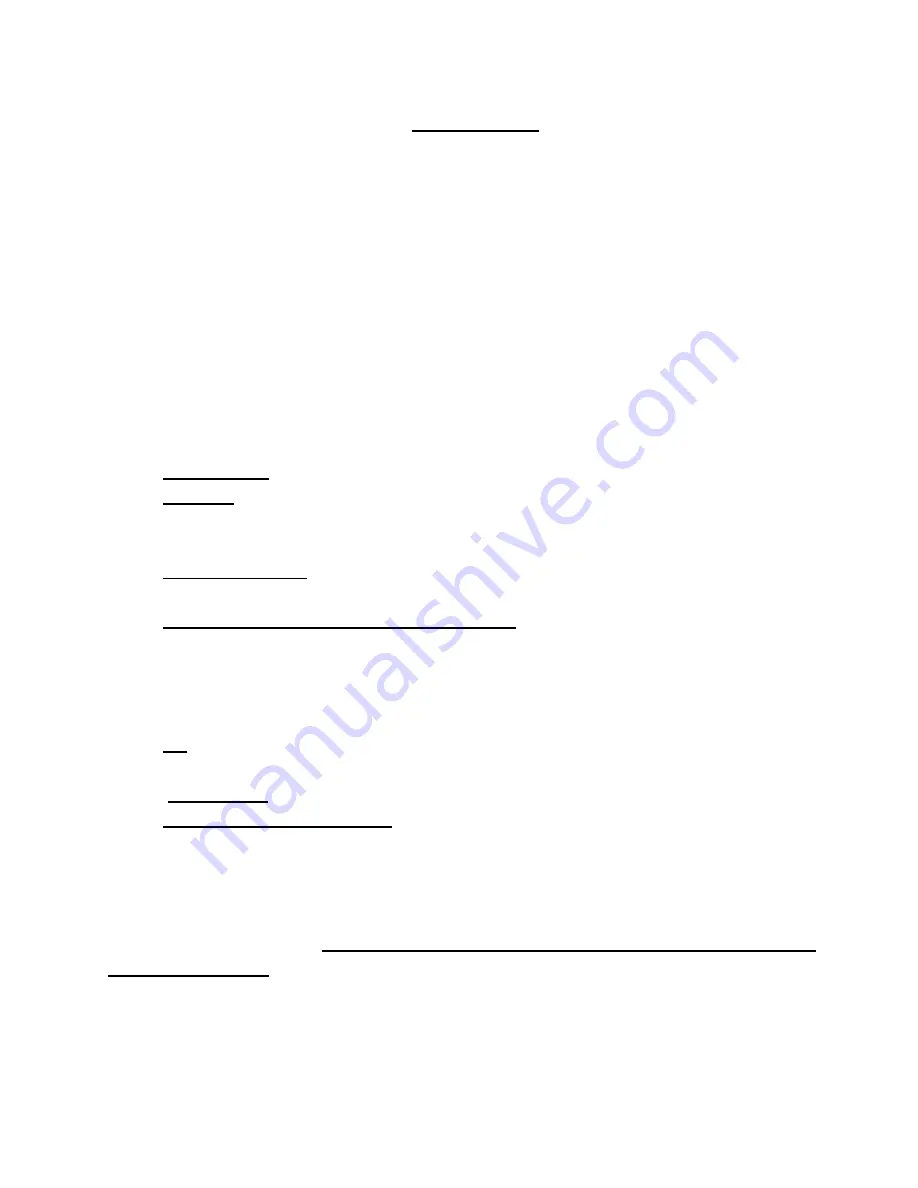
10
OPERATION
Economical and trouble free operation of any process equipment is dependent upon factors such as
maintenance procedures and general overall care of the equipment. To be assured that good
maintenance procedures are being followed, one should understand the general operation of the
equipment. This section contains information that is intended to serve as a process and mechanical
guide for the proper operation of the centrifuge.
In order for the operator to obtain a full understanding of the centrifuge function, a study should be
made of Figure I, where a general flow description is given.
Before any attempt is made to start the CSI Centrifuge for the first time, a quick check should be
made of the following points:
1.)
Free Rotation
- The motor sheave should be free when turned by hand.
2.)
Oil Level
- The machine is shipped full of oil; however, it should be checked after machine
installation. Always start the oil pump motor before starting the main drive motor. When
properly wired, the main drive motor will not start before the oil pump motor is started.
3.)
Rotation Direction
- When looking directly into the main drive motor shaft, it should be
clockwise.
4.)
Electrical Connections of Protection Cut Outs
- The main drive motor should not start
before the oil pump motor is started. One should be able to hear the pressure switch by
turning the pump motor on and off. Disconnecting the pressure line should cause the pressure
switch to drop out. A flow switch is also wired into the control circuit to assure proper
lubrication of the main drive and oil pimp motor.
5.)
Oil
- The pressure should read approximately 15-20 psi when the machine is warm. Should
the pressure side drop below 3 psi, the pressure switch will kick out.
6.)
Motor Loads
- Check the no load motor amperage and compare to the operating amperage.
7.)
Observation of Unload Sound
– The operator should be familiar with the normal operating
sounds of any equipment.
Always start the machine in an unload condition. If the machine should be started in a loaded
condition, the required load could exceed the motor capacity. To be assured that the machine is left
clear of any material after use
, it should be allowed to run approximately ten minutes after the
feed has been cut off.
The operator should always be aware of the normal oil pressure, motor amperage, effluent solids
content and vibration level. By watching the above characteristics one can be fairly certain that the
machine is operating properly. Here is a table giving the above symptoms with their cause and cure: