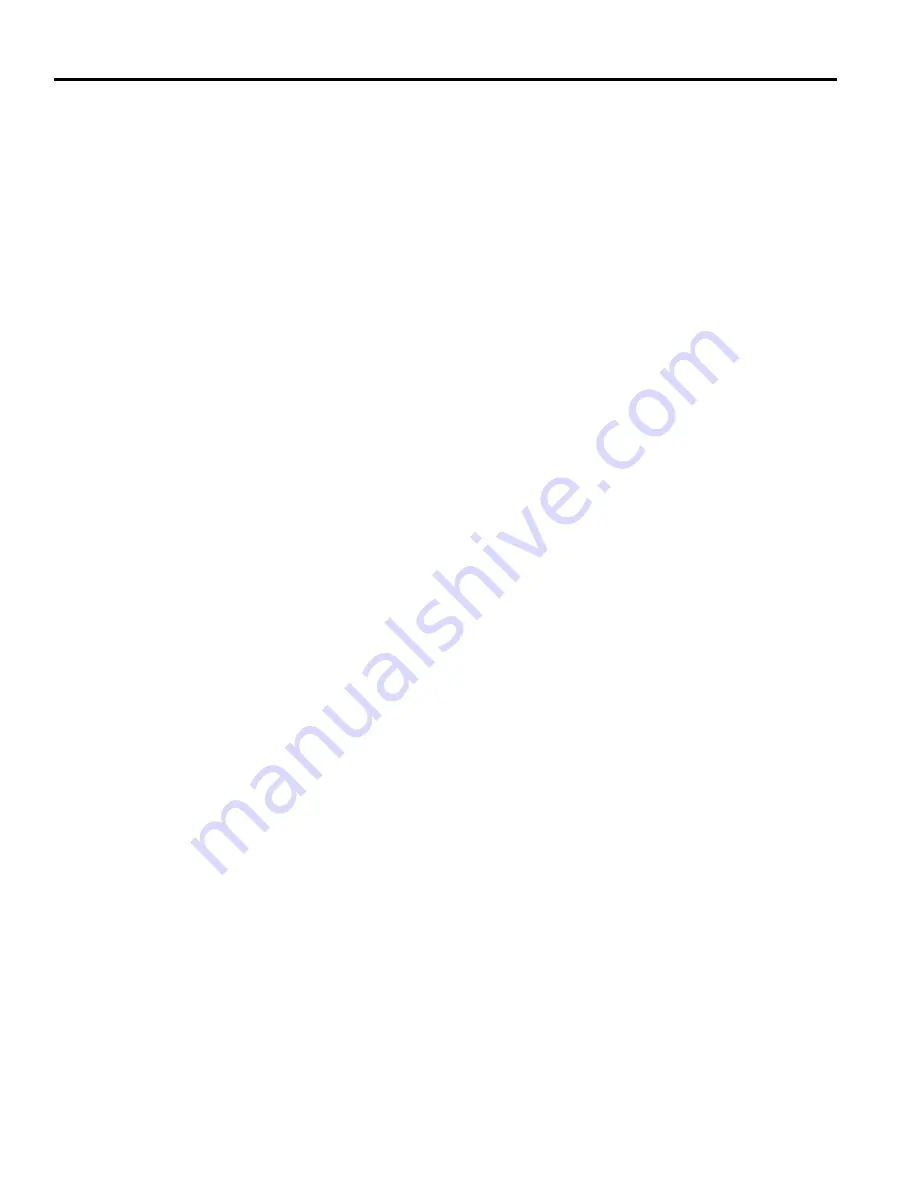
6 SPRAYER OPERATION
26
• Check plastic pressure gauge tube for kinks,
breaks or blockage, repair as needed. To clear a
blocked tube (packed with dry powder):
a.
Put some clean water in the spray tank, 2 to 5
gallons (7.6 to 18.9 L) is sufficient. Turn sprayer
on and set rpm's to 3000 on truck.
b.
On the back-side of the console is a metal tube
receiver with an 1/8 in. tube engaged. Push the
tube and top of the metal coupler in with your
thumb and index finger, while holding the metal
ring in, pull the tube out with your other hand.
Point end of tube away from unit and your face
and allow debris to clear from tube.
c.
If unsuccessful, remove other end of tube from
Boom Valve inlet. Use a rubber tipped air nozzle
to force high pressure air through the tube. If still
unsuccessful, replace the tube with a new piece,
and start flushing the new tube after each spray
application.
• Move back to the boom area at the rear of the
sprayer. Inspect the connector plugs on the
motorized valve harness, they should be tight
against the valve body tighten if necessary (there
should be no prongs showing from the valve).
• Check valve mating joints (seams) for leakage. if a
leak is detected, tighten the nuts on the 4 guide rod
bolts (there are o-rings in each joint area, Do Not
tighten too tight. If the leak persists, separate the
valve bodies and replace the o-rings with new
ones.
• Make sure the U-clips on the boom feed barbs and
metered by-pass valve are pushed in and secured
(leakage can result if U-clips are not in place).
• Follow the boom hoses from each motorized valve
to the corresponding boom section, make sure the
brass compression clamp (pipe saddle feeder) with
the nylon fitting is snug against the SST tube and
the pipe saddle is parallel to the ground (improper
saddle alignment can cause reduced flow during
large tip use, adjust as necessary).
Move to the control console, Listen carefully as you
perform the next series of checks.
• Push up on the pressure-adjust toggle switch, the
Servo motor on the yellow striped valve should run.
Reverse toggle switch position, verify motor works
in both directions.
• Push the master power toggle to the "ON" position,
check the switches one-at-a-time for boom 1, then
boom 2, then boom 3, checking switches in both
directions. Verify each blue striped valve works in
both directions.
Raven SCS330 and SCS440 Boom Control
System.
• Procedures are similar to the motorized valve
control, refer to the manual supplied with the
Raven Accessory for test procedures.
• Wipe any debris from the console using a damp
rag and mild soap.
• Verify your pre-set calibration numbers, do they
match your records sheet in the Raven Manual?
Modify any numbers that do not match.
• Verify tip size in the boom is correct based on your
desired spray speed, tip spacing, and target
output.
• Make sure all harness connectors on the back of
the box, at the flow meter, and at the flow regulator
servo valve are secure.
• Inspect drive-line speed sensor assembly, Remove
any debris, especially metal shavings, from the red
& black magnet assemblies on the drive-line (the
metal particles can affect the pick-up sensors
ability to read the signal, resulting with inaccurate
speed readings and/or bad calibration settings by
the computer).
• Place control box power switch to the "manual"
position. Push the master power toggle to the "ON"
position, check the switches one-at-a-time for
boom 1, then boom 2, then boom 3, checking
switches in both directions. Verify each blue striped
valve works in both directions.
• If the Raven system is equipped with the RADAR
speed sensor, refer to the Raven Manual for check-
list and test procedures.
5.
Optional accessories that may be installed.
Proceed with the check list for each accessory that
has been installed on the Spraytek. Refer to the
accessory manuals for adjustment and set-up
procedures.
Summary of Contents for Spraytek DS175
Page 35: ...NOTES 7 35 7 NOTES...