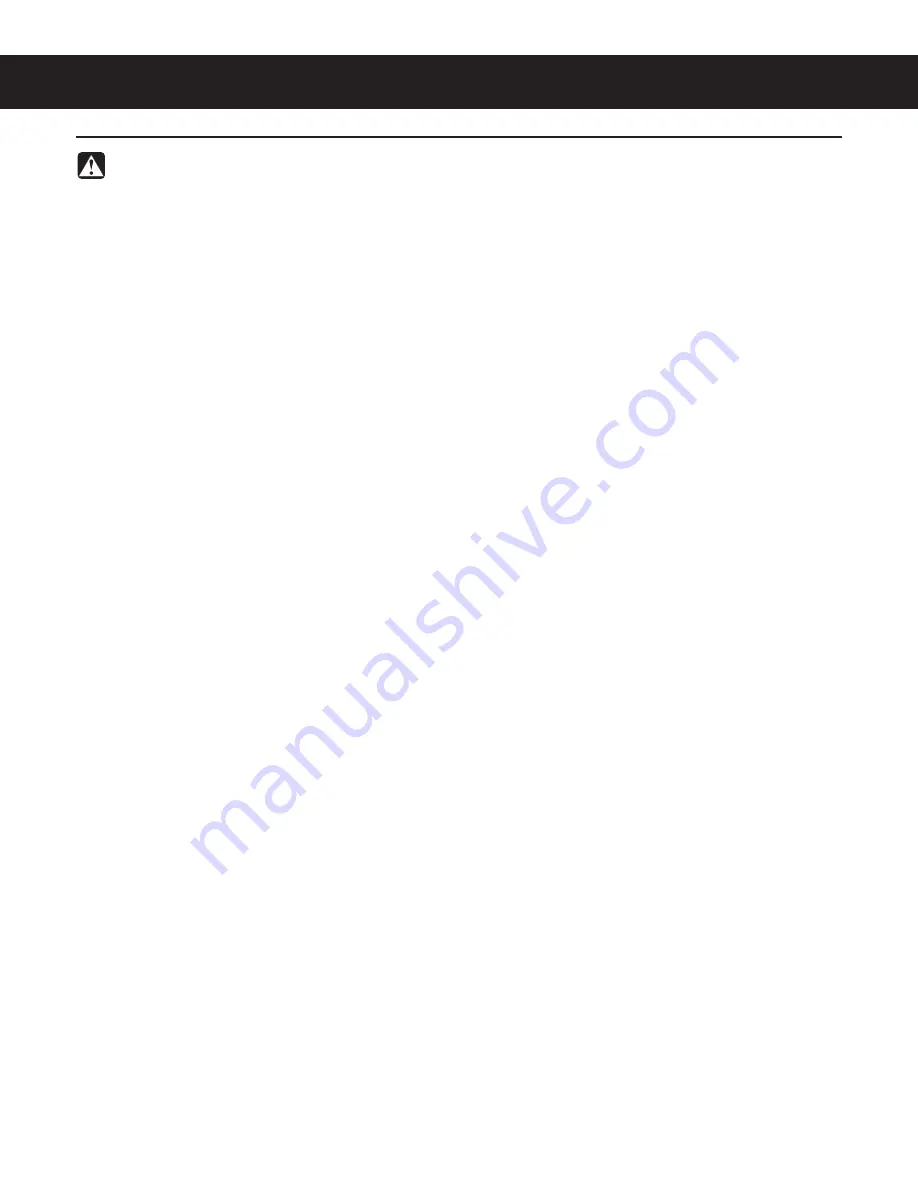
WARNING:
Electric Shock Hazard -
the following procedures are to be performed only by a quali
m
ed service technician.
Turn off power when replacing components. Neither Wilbur Curtis Co., Inc. nor the seller can be held
responsible for the interpretation of this information, or any liability in connection with its use.
Scald and Burn Hazard -
keep body parts clear of hot surfaces during troubleshooting.
Troubleshooting Guidelines
• An urn that is not level may not function properly. Make sure the urn is properly leveled before proceeding.
• This troubleshooting guide identi
m
es some, but not all, of the possible causes for common problems that can
occur.
• Use this troubleshooting guide along with the appropriate
ELECTRICAL SCHEMATIC.
No Power - Nothing Works
1 Make sure the circuit breaker for the circuit supplying power to the urn is not tripped and is turned on. On units
with both a 120 Volt and 220 Volt power supply, make sure both circuits are turned on.
2 On urns with a power plug, make sure it is connected to the power receptacle.
3 Make sure that the main power toggle switch on the bottom of the control box is turned ON.
4 Remove the fuse on the front of the control box and make sure it is not blown.
5 Remove the electrical box cover and verify that all wires from the power cord are properly connected inside
the unit. Check to make sure the wires are not burned/overheated. Check chassis ground.
Urn Does Not Start to Brew When BREW BUTTON is Pressed
If the urn starts to brew when the BREW BUTTON is press, but stops brewing when it is released, see
Brewing
Stops When BREW BUTTON is released
.
1 First check the water level in the water jacket. If the water level is low, see
Water Jacket Does Not Fill
.
2 Press the BREW BUTTON and check for power across the terminals of the brew pump. If there is power to the
pump, but water does not
n
ow, replace the pump.
3 If the brew pump is not getting power,
m
rst check for faulty wiring and connections between the timer and the
pump.
4 If the wiring is OK, check for power across terminals 2 and 3 and across terminals 3 and 9 on the timer.
5 If power is being supplied to the timer, check to make sure power is supplied to pin 5 of the timer when the
BREW BUTTON is pressed. If power is being supplied to all the terminals checked in steps 4 and 5, but there
is no power supplied to the pump when the BREW BUTTON is pressed, replace the timer. After replacing the
timer, set the timer as instructed in the
Setting the Timer
section on the following page.
Brewing Stops When BREW BUTTON is Released
The brew light stays on only while the switch is pressed, but turns off when released and water comes out of the
spray head only while the switch is kept pressed. Normally, the timer should reset itself to the N. O. position after
every brewing cycle but if it fails to reset, brewing will stop when the button is released.
1 Turn off power to the urn.
2 Disconnect the wires to terminals 8 and 9 on the timer.
3 Using a multi-meter, check for continuity between terminals 8 and 9 on the timer. If there is continuity, the timer
is faulty and must be replaced. After replacing the timer, set the timer as instructed in the
Setting the Brew
Timer
section on the following page.
TROUBLESHOOTING GUIDE
TG20
RU URN, CONTROL CIRCUIT, TROUBLESHOOTING GUIDE
ø
030921B