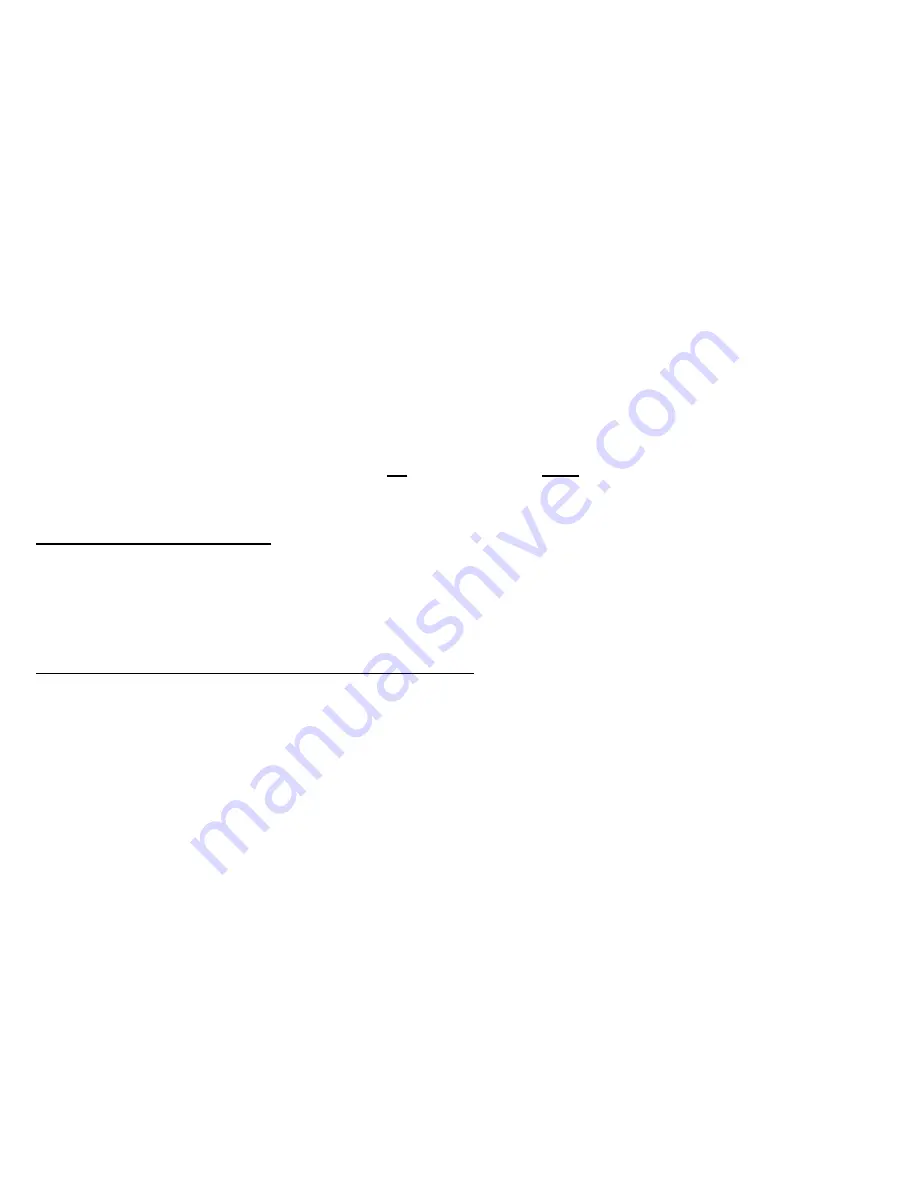
Air Hold Down Clamps for the Material:
Both Horizontal or Vertical Air Clamps are available. Vertical Clamps are provided standard on the machine. These
clamps pneumatically hold the material in place when the saw blades are cutting the material. The clamps are
controlled by a 3-Way Valve mounted on the bottom of the Power Feed Unit. When the machine is in the rest
position, the Upstroke Stud contacts the 3-Way Valve, LV1 & LV2 (2-Way Valve). As soon as the Foot Valve is
tripped, the clamps move into position. A manual shut-off for the clamps is provided should you not want to use the
clamps for a particular moulding.
Foot Valve:
The Foot Valve, P/N B3P53E actuates the clamps into position. Once the Foot Valve is depressed, the Two-Hand
Anti-Tie Down Control is energized and ready to activate. As soon as the Two-Hand Control buttons are depressed,
your foot can be removed from the Foot Valve. The clamp pressure will be maintained by Limit Valve #1 & #2, P/N
B3P50 & P/N B3P49.
Speed Control of Blade Movement:
The downstroke speed of the blade is controlled by the Speed Control Valve, P/N 2B3P61 or P/N B3P60, located in
the lower port of the main drive Cylinder, P/N 2B3P05 or P/N B3P306. Adjust as required for best finish. The
Upstroke Control Valve, P/N B3P63, is located in port No. 5 of the main control Valve, P/N B3P73. Simply loosen
nut on machine screw (10-32 thread) and adjust
IN
to slow down, or
OUT
to speed up.
Preventative Maintenance:
The CTD Double End Trim Saws are relatively easy machines to operate and maintain. Following is a weekly check
list of General Maintenance items. The best preventative maintenance advise is to
CLEAN THE MACHINE DAILY
,
especially around the pivot points on the machine.
Lubrication and Adjustments of Bearings:
NO LUBRICATION OR ADJUSTMENTS ARE REQUIRED
.
All CTD cut-off saws are assembled using sealed,
prelubricated ball bearings. The spindle and pivot assembly are constructed using preloaded belleville springs.
These springs eliminate the need for adjustments of bearings and also greatly increase the life of the bearings.
General Maintenance Weekly Check List:
Always disconnect electrical power and air supply.
1. Keep machine clean—especially around pivot bracket and pivot bearings.
2. Blow off and clean around the cylinder.
3. Check Air Filter Bowl for water and condensation build up.
4. Remove any scrap pieces and dust build up from inside floor stand.
5. Check monthly;
A. For excessive belt wear.
B. Make sure motor pulley set screws are tight.
-16-
Summary of Contents for DM200R
Page 18: ... 18 ...
Page 19: ... 19 ...
Page 20: ...DM200 Base Assembly Exploded View Right Side Shown Left Opposite 20 ...
Page 21: ...DM200 Base Assembly Parts List 21 ...
Page 22: ... 22 ...
Page 23: ... 23 ...
Page 24: ...400S Blade Guard and Stand Exploded View Model M516 Shown Right Side Shown Left Opposite 24 ...
Page 25: ...400S Blade Guard and Stand Parts List Model M516 Shown 25 ...
Page 26: ... 26 ...
Page 27: ...400S Base Parts List Model M516 Shown 27 ...
Page 28: ... 28 ...
Page 29: ...Parts list 29 ...
Page 30: ... 30 ...
Page 35: ......