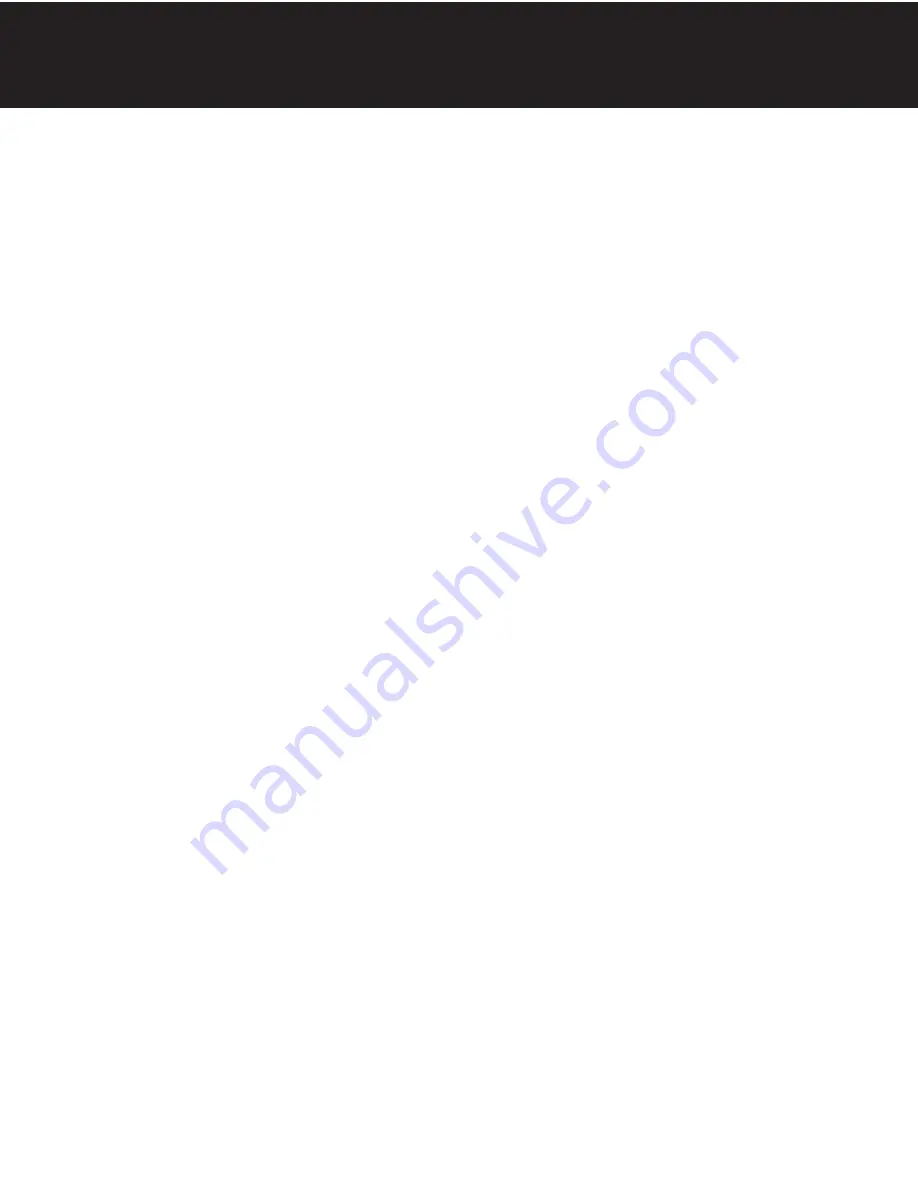
25
Service Instructions / Instructional Videos Available at www.csiwater.com
A.
General Preliminary Instructions
PERFORM BEFORE ALL SERVICING OPERATIONS
1. Turn off water supply to conditioner.
-If the conditioner installation has a “three valve” bypass system, first open the valve in the bypass line, then
close the valves at the conditioner inlet and outlet.
-If the conditioner has an integral bypass valve, put it in the bypass position.
-If there is only a shut off valve near the conditioner inlet, close it.
2. Remove cover and relieve water pressure in the conditioner by stepping the control into the backwash
position momentarily. Return the control to the service position.
3. Unplug electrical cord from outlet.
B.
To Replace Powerhead
1. Remove the control valve cover and disconnect the power supply.
2. Disconnect the meter cable from circuit board and feed back through control (if existing meter is being re-used)
3. Remove lower back base screws and detach lower back base.
4. Remove screw and washer at drive yoke. Remove powerhead mounting screws. The entire powerhead
assembly will now lift off easily.
5. Put new powerhead on top of the valve. Be sure the drive pin on main gear engages slot in drive yoke (wide
side of drive yoke upright must face to the left away form the motor).
6. Replace powerhead mounting screws. Replace screw and washer at drive yoke.
7. Reattach lower back base.
7. Reconnect meter signal, wire and power supply.
8. Reinstall cover.
C.
To Replace Piston Assembly
1. Follow steps
A1 - A3
2. Disconnect the meter signal wire from the circuit board.
3. Remove lower back base screws and detach lower back base.
4. Remove screw and washer at piston drive yoke. Remove powerhead mounting screws. The entire powerhead
assembly will now lift off easily.
5. Remove piston retaining plate screws.
6. Pull upward on end of piston yoke until assembly is out of valve.
7. Inspect the inside of the valve to make sure that there is no foreign matter that would interfere with the valve
operation.
8. Install new seals and spacers.
9. Take new piston assembly and push piston into valve by means of the end plug. Twist drive yoke carefully in a
clockwise direction to properly align it with drive gear. Reinstall piston retaining plate screws.
10. Follow steps
B5 - B9
D.
To Replace Seals and Spacers
1. Follow steps
A1 - A3
.
2. Disconnect the meter signal wire from the circuit board.
3. Remove screw and washer at piston drive yoke. Remove powerhead mounting screws. The entire powerhead
assembly will now lift off easily. Remove piston retaining plate screws.
4. Pull upward on end of piston rod yoke until assembly is out of valve. Remove seals and spacers. (Note: Special
end spacer must be reused)
5. Lubricate new seals with silicone lubricant included in the seal and spacer kit. Make sure the special end
spacer is properly seated in the valve body. Install new seals and spacers individually, pressing around the
outer edge of each seal to make sure it is seated. (When all seals and spacers are seated properly, you will
have a 1/4” of space between the top seal the the top of the valve body)
6. Follow Steps
C9 - C10
.