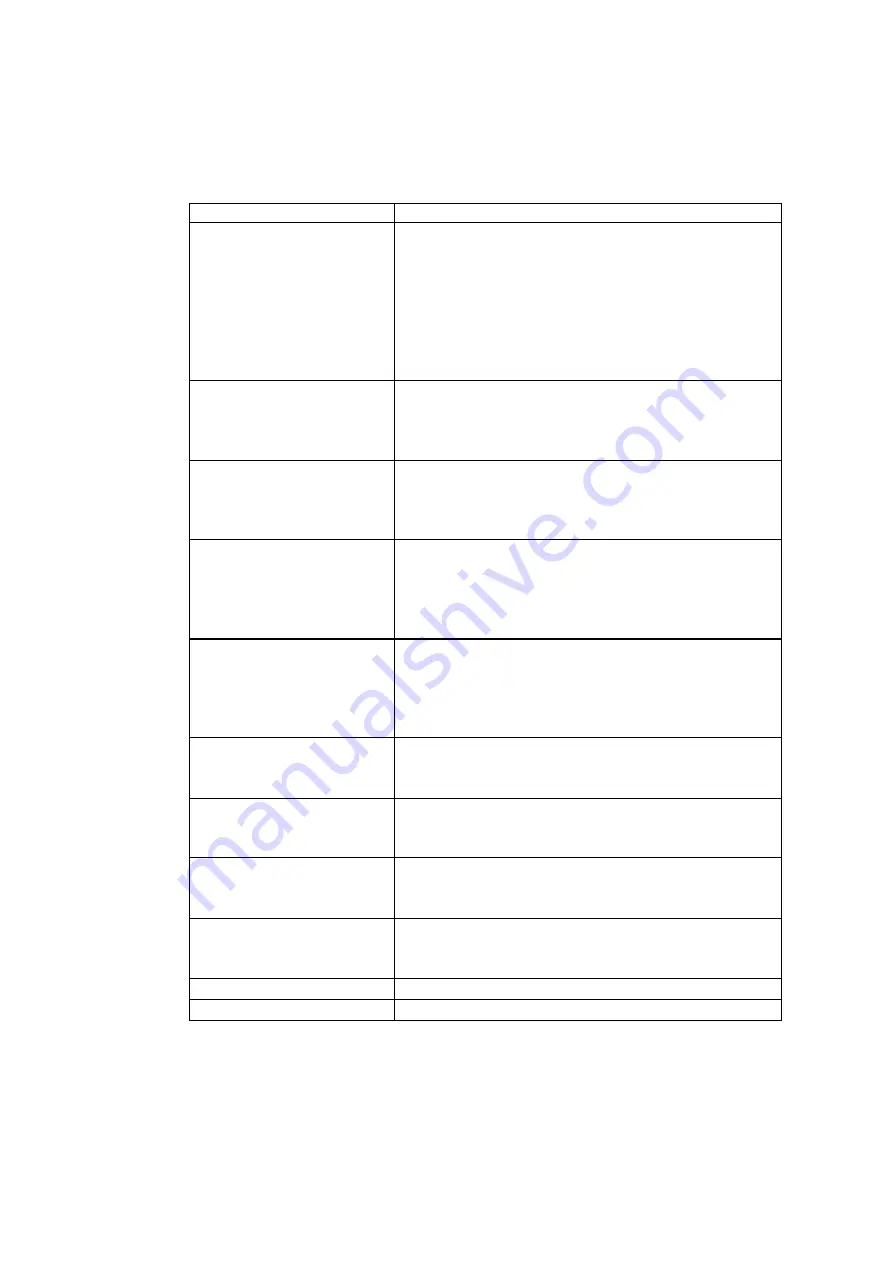
No. P10224
P. 25 / 47
10. WELDING OPERATION (continued)
10.7 WELDING CONDITIONS
●
If the improper welding conditions are set, the following problems will occur.
CAUSE TROUBLE
Welding current too large.
・
Deep penetration.
・
Holes or brakes on welded metal when welding thin plate
when welding thin plate.
・
Wide bead width.
・
Increase in excess metal length.
・
Increase in leg length.
・
Easy overlapping.
・
Bead dropping or undercut at some welding positions.
Arc voltage too high.
・
Long arc length.
・
Wide bead width.
・
Decrease in excess metal length.
・
Easy occurrence of blowhole.
Arc voltage too low.
・
Sticking through base metal and spatter.
・
Narrow bead width.
・
Shallow penetration.
・
High excess metal.
Welding speed too fast.
・
Narrow bead width.
・
Shallow penetration.
・
Low excess metal.
・
Easy undercut.
・
Easy occurrence of poor gas shield.
Wire extension too long.
・
Long arc length.
・
Large potential drop and output voltage decrease caused by
resistance heat generated from wire extension part.
・
Shallow penetration.
・
Easy generation of poor gas shield.
Wire extension too short.
・
Short arc length.
・
Deep penetration.
・
Spatter.
Torch angle too large.
・
Wide bead width and shallow penetration at angle of advance.
・
Easy occurrence of convex bead width and deep penetration
at angle of sweep back.
Penetration too shallow
・
Narrow bead width.
・
Shallow penetration.
・
Easy overlapping.
Penetration too deep.
・
Wide bead width.
・
Deep penetration.
・
Easy occurrence of hole or break (when welding a thin plate).
Rate of gas flow too high.
・
Easy lacking of lack of arc at low current.
Rate of gas flow too low.
・
Easy generation of poor gas shield at large current.