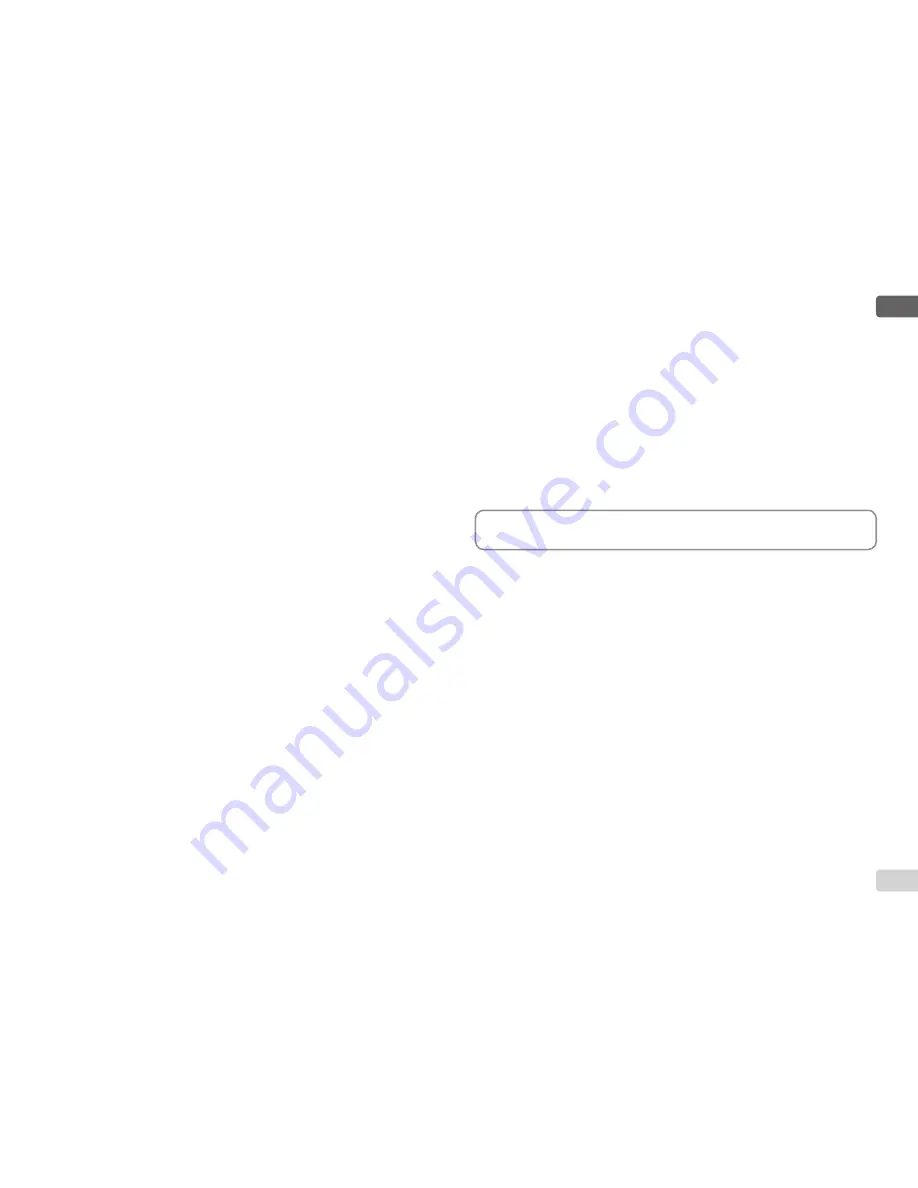
ENGLISH
GB
60
5.5.6 - T1: Low pressure delay (function detecting low pressure on
suction)
Sets the time when the inverter switches off after detecting low pressure
on suction (see Setting low pressure detection on suction par. 7.6.15.5).
T1 can be set between 0 and 12 s. The factory setting is 2 s.
5.6 -
Technical Assistance Menu
Advanced settings to be made only by skilled personnel or under the direct
control of the service network.
From the main menu, hold down simultaneously the “MODE” and “SET”
keys until “SP” appears on the display (or use the selection menu press
-
ing + or -). The menu allows you to view and modify various configuration
parameters: the MODE key allows you to scroll through the menu pages,
the + and – keys allow you respectively to increase and decrease the value
of the parameter concerned. Press SET to leave this menu and return to
the main menu.
5.6.1 - TB: Water lack blockage time
Setting the reaction time of the water lack blockage allows you to select the
time (in seconds) taken by the device to indicate the lack of water.
The variation of this parameter may be useful if there is known to be a
delay between the moment the motor is switched on and the moment it
actually begins to deliver. One example may be a plant where the suction
pipe is particularly long and there are some slight leaks. In this case the
pipe in question may be discharged and, even though water is not lacking,
the electropump will take a certain time to reload, supply the flow and put
the plant under pressure.
5.6.2 - T2: Delay in switching off
Sets the delay with which the inverter must switch off after switch-off con
-
ditions have been reached: plant under pressure and flow rate lower than
the minimum flow.
T2 can be set between 2 and 120 s. The factory setting is 10 s.
5.6.3 - GP: Proportional gain coefficient
Generally the proportional term must be increased for systems character
-
ised by elasticity (for example with PVC pipes) and lowered in rigid sys
-
tems (for example with iron pipes).
To keep the pressure in the system constant, the inverter performs a type
PI control on the measured pressure error. Depending on this error the
inverter calculates the power to be supplied to the motor. The behaviour
of this control depends on the set GP and GI parameters. To cope with
the different behaviour of the various types of hydraulic plants where the
system can work, the inverter allows the selection of parameters different
from those set by the factory. For nearly all plants the factory-set GP and
GI parameters are optimal. However, should any problems occur in ad
-
justment, these settings may be varied.
5.6.4 - GI: Integral gain coefficient
In the presence of large falls in pressure due to a sudden increase of the
flow or a slow response of the system, increase the value of GI. Instead,
if there are swings in pressure around the setpoint value, decrease the
value of GI.
5.6.5 - RM: Maximum speed
Sets a maximum limit on the number of pump revolutions.
5.6.6 - AY: Anti Cycling
As described in paragraph 9, this function is for avoiding frequent switch
-
ing on and off in the case of leaks in the system. The function can be
enabled in 2 different modes, normal and smart. In normal mode the elec
-
tronic control blocks the motor after N identical start/stop cycles. In smart
mode it acts on the parameter RP to reduce the negative effects due to
leaks. If set on “Disable”, the function does not intervene.
5.6.7 - AE: Enabling the anti-block function
This function is for avoiding mechanical blocks in the case of long inactiv
-
ity; it acts by periodically rotating the pump.
When the function is enabled, every 23 hours the pump performs an un
-
blocking cycle lasting 1 min.
5.6.8 - AF: Enabling the anti-freeze function
If this function is enabled the pump is automatically rotated when the tem
-
perature reaches values close to freezing point, in order to avoid break
-
ages of the pump.
IMPORTANT:
To obtain satisfactory pressure adjustments, you gener
-
ally have to adjust both GP and GI.