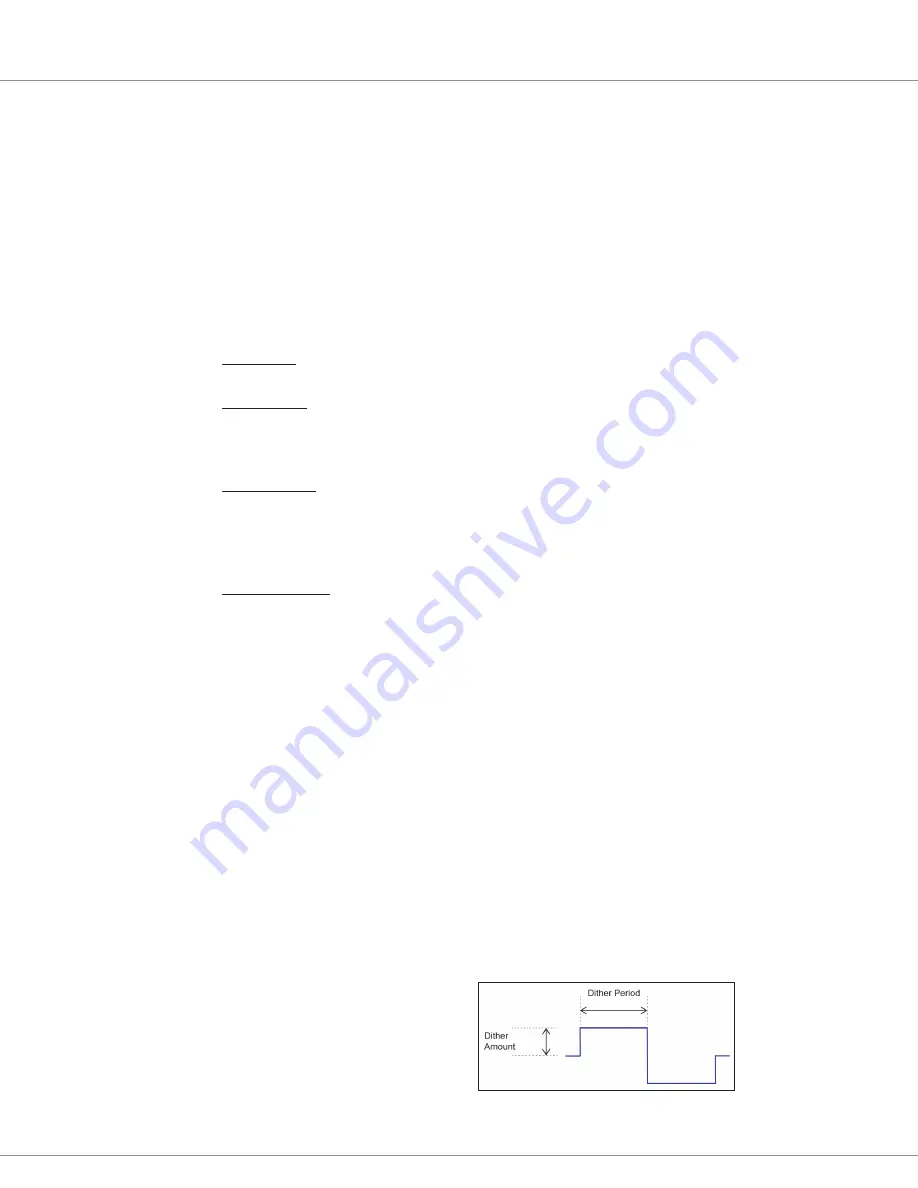
2 — INSTALLATION SPECIFICATIONS AND WIRING
Curtis Model 1351 – December 2018
pg. 14
PWM (coil-voltage-current/PV) Drivers
Drivers 1 through 10 utilize a low side quarter-bridge topology to drive inductive loads connected to
the Coil Return (B
+
). These are high-frequency pulse width modulation (PWM) drivers. Via parameter
settings, each has one of four operating modes: Off, Direct PWM, Voltage Compensated, and Current
Control. The drivers can control (sink) up to 3 amperes, although the 15 total drivers have a combined
current limit of 23 amperes (when using both Coil Return pins 11 & 12*). All inductive loads shall be
connected to the coil return (pins 11 & 12), which provides flyback diode protection. Resistive and
RC (inrush) loads shall not exceed three amps (peak). Each driver offers current measurement, output
state monitoring, and open/short fault detection. During setup and development, use the Test feature
(via VCL) to verify the fault detection of the driver circuits and external load connections. Each driver
is protected against shorts to B
+
or B
−
.
Off (Open)
The output driver FET is off (non-energized). Use this mode to disable the driver
output to allow the pin usage as an input.
Direct PWM
The Direct PWM mode allows the driver to produce PWM as commanded.
FET and wiring diagnostics are performed in this mode. The PWM produced
is equal the command percentage by directly writing to the variable
Driver_X_
Command
, where the value of 0 – 1000 commands from 0.0 – 100.0% PWM.
Voltage Comp
The Voltage Compensated mode continuously regulates the driver PWM based
on the command, the
Nominal Voltage
setting and the present battery voltage in
an attempt to provide a constant average voltage at the output. FET and wiring
diagnostics are performed in this mode. Initial and continuous PWM % timing
control is applied. The command is a % of nominal voltage desired at the output.
Current Control
The Current Regulated Mode interprets the command as a load current
request. This mode uses the feedback from current shunts to regulate (using a
PI controller) the PWM and thus provide the requested load current. Use this
mode to control Proportional Valves. It requires several additional features for
proper position control: Dither, Min/Max current settings, and PI gain settings.
On a normally closed valve, the Maximum current will provide a full open valve
and minimum current commands a fully closed valve. Setting the minimum
current above zero amps allows the valve to be quickly energized, and ready to
move quickly when commanded. Use the Maximum Current setting to calculate
the dither amount.
A 0.0% command will command zero current and the FET will be completely
off (irrespective of the Minimum setting). 0.1% will command a jump to the
Minimum Current and from there the current will linearly increase to Maximum
Current at 100% command.
Dither provides an amount of cyclically changing current to vibrate the solenoid
and keep it from “sticking” in one position. Without dither, it is harder to make
small adjustment in the proportional valve position. Dither has both a frequency
and amount. Note that the PI controller gains are critical in controlling dither
and should be adjusted to ensure the dither is properly generated.
Dither Waveform (
current control/proportional valve mode
)