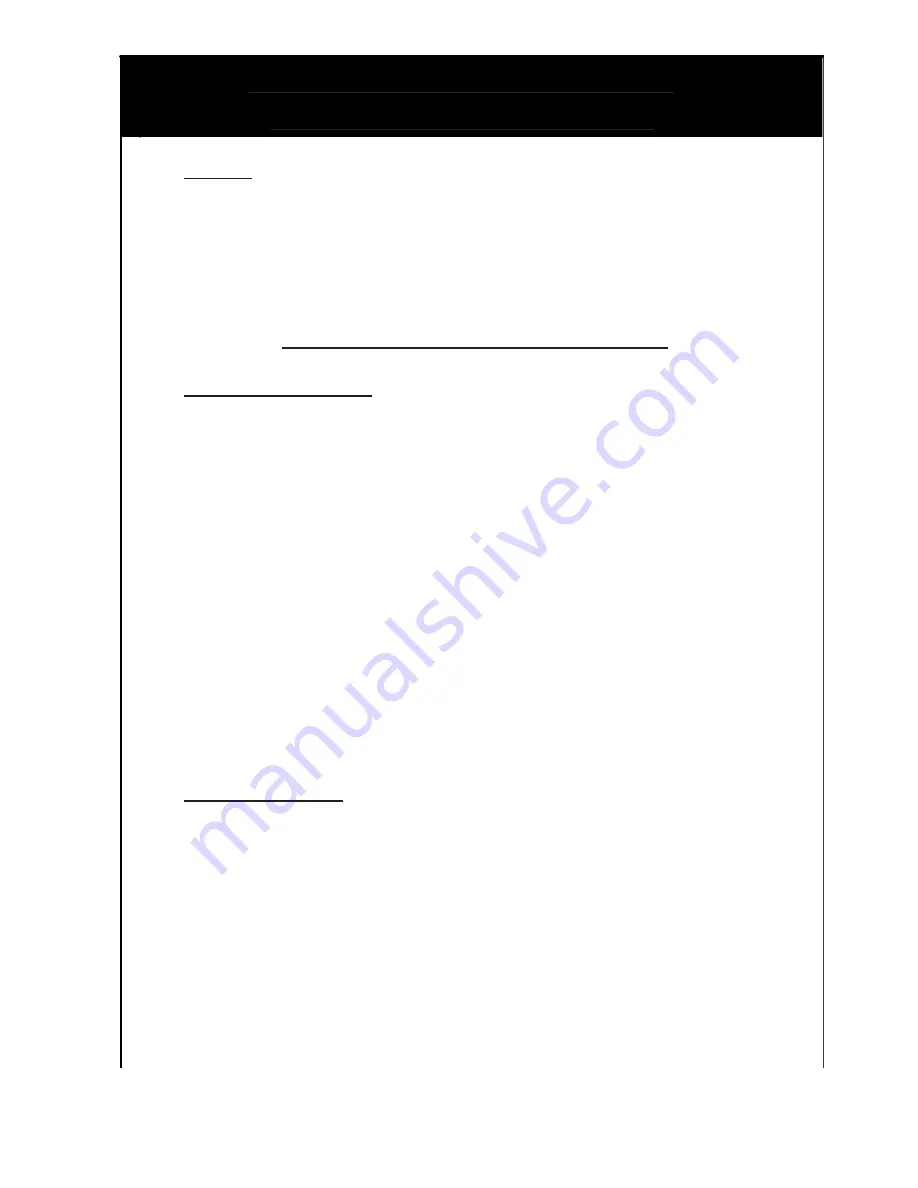
21
Warning
:
This product contains refractory ceramic fibers (RCF). RCF has been classified
as a possible human carcinogen. After this product is fired, RCF may, when
exposed to extremely high temperature (>1800F), change into a known human
carcinogen. When disturbed as a result of servicing or repair, RCF becomes
airborne and, if inhaled, may be hazardous to your health.
AVOID Breathing Fiber Particulates and Dust
Precautionary Measures
:
Do not remove or replace previously fired RCF (combustion chamber insulation,
target walls, canopy gasket, flue cover gasket, etc.) or attempt any service or
repair work involving RCF without wearing the following protective gear:
1. A National Institute for Occupational Safety and Health (NIOSH) ap-
proved respirator
2. Long sleeved, loose fitting clothing
3. Gloves
4. Eye Protection
•
Take steps to assure adequate ventilation.
•
Wash all exposed body areas gently with soap and water after contact.
•
Wash work clothes separately from other laundry and rinse washing ma-
chine after use to avoid contaminating other clothes.
•
Discard used RCF components by sealing in an air tight plastic bag.
First Aid Procedures
:
•
If contact with eyes: Flush with water for at least 15 minutes. Seek
immediate medical attention if irritation persists.
•
If contact with skin: Wash affected area gently with soap and water.
Seek immediate medical attention if irritation persists.
•
If breathing difficulty develops: Leave the area and move to a loca-
tion with clean fresh air. Seek immediate medical attention if breath-
ing difficulties persist.
•
Ingestion: Do not induce vomiting. Drink plenty of water. Seek im-
mediate medical attention.
Important Product Safety Information
Refractory Ceramic Fiber Product
Summary of Contents for 24-03
Page 2: ...2...
Page 8: ...8 Section I General Information FIGURE 1 Dimensional Information...
Page 20: ...20 Figure 16 Bare Boiler Assembly...
Page 24: ...24 Figure 22 Series 24 Jacket Assembly Boiler Models 24 03 thru 24 12...
Page 29: ...29 This Page Is Intentionally Left Blank...
Page 45: ...45 Figure 41 Typical Boiler Wiring with RTC Front...
Page 46: ...46 Figure 42 Typical Boiler with RTC Return Sensor Rear...
Page 62: ...62 Figure 44 Bare Boiler Assembly...