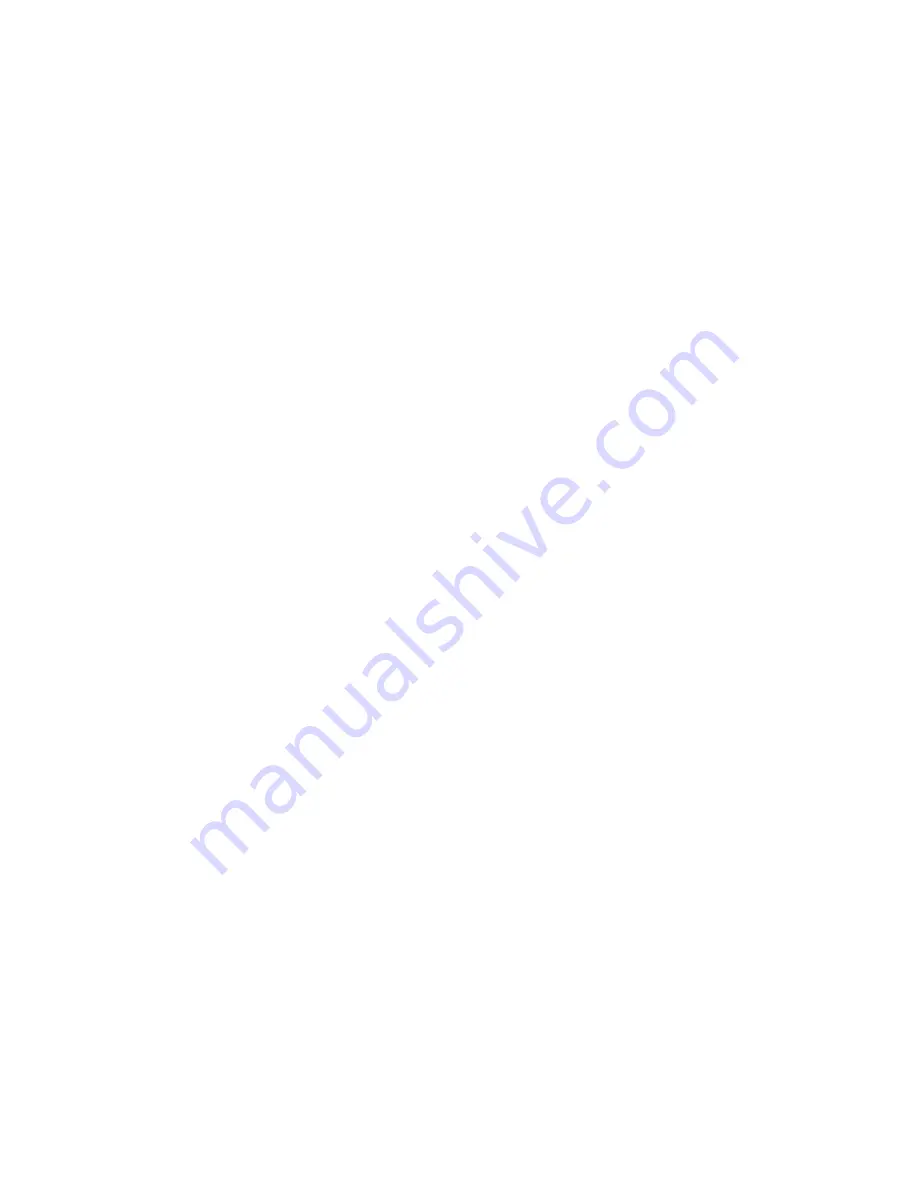
Cutting Aluminum:
As with cutting any material, it is important that aluminum be clamped properly. Precision blades are required for accurate
cutting. CTD suggests and uses a Triple Chip Grind on all our non-ferrous Carbide Blades. When cutting aluminum, or other
non-ferrous materials, it is essential that the blades be lubricated with a saw blade Lubrication System or other blade lubricat-
ing system for the finest finish. See “Saw Blade Lubrication” on next page for more details.
Combination Blades:
Any combination blade is basically an aluminum cutting blade. Significant blade life in-between sharpenings will be lost if a
blade is used for cutting both aluminum and wood. The amount of production for either wood or aluminum should be the
determining factor in the assessment of the particular blade type to be used. Please consult the factory.
CTD Bio Lubrication System:
The CTD biodegradable lubrication system operates by pulse spraying a minute amount of biodegradable
lubricant directly on to the saw teeth of the blade in time-measured increments. The majority of the lubricant
then dissipates with the heat of the cutting action. Chips coming off the blade are hot and dry, and are more
easily collected. (See specific instructions included with system.)
-12-
Cutting Plastic:
Plastic can be cut as easily as wood on all double end trim saws. However, because of its elastic properties, the
material can deflect as the blades pass through. CTD offers Horizontal and Vertical Clamps for this application.
Additional tooling may be required. Special carbide blades are available for cutting plastics.
Angular Adjustment in Opposite direction for CTD Models DM200R or DM400:
1. Remove 90 degree stop, p/n 2DM29 from keyway by removing bolt, lifting away and setting aside.
2. Move Vertical Clamp Assembly on inside fence bracket to center work support by: (see diagram on bottom of page
10 of the instruction Bulletin)
a) Loosen wing nut, p/n 200B1P22
b) Lift vertical clamp adjustment bracket, p/n 200M21 from vertical clamp support bar, p/n 200M20
c) Loosen thread on vertical clamp support bar, p/n 200M20 and
d) Move 200M20 to a threaded hole in center work support and tighten
e) Place vertical clamp adjustment bracket, p/n 200M21, with assembly back on bar, p/n 200M20 and tighten
wing nut.
3. Remove inside fence and inside bracket assembly with key from inside keyway. These are p/n’s 200DC40L or R,
200DM18 and 2DM26 for DM200R, or 400DM06 and 41C04L or R for DM400
4. Move lock down bolt with tab washer (below table surface) from rear holeto front hole.
5. Rotate Top Base Assembly, p/n 200DF21L or R with Sawhead Assembly in the opposite direction, aligning etched
quadrant on base and the desired angle with the secondary zero block and pointer.
6. Attach longer inside fence supplied to the center work support fence Bracket, with the fasteners provided, to create a
new inside fence support for the material to be cut.
7. Align and adjust fences front to back and side to side with outside fences Using a long straight edge.
Make sure fences do not contact blade.
8. Readjust vertical clamp assembly as necessary.
See Diagram on page 10
Summary of Contents for DM200R
Page 18: ... 18 ...
Page 19: ... 19 ...
Page 20: ...DM200 Base Assembly Exploded View Right Side Shown Left Opposite 20 ...
Page 21: ...DM200 Base Assembly Parts List 21 ...
Page 22: ... 22 ...
Page 23: ... 23 ...
Page 24: ...400S Blade Guard and Stand Exploded View Model M516 Shown Right Side Shown Left Opposite 24 ...
Page 25: ...400S Blade Guard and Stand Parts List Model M516 Shown 25 ...
Page 26: ... 26 ...
Page 27: ...400S Base Parts List Model M516 Shown 27 ...
Page 28: ... 28 ...
Page 29: ...Parts list 29 ...
Page 30: ... 30 ...
Page 35: ......