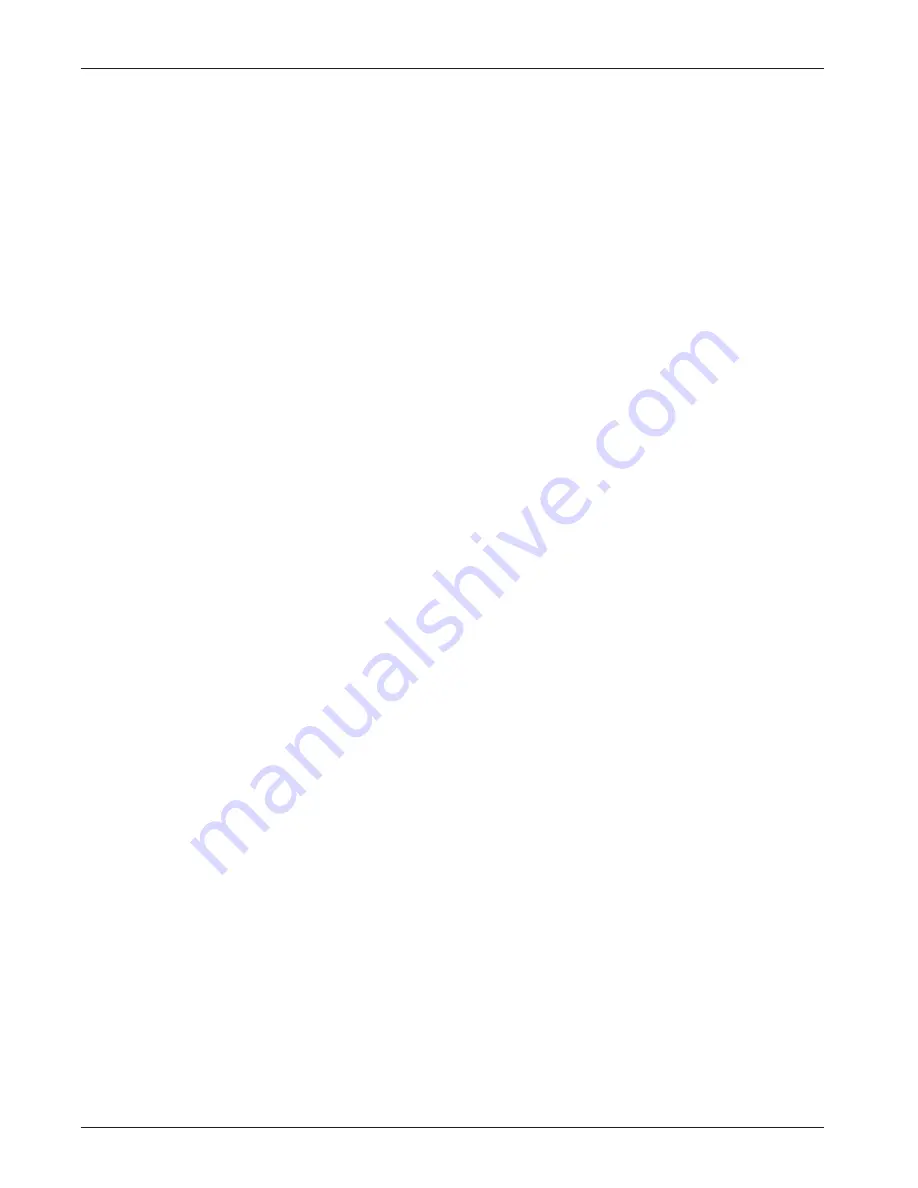
vi
Curtis 1228 Manual,
Rev. F
FIGURES
FIG
.
1:
Curtis 1228 electronic motor controller ....................................1
FIG
.
2:
Mounting dimensions, Curtis 1228 controller .........................4
FIG
.
3a: Standard wiring configuration, with seat lift .............................6
FIG
.
3b: Alternative wiring configuration, with seat lift ..........................7
FIG
.
4a: Standard wiring configuration, without seat lift ........................8
FIG
.
4b: Alternative wiring configuration, without seat lift .....................9
FIG
.
5:
Wiring for 5K
Ω
, 3-wire potentiometer ..................................10
FIG
.
6:
Wiring for 5V throttle ............................................................11
FIG
.
7:
Wiring for Curtis ET-XXX electronic throttle ........................11
FIG
.
8:
Wiring to inhibit operation during battery charging ..............13
FIG
.
9:
Effect of adjusting the neutral deadband parameter ................24
FIG
.
10: Effect of adjusting the throttle gain parameter ........................25
FIG
.
11: Ramp shape (throttle map) for controller
with maximum speed set at 100% ..........................................26
FIG
.
12: Ramp shape (throttle map) for controller
with maximum speed set at 60% ............................................27
TABLES
TABLE
1:
Programmable throttle input signal types ..........................22
TABLE
2:
Status LED fault codes ......................................................45
TABLE
3:
Troubleshooting chart .......................................................46
TABLE
D-1: Parameter index .............................................................. D-1
TABLE
E-1: Specifications, 1228 controller ........................................E-1
FIGURES / TABLES
Summary of Contents for MultiMode 1228
Page 2: ......