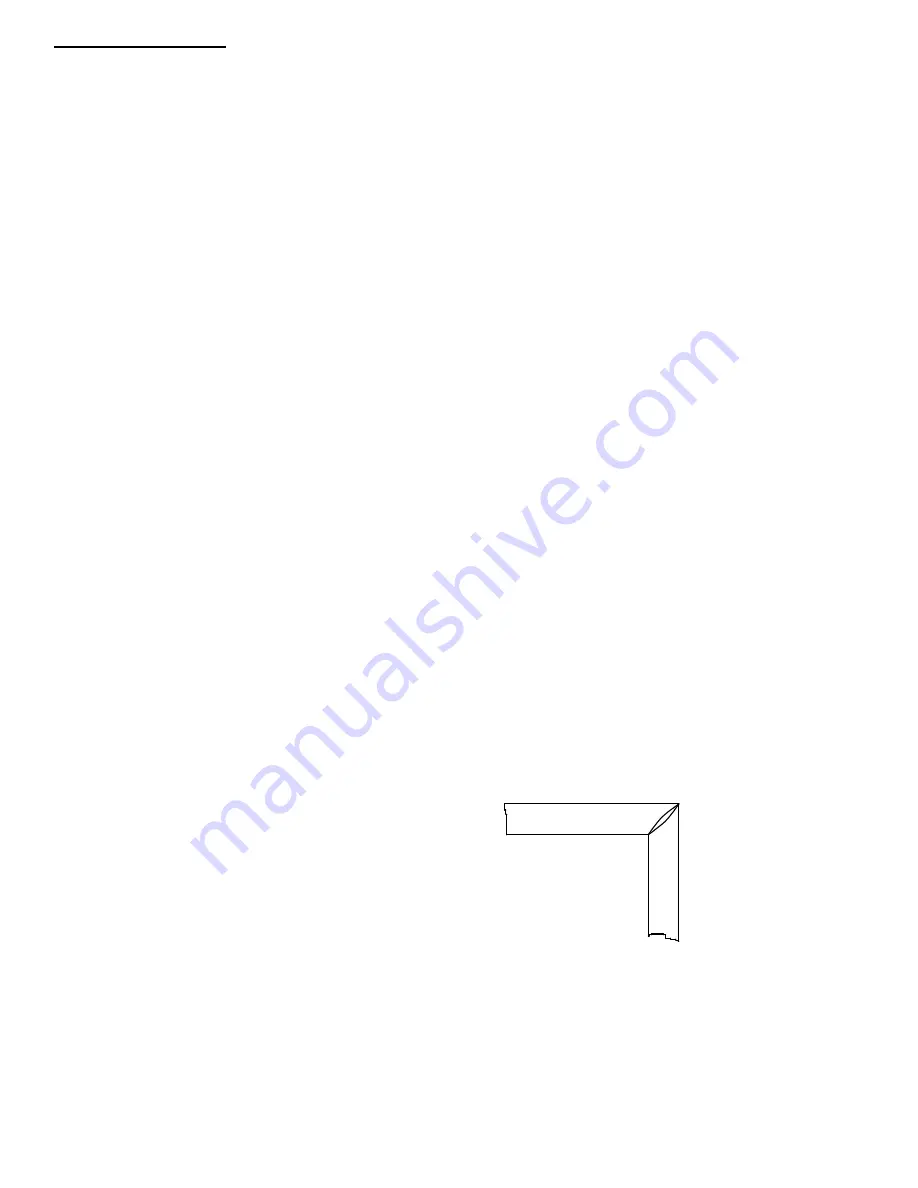
Repair and Service:
Always use CTD factory authorized replacement parts and consult factory before making any repairs or adjust-
ments which may be unclear.
Fence Alignment and 45
Angle Adjustment of Blades:
All machines are preset at the factory for perfect 90
and 45
mitre cuts. If any adjustments are necessary:
1. Check alignment of fences—left to right, as shown in Diagram “B“ on Page No. 5. Use a two foot steel
scale or quality precision straight edge and lay flat on table base. Butt edge against inside fence and
outside fence. Touch the outside corner of the straight edge. If one side of the straight edge pulls away
from the fence, then the outside fence is not in alignment with the inside fence.
2. Loosen 3/8-16 lock nut on both fence brackets. Clean all surfaces of dirt or dust, and re-assemble as
before.
3. Re-align inside fence to outside fence with your straight edge. Once you are sure both fences are in
alignment, you now have a reference point to check your 45
mitre.
If adjustments of the 45
mitre settings are necessary, you will need a precision draftsman’s triangle. Check the 45
mitre by placing the triangle against the inside fence and the plate of the blade, below or in between the gullets or
teeth of a Carbide Blade. Touch the triangle against the steel plate of the blade—not against the tips. If an adjustment
is necessary:
A. Loosen the lock nut on the adjusting screw (3/8-16 Hex Cap Screw), that locks through the 45
Stop Key, P/N 2DM29.
B. Adjust 3/8-16 screw until blade plate aligns perfectly with precision triangle. Now, tighten the screw
and nut. It is not necessary to move the 45
stop key.
Irregular Mitres:
Irregular mitre cuts are almost always caused by out-of-square material. Check your material with a 90
square
and a straight edge. Material that has a high spot on the bottom will move, or roll forward as it is being cut (even
with pneumatic hold down clamps), thereby causing the blade to cut more on the inside of the moulding than the
outside. Another cause of irregular mitre cuts is too thin a blade plate thickness. Blade plate thickness should be
.100 to .110 on 12” blades. Blades will find the easiest avenue to cut through material, and sometimes the blade
plate will distort when cutting heavier sections. The drawing is an example of a cut when blade plate is too thin
for the material being cut.
Other Repairs:
See specific sections within the manual for additional information on repairs and maintenance.
-17-
Summary of Contents for DM200R
Page 18: ... 18 ...
Page 19: ... 19 ...
Page 20: ...DM200 Base Assembly Exploded View Right Side Shown Left Opposite 20 ...
Page 21: ...DM200 Base Assembly Parts List 21 ...
Page 22: ... 22 ...
Page 23: ... 23 ...
Page 24: ...400S Blade Guard and Stand Exploded View Model M516 Shown Right Side Shown Left Opposite 24 ...
Page 25: ...400S Blade Guard and Stand Parts List Model M516 Shown 25 ...
Page 26: ... 26 ...
Page 27: ...400S Base Parts List Model M516 Shown 27 ...
Page 28: ... 28 ...
Page 29: ...Parts list 29 ...
Page 30: ... 30 ...
Page 35: ......