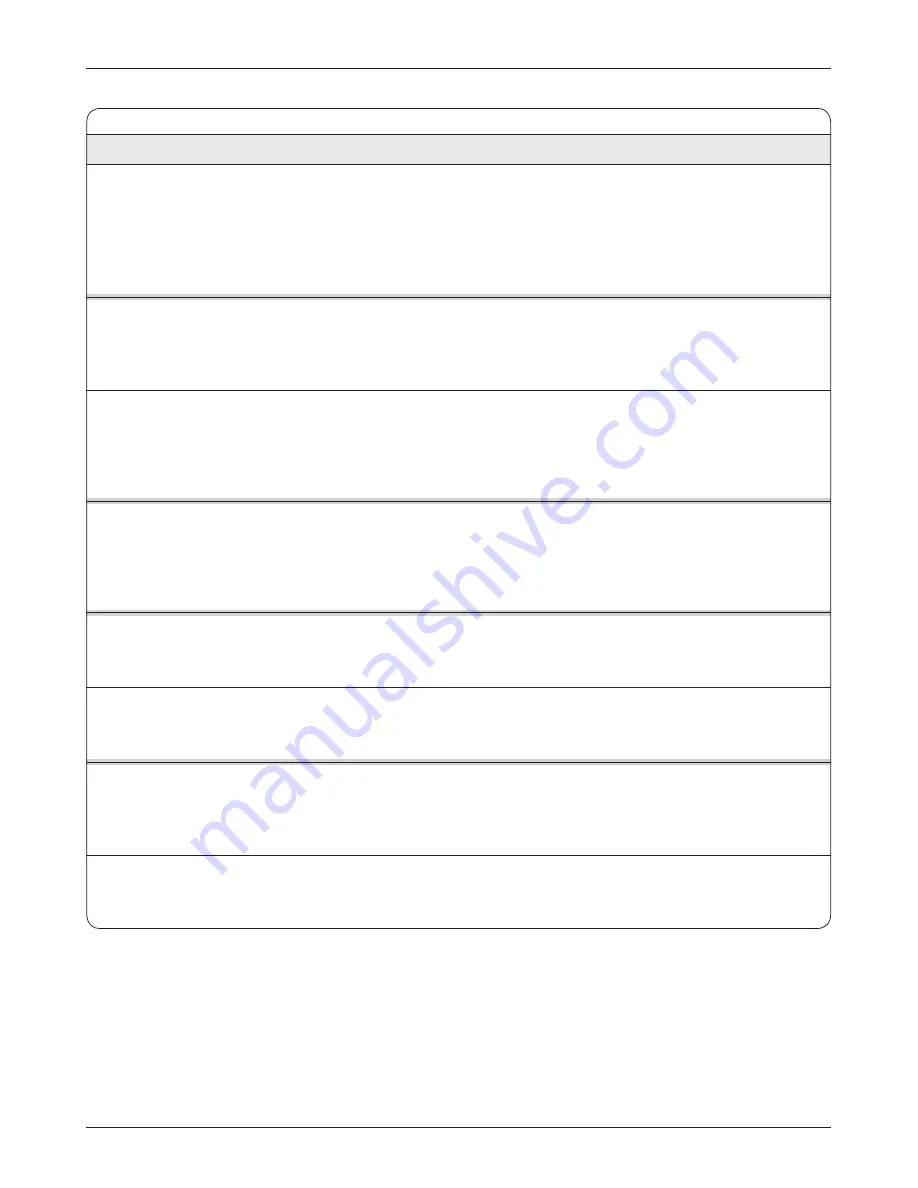
Curtis 1230 Manual,
Rev. C
35
3 — PROGRAMMABLE PARAMETERS:
Motor Control Parameters
MOTOR MENU
ALLOWABLE
PARAMETER
RANGE
DESCRIPTION
Min Motor Voltage
0.0–6.0 V
Defines the starting point of the V/f profile. This voltage is applied to the
motor at 0 RPM if no (or very low) torque is demanded.
Increasing this parameter can improve low speed behavior, because
the motor will have flux even at zero throttle request. However, if the
parameter is set too high, the motor idle current will be too high, reducing
efficiency and increasing the motor temperature.
Nominal Motor Voltage
7–30 V
This parameter should initially be set according to motor nameplate data.
The nominal motor voltage parameter and the nominal motor frequen-
cy parameter work as a pair to define the slope of the V/f profile.
Note: If set too high, excessive current can damage the motor.
Nominal Motor Frequency
20–400 Hz
This parameter should initially be set according to motor nameplate data.
The nominal motor voltage parameter and the nominal motor frequen-
cy parameter work as a pair to define the slope of the V/f profile.
Increasing the nominal motor frequency makes the V/f profile less
steep and reduces the no-load motor current.
Max Motor Speed
1000–10000 RPM
Defines the maximum motor RPM at full throttle and a 100% setting of
the M1/M2 maximum speed parameter. This parameter can be used to
achieve identical fleet top speed and to limit vehicle and motor speed to
the safe operating area even when running downhill.
Note: If set too high, the bearings and gearbox can be damaged.
Number of Motor Poles
2–8
This parameter must be set according to motor nameplate data. It is used
in calculating the motor output frequency based on the measured encoder
input frequency.
Encoder Pulses/Rev
32–128
This parameter must be set according to motor nameplate data. It is used
in calculating the motor output frequency based on the measured encoder
input frequency.
Swap Encoder Direction
OFF
/
ON
If the speed encoder A and B signals are wired backwards, this parameter
can be used to change the sign of the measured motor speed. It has the
same effect as physically swapping the A and B wires on the encoder
inputs (J2 Pins 2 and 4).
Failsafe Delay
2–20 sec.
If the motor is turning faster than desired, or in the opposite direction, the
controller will shut down the motor and engage the electromagnetic brake
after the programmed failsafe delay.
Summary of Contents for MultiMode 1230
Page 2: ......