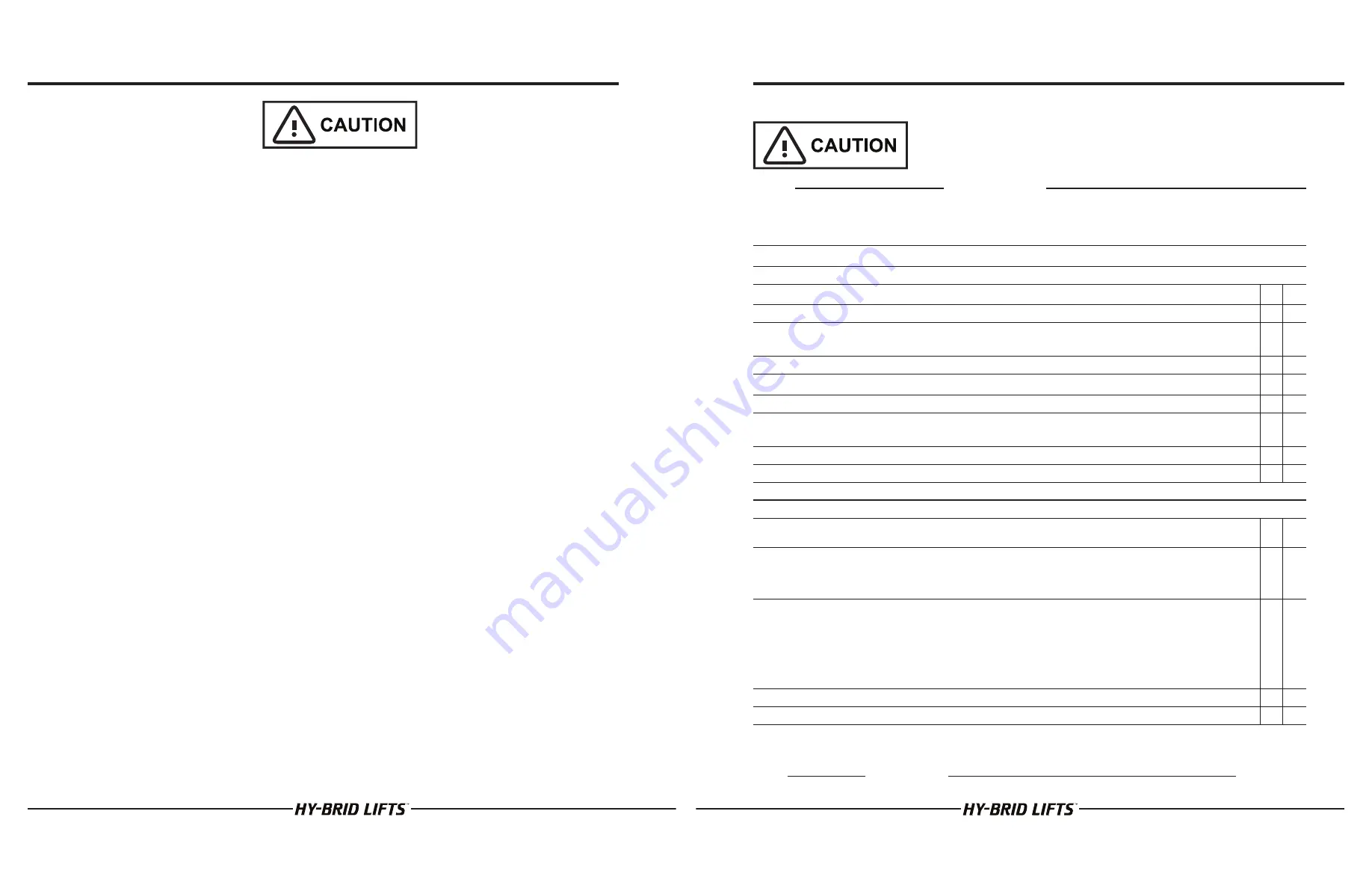
SECTION 3 | MAINTENANCE CHECKLISTS
FAILURE TO PERFORM INSPECTIONS AND PREVENTATIVE
MAINTENANCE AT RECOMMENDED INTERVALS MAY RESULT IN THE
UNIT BEING OPERATED WITH A DEFECT THAT MAY RESULT
IN INJURY OR DEATH OF THE OPERATOR.
Regular inspection and conscientious maintenance is important to efficient economical operation of this machine.
It will help to assure that equipment will perform satisfactorily with a minimum of service and repair. Make checks at
the stated intervals or more frequently if required by local operating conditions. The following inspection checklists
are required and included in this manual:
•
Pre-Start (Required before operation at each work shift)
•
Frequent (Required at intervals not more than three months)
•
Pre-Delivery/Annual (Required at intervals not more than twelve months)
The rated life of the machine is Light Intermittent Duty (typical use 10 years, 40 weeks per year, 20 hours per week,
5 load cycles per hour).
MAINTENANCE & TROUBLESHOOTING
HB-P4.5/HB-P5.0
SUPO-648
REV G
14
SECTION 3 | MAINTENANCE CHECKLISTS
3.1 | PRE-START INSPECTION CHECKLIST
THIS CHECKLIST MUST BE USED AT THE BEGINNING OF EACH SHIFT OR
AFTER EVERY SIX TO EIGHT HOURS OF USE. FAILURE TO DO SO COULD
AFFECT THE SAFETY OF THE OPERATOR.
MODEL: SERIAL NUMBER:
•
Keep inspection records up-to-date.
•
Record and report all discrepancies to your supervisor.
•
A dirty machine cannot be properly inspected.
Y — Yes/Acceptable N — No/Unacceptable R — Repaired
Description
Y
N
R
VISUAL INSPECTIONS
Check that there are no damaged, dented, or bent structural members.
ڧ ڧ ڧ
There are no loose or missing parts.
ڧ ڧ ڧ
Check that warning and instructional labels are legible and secure. Ensure that load capacity is clearly
marked.
ڧ ڧ ڧ
Check the platform rails and safety gate for damage.
ڧ ڧ ڧ
Platform and base controls are not missing, damaged, or disconnected.
ڧ ڧ ڧ
Electrical cables and wires are not torn, frayed, or disconnected.
ڧ ڧ ڧ
Hydraulic hoses are not torn or loose, and there are no leaks. Check that hoses and cables have no
worn areas or chafing.
ڧ ڧ ڧ
Check the tires for damage.
ڧ ڧ ڧ
Check that all snap rings are secure in grooves on pivot pins.
ڧ ڧ ڧ
FUNCTIONAL TESTS
Gate closes automatically and latches (alignment can be adjusted with screw-on toe board or
railing).
ڧ ڧ ڧ
Platform Controls — Check all switches and push buttons for proper operation:
Up/Down Controls (Elevates, Lowers, Enable button must be pressed)
ڧ ڧ ڧ
Emergency Stop (stops all movement)
ڧ ڧ ڧ
Base Controls — Check all switches and push buttons for proper operation
Emergency Stop (stops all movement)
ڧ ڧ ڧ
Key Switch (Selects Platform Control, Ground Control, or Off)
ڧ ڧ ڧ
Alarm (Not damaged, sounds for descent)
ڧ ڧ ڧ
Up/Down Rocker Switch (Elevates, Lowers)
ڧ ڧ ڧ
Wheels: Front and rear wheels rotate freely.
ڧ ڧ ڧ
Brakes engage and hold when platform is elevated.
ڧ ڧ ڧ
DATE:
INSPECTED BY:
MAINTENANCE & TROUBLESHOOTING
HB-P4.5/HB-P5.0
SUPO-648
REV G
15