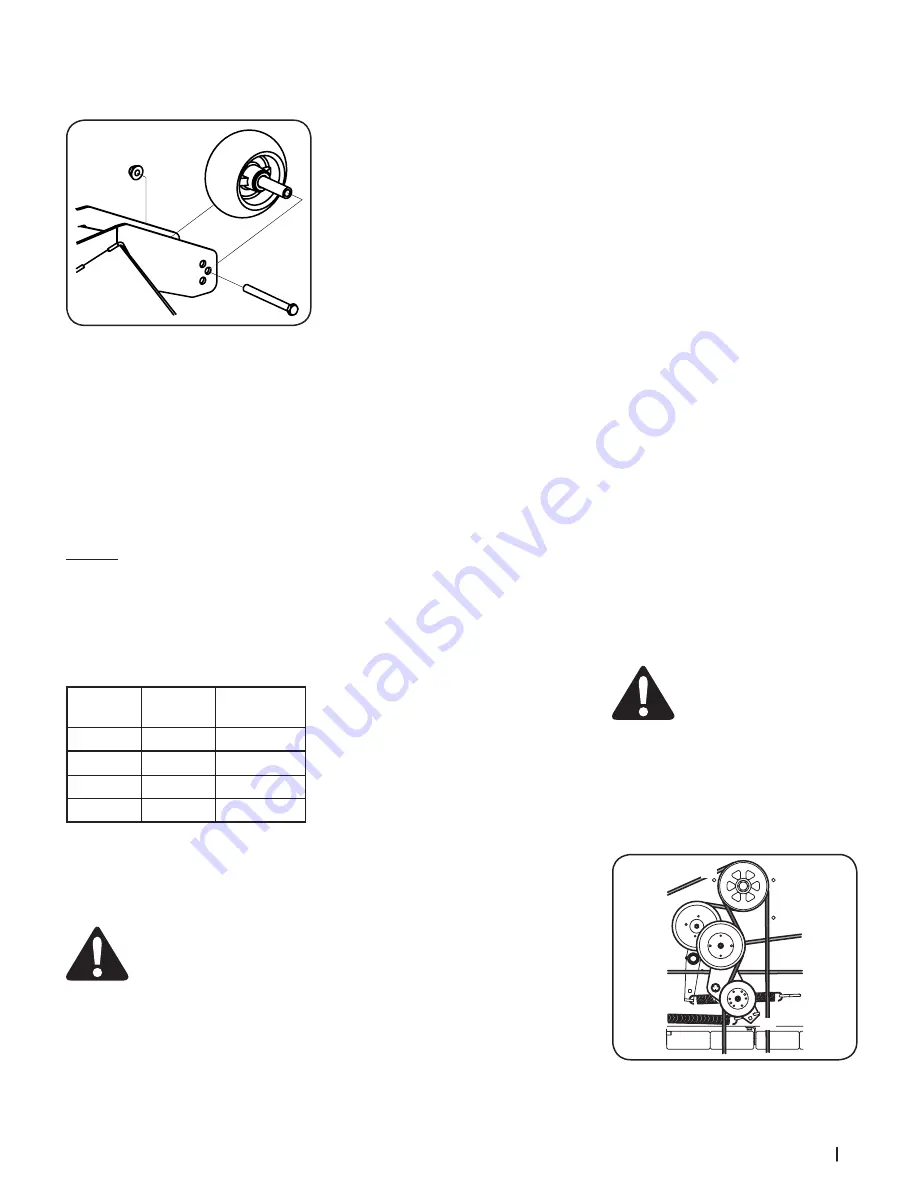
25
S
ection
4 — S
ervice
2.
Remove the lock nut (a) securing one of
the front gauge wheel (b) to the deck.
Remove the front gauge wheel (b), hex
screw (c) and spacer (d). See Figure 4-10.
(a)
(b)
(c)
(d)
(e)
Figure 4-10
NOTE:
There are a pair of front gauge
wheels on the nose of the 54” and 60”
decks.
3.
Insert the hex screw (c) into the one of
three index holes in the front gauge wheel
bracket (e) that will give the front gauge
wheel (b) a 1⁄4-1⁄2” clearance with the ground.
4.
Note the index hole of the just adjusted
front auge wheel (b), and adjust the other
front gauge wheel (b) into the respective
index hole of the other front gauge wheel
bracket (e).
Service
Charging the Battery
Test and, if necessary, recharge the battery after
the tractor has been stored for a period of time.
•
A voltmeter or load tester should read
12.6 volts (DC) or higher across the
battery terminals. See Figure 4-11.
Figure 4-11
•
Charge the battery with a 12-volt battery
charger at a MAXIMUM rate of 10 amps.
Jump Starting
WARNING!:
Failure to use this
starting procedure can cause
sparking, and the gases in the
battery to explode.
1.
Connect the end of one cable to the
disabled machine battery’s positive
terminal; then connect the other end
of that cable to the booster battery’s
positive terminal.
2.
Connect one end of the other cable to
the booster battery’s negative terminal;
then connect the other end of that cable
to the frame of the disabled tractor, as
far from the battery as possible.
Voltmeter
Reading
State of
Charge
Charging
Time
12.7
100%
Full Charge
12.4
75%
90 Min.
12.2
50%
180 Min.
12.0
25%
280 Min.
3.
Start the disabled tractor following the
normal starting instructions previously
provided; then disconnect the jumper
cables in the exact reverse order of their
connection.
4.
Have the tractor’s electrical system
checked and repaired as soon as
possible to eliminate the need for jump
starting.
Servicing Electrical System
Fuse
There are two fuses located inside the left
console. Lift the seat and look down at the left
console to find the location of the fuses. One
30 amp fuse for the power steering and one
25 amp fuse the ignition, PTO, etc. These are
standard plug-in type automotive fuses. Always
use the same capacity fuse for replacement.
Check the 30 amp fuse if the power steering is
not working and check the 25 amp fuse for all
other electrical problems.
If you have a recurring problem with blown fuses,
have the tractor’s electrical system checked by
your Cub Cadet Service Dealer.
Safety Interlock System & Switch
Operation Checks
The following operational checks should be
made daily:
PTO Switch
1.
Sit in the operator’s seat. With the drive
levers in the neutral position and the
parking brake engaged, engage the PTO
switch by pulling up on the knob and try
to start the engine. The engine should
not start. If it does, the PTO switch must
be replaced. See your Cub Cadet Service
Dealer.
2.
If the engine does not start, disengage
the PTO by pressing the knob down and
start the engine. Now engage the PTO
and the blades should rotate.
3.
If the blades do not turn, the PTO switch
must be replaced, the seat switch must
be replaced or the electric PTO clutch
must be repaired. See your Cub Cadet
Service Dealer.
Parking Brake Switch
•
Sit in the operator’s seat. With the drive
levers in the neutral position and the PTO
disengaged, release the parking brake
and try to start the engine. The engine
should not start.
•
If it does, the parking brake switch must
be repositioned or replaced. See your Cub
Cadet Service Dealer. If the engine does
not start, engage the parking brake and
start the engine.
Seat Switch
With the drive in the neutral position,
the parking brake engaged and the PTO
disengaged, start the engine. Now release the
parking brake and raise up off the seat. Release
the operator’s seat and the engine should stop.
If the engine does not stop, the seat switch
must be replaced. See your Cub Cadet Service
Dealer.
With the drive in the neutral position,
the parking brake engaged and the PTO
disengaged, sit in the operator’s seat and start
the engine. Engage the PTO and the blades
should start to rotate. Raise up slightly off the
operator’s seat and the blades should stop. If
the blades do not stop when you dismount from
the operator’s seat, the seat switch must be
replaced. See your Cub Cadet Service Dealer.
Electric PTO Clutch
This clutch operates when the engine is running,
the operator is in the operator’s seat and the
PTO is engaged. This electric clutch is a normally
trouble free device. If a problem develops and
the blades do not turn, first check the 25 amp
fuse, then investigate the wiring harness and the
connections to the seat switch, the PTO switch
and the electric blade clutch. Then check the seat
switch, the PTO switch and finally the electric
blade clutch. If the PTO clutch is still not working
properly, see an authorized service dealer.
Deck Removal
Remove the mower deck from the tractor as
follows:
1.
Lower the deck to the ground. Capture
the deck lift by placing the clevis pin
behind the lowest position.
2.
Apply the parking brake. Remove
ignition key and the spark plug cap.
Warning!
The muffler and any
surrounding parts at the rear of
the tractor may be extremely hot,
and could cause serious burns.
Use extreme caution when near
the muffler. Allow the muffler to
fully cool before removing the
belt from the PTO pulley.
4.
Using a 1⁄2” drive in the idler pulley
bracket (a), turn the wrench towards the
right of the tractor and slide the PTO belt
(b) off the PTO pulley (c). See Figure 4-12.
(a)
(b)
(c)
Figure 4-12