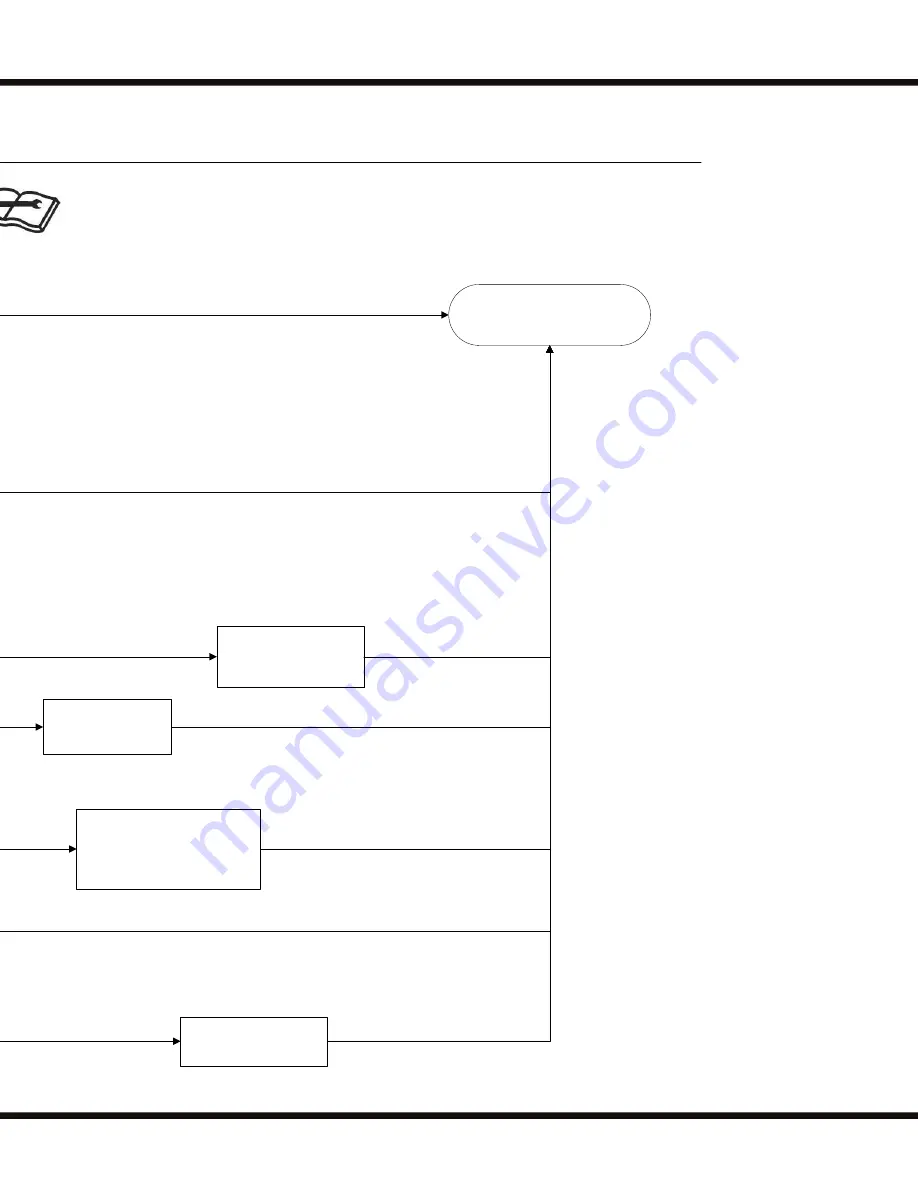
35
MAINTENANCE & TROUBLESHOOTING MANUAL
PS5.0-M REV B
SECTION 6
TROUBLESHOOTING FLOWCHARTS
No Left Turn & Right Turn
OK?
R1 Failure. Replace
Relay.
R2, R3, or R4 failure. Listen for
clicks, try switching relays around.
Replace relay(s).
No Right Turn & Left Turn
OK?
Does machine steer ?
(drive, elevate, lower OK)
Check for power connection.
See Hy-Brid Troubleshooting.
(Power connections at pump,
fuse, etc.)
No; Drive, elevate and
lower not operating
Consider Steer Limit Switch Adjustment
Check electrical connections at switch. Do a
continuity check on switch.
Replace limit switch and/or
readjust.
Consider relay failure, relay
block wiring.
Check steer actuator for
failure. Apply 24V to leads.
Replace actuator
Consider joystick failure or
wiring connection problem.
Contact Hy-Brid Lifts for further
troubleshooting
Consider damaged
main cable, main cable
connections at upper
and lower control.
(Check terminals #17 &
#22)
No; Steering
Not operating
properly
Check wire connections at actuator.
Pull test connections
—
if failure,
crimp on new connector(s)
Consider mode limit switch wiring or switch failure
(red and/or black wires) Continuity test on switch,
voltage test on red/black wires
Verify joystick
rocker switch
working properly.
WARNING
Any modification on this machine without
the express consent of the manufacturer
is prohibited.
WARNING
Failure to comply with safety precautions
may result in damage, injury, or death.
Refer to Maintenance Manual for
complete warnings
Flowchart: Pro Series-Steer
Revision A
Summary of Contents for HY-BRID LIFTS PRO PS-1030
Page 11: ...11 MAINTENANCE TROUBLESHOOTING MANUAL PS5 0 M REV B THIS PAGE WAS INTENTIONALLY LEFT BLANK ...
Page 37: ...37 MAINTENANCE TROUBLESHOOTING MANUAL PS5 0 M REV B SECTION 6 TROUBLESHOOTING FLOWCHARTS ...
Page 44: ...PRO SERIES PS 1030 PS 1430 PS 1930 44 SECTION 9 INSPECTION REPAIR LOG DATE COMMENTS ...
Page 46: ...PRO SERIES PS 1030 PS 1430 PS 1930 46 SECTION 9 INSPECTION REPAIR LOG DATE COMMENTS ...