION (continued)
7.3 Adjusting of the wire reel hub
After performing inching operation, take care to adjust the brake of the wire reel hub to prevent the wire
from going too slack. The bake has been properly adjusted before shipment. Therefore, readjustment of
the brake is not required for welding in standard welding conditions.
How to adjust the wire reel hub
1. Detach the cap knob from the wire reel shaft.
2. Adjustment of the brake can be achieved by turning the hexagon bolt (M10).
7.4 Feeding Wire Feeding by Performing Inching Operation
WARNING
●
Do not look into the tip hole to check for the rate of wire feeding while inching.
CAUTION
●
Keep away your hands, fingers, hair or clothes from the rotating parts of the feed
roll, etc. to prevent you from being caught into the rotating parts while inching.
After straightening the welding torch, feed the wire by pressing
the INCHING key. (the INCHING lamp located at the upper right
of the INCHING key lights up). When the wire appears from the
end of the torch, press the INCHING key again (the INCHING
lamp goes out). Cut the wire at about 10 mm from the end of the
torch. Wire feed rate can be adjusted by turning the parameter
adjusting knob.
Wire reel shaft
Hexagon bolt (M10)
Cap knob
To brake more quickly,
turn the bolt clockwise.
To brake more slowly, turn
the bolt counter-clockwise.
インチング
INCHING key
Parameter adjusting knob