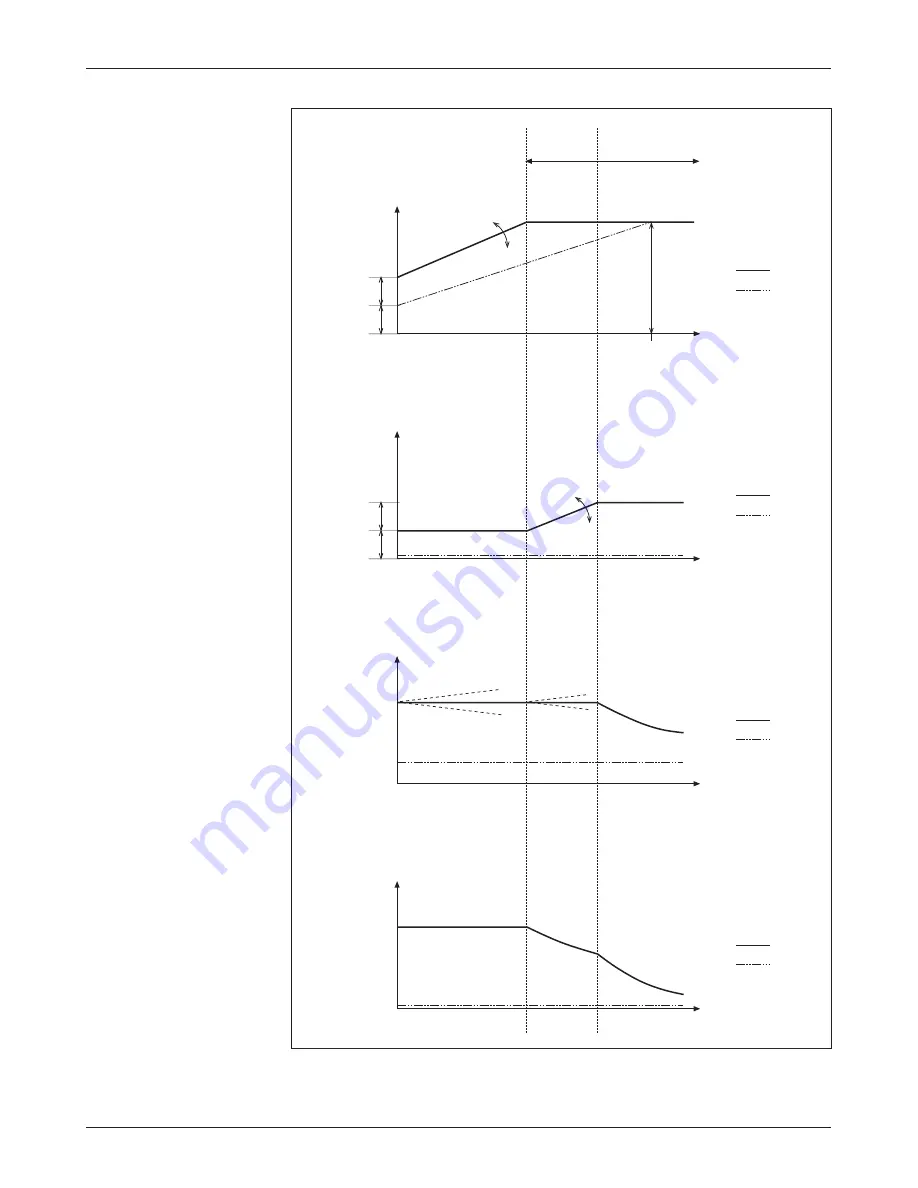
Curtis 1230 Manual,
Rev. C
37
3 — PROGRAMMABLE PARAMETERS:
Motor Control Parameters
Fig. 16
Motor control pa-
rameters and their effect on
operating characteristics.
HIGH SPEED
CONSTANT TORQUE
CONSTANT
POWER
MOTOR
VOLTAGE
(rms)
FREQUENCY
Field Weakening
Accel Slip Voltage
Min Motor Voltage
+
-
Accel Compensation
Nominal Motor
Vo
lta
ge
Nominal
Motor
Frequency
Full Load
No Load
SLIP
FREQUENCY
(Hz)
FREQUENCY
Pull Out Slip
Accel Slip
+
-
Slip Boost
Full Load
No Load
MOTOR
CURRENT
(rms)
FREQUENCY
Slip Boost:
Full Load
No Load
TORQUE
FREQUENCY
Full Load
No Load
Accel Compensation:
too high
too low
too high
too low
Summary of Contents for MultiMode 1230
Page 2: ......