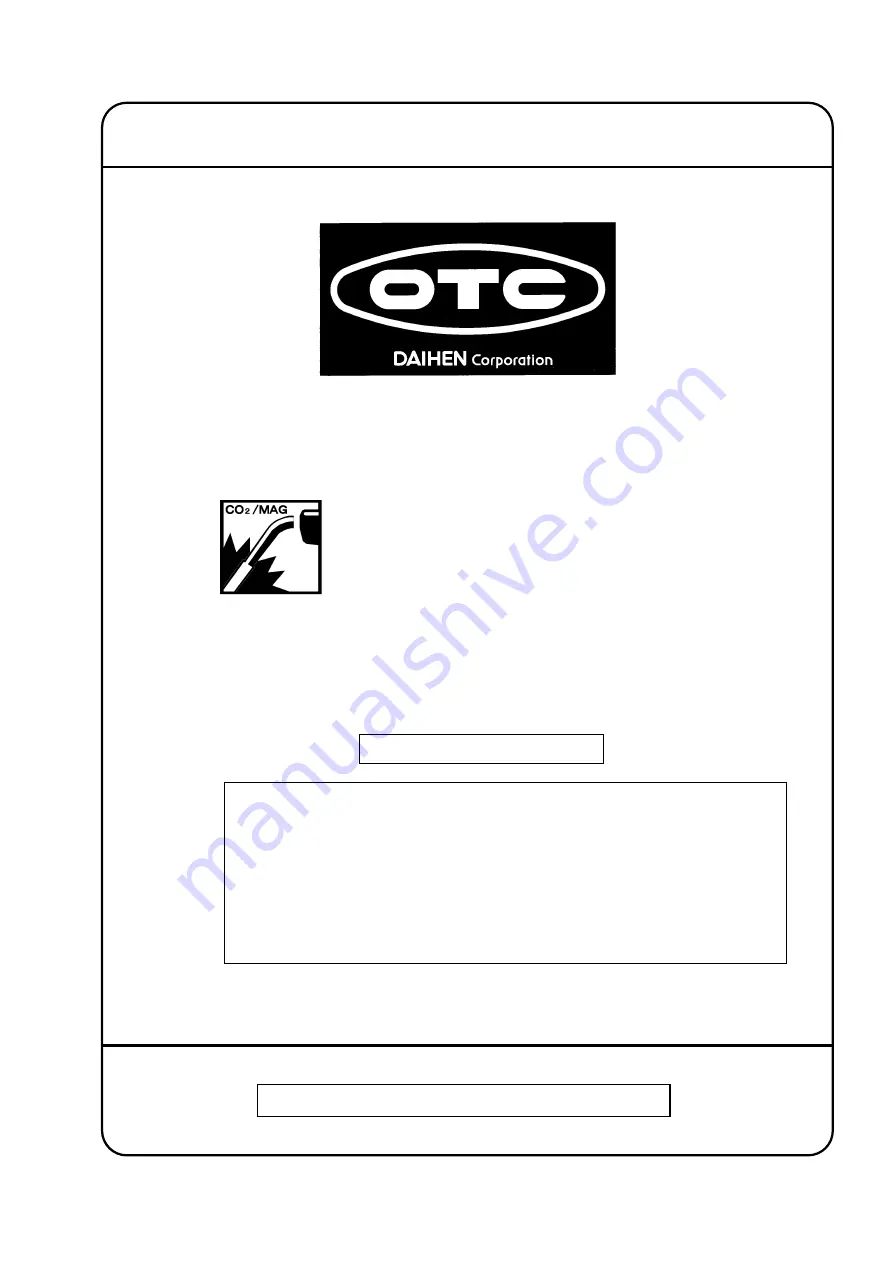
2P30161-4
OWNER'S MANUAL
FOR
DIGITAL INVERTER
CPVE-400/500
MODEL: CPVE-400 P30161/C1017
CPVE-500 P30162/C1018
INVERTER CONTROLLED WELDING POWER SOURCE
DO NOT DESTROY
IMPORTANT: Read and understand the entire contents of this
manual, with special emphasis on the safety material throughout
the manual, before installing, operating, or maintaining this
equipment. This equipment and this manual are for use only by
persons trained and experienced in the safety operation of
welding equipment. Do not allow untrained persons to install,
operate or maintain this equipment. Contact your distributor if you
do not fully understand this manual.
DAIHEN Corporation
WELDING PRODUCTS DIVISION
Upon contact, advise MODEL and MANUAL NO.
Wminfo