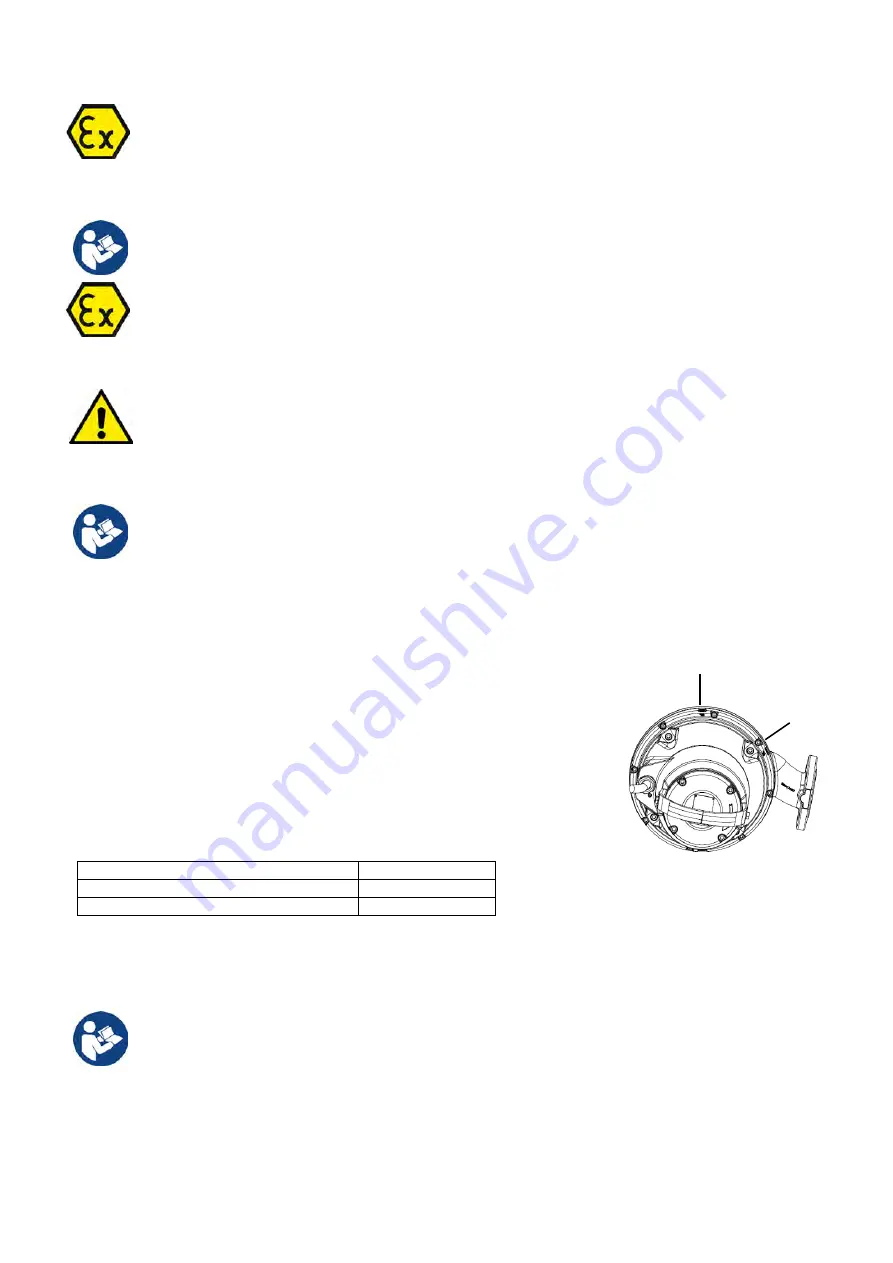
ENGLISH
28
The ball bearings used are sealed and lubricated, using a special lubricant for high temperatures (-40°C + 150°C).
Defective bearings may reduce the Ex safety.
•
O-rings and similar parts
During service/replacement, it must be ensured that the grooves for the O-rings as well as the seal faces have been cleaned before the
new parts are fitted.
Used rubber parts must not be reused.
Explosion-proof pumps must be checked by an authorized Ex workshop once a year.
•
Oil change
After 3000 operating hours or once a year, change the oil in the oil chamber as described below.
If the shaft seal has been replaced, the oil must be changed.
When loosening the screws of the oil chamber, note that pressure may have built up in the chamber. Do not remove
the screws until the pressure has been fully relieved.
•
Draining of oil
1.
Place the pump on a plane surface with one oil screw pointing downwards.
2.
Place a suitable container (approx. 1 litre), for instance made of transparent plastic material, under the oil screw.
Used oil must be disposed of in accordance with local regulations.
3.
Remove the lower oil screw.
4.
Remove the upper oil screw. If the pump has been in operation for a long period of time, if the oil is drained off shortly after the
pump has been stopped, and if the oil is greyish white like milk, it contains water. If the oil contains more than 20 % water, it is
an indication that the shaft seal is defective and must be replaced. If the shaft seal is not replaced, the motor will be damaged. If
the quantity of oil is smaller than the quantity stated, the shaft seal is defective.
5.
Clean the faces for the gaskets for oil screws.
•
Filling with oil
1.
Rotate the pump so that one of the two oil holes in a vertical position facing upwards.
2.
Pour the oil into the chamber. The suitable amount of oil is indicated by the second oil
venting hole (positioned beside the vertical filling hole). Once the oil has reached and
escapes from the hole at the side, the oil quantity is correct.
3.
Fit the oil screws with new gaskets.
The table shows the quantity of oil in the oil chamber of FKV and FKC pumps. Oil type: ESSO
MARCOL 152.
Motor type
Oil quantity [l]
up to 3kW 2poles / up to 2.2kW 4poles
0.5
from 4kW 2poles /from 3kW 4poles
0.95
8.2 Special maintenance
Special maintenance operations must be carried out exclusively by an assistance workshop authorised by
DAB Pumps.
8.3 Contaminated pumps
If a pump has been used for a liquid which is injurious to health or toxic, the pump will be classified as
contaminated.
If you are asking to have a pump repaired, you must contact the service centre to give them the details about the pumped liquid, etc.,
before sending the pump for repair. Otherwise, the service centre may refuse to accept the pump.
However, any application for service (no matter to whom it may be made) must include details about the pumped liquid if the pump has
been used for liquids which are injurious to health or toxic.
Before a pump is returned, it must be cleaned in the best possible way before it is returned.
Oil filling hole
(in vertical position)
Oil venting
hole
Fig. 11
Oil filling holes