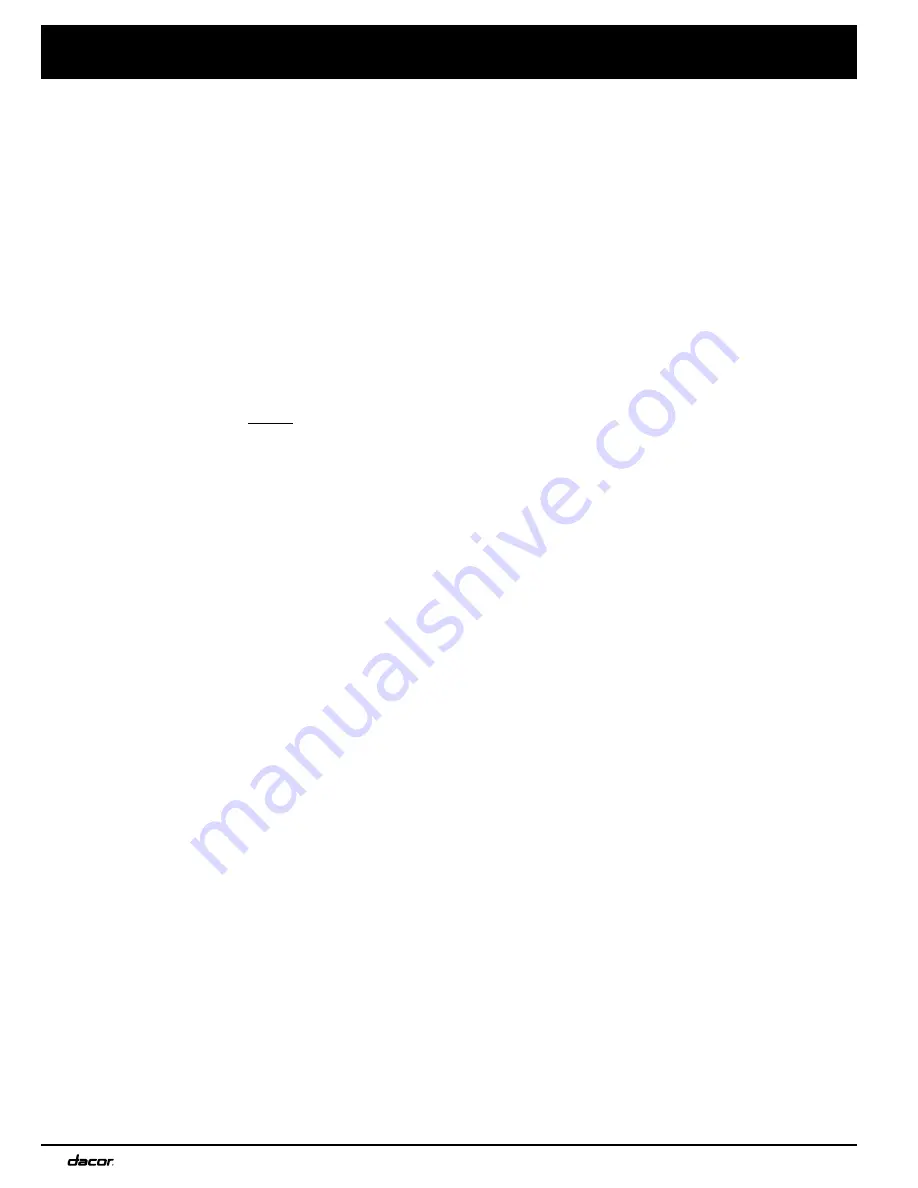
10
Ductwork Tips
Wherever possible, reduce the number of transitions, turns,
and sharp angles. Two staggered 45° angles are better
than one sharp 90° angle.
Keep turns as far away from the hood exhaust as possible,
and keep as much space between any bends as possible.
For best performance: use round duct instead of rectangu-
lar, especially when elbows are required.
If multiple elbows are used, try to keep at least 24 inches of
straight duct between each elbow.
Avoid using “S” or back-to-back adjacent elbows.
In extremely cold weather regions, use thermal breaks, i.e.,
short sections of non-metallic duct, to avoid indoor heat
loss. Locate the break as close as possible to the outside
pass-through point.
Do not use flexible metal duct. Do not use ductwork that is
smaller than what is advised in the tables.
• The hood exhaust connects to an 8-inch round duct.
You can
increase
the duct size over the duct run if
desired.
• To prevent a backdraft,
never decrease
the duct size
over the run. If existing ductwork is smaller than 8
inches in diameter, remove it and replace it with 8-inch
ductwork.
• Do not rely on tape alone to seal duct joints. Fasten
all connections with sheet metal screws, and tape all
joints with certified duct tape or foil tape.
• Use sheet metal screws as needed to support the
weight of the ducting.
• To prevent backdrafts, a damper at the duct outlet may
also be required.
Preparation and Setup
Summary of Contents for Distinctive DTHP30
Page 30: ...28 Notes ...
Page 31: ......