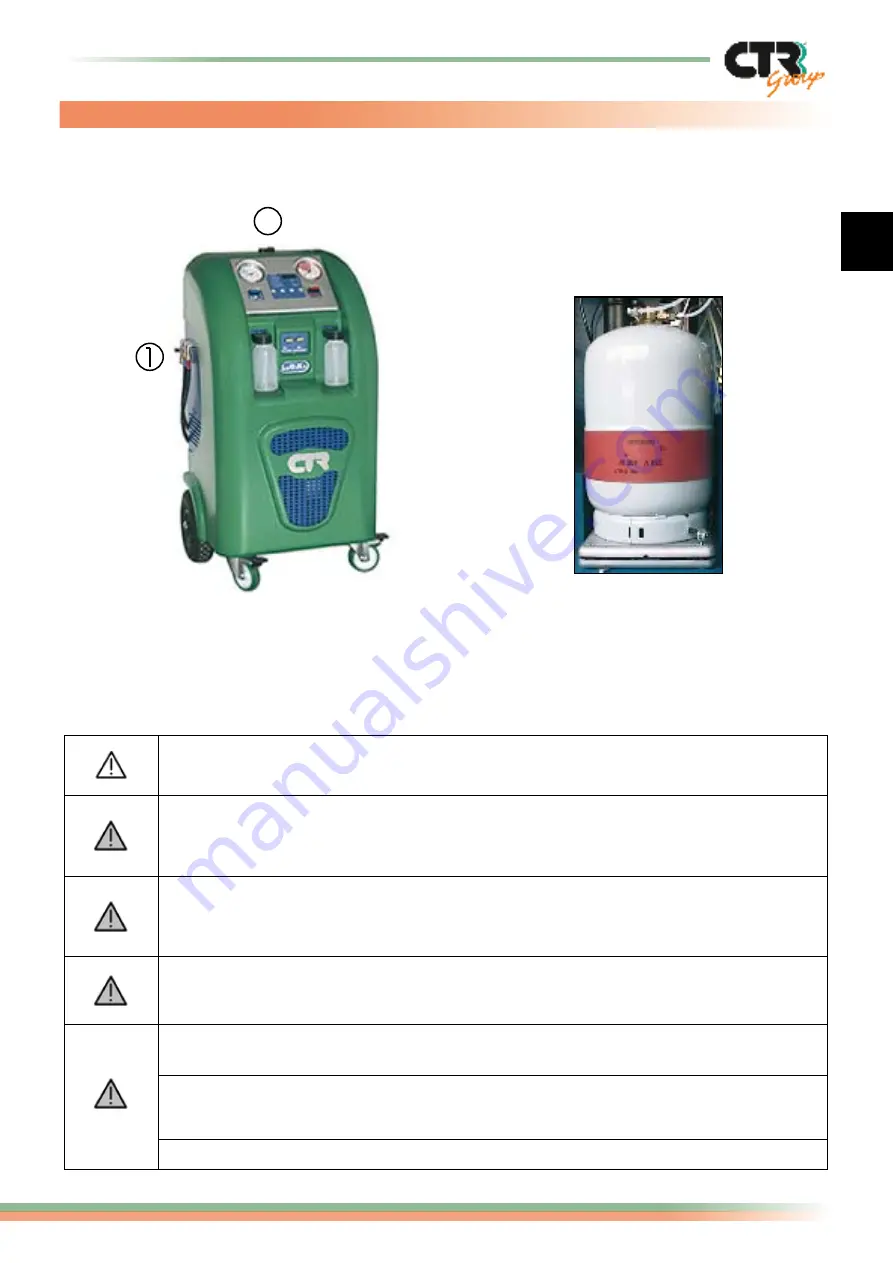
2
EN
Logika - use and maintenance guide
5/16
page
This figure indicates the areas on the machine where there may be a safety hazard during
operations:
When the machine is operating, check the level of oil in the two tanks making
sure that it does not overflow.
We remind you that maintenance and repair carried out by not qualified staff
change the standard of security of the machine and expose the worker to serious
risks.
NEVER
disconnect the
HP
and
LP
hoses, unless expressly stated in this guide.
Do not manually action the manual filling valves during normal operating phases
unless expressly stated in the instructions.
Always wait some minutes after having switched off the machine to allow the
system to be correctly reset (temperature and pressure).
In no case should the operator use combustible or flammable liquids or detergents
for cleaning the machine.
During maintenance work do not contaminate the environment with eventual
residual waste products and always follow the prescribed directives in force
regarding disposal.
NEVER
disassemble the cylinder.
The machine is delivered with
the cylinder correctly positioned
in its seating on the weighing
scale and already fixed with
brackets (n. 2) for this purpose.
3. Warning
1)
Area where refrigerant may be
ejected.
2)
Components carrying live current.