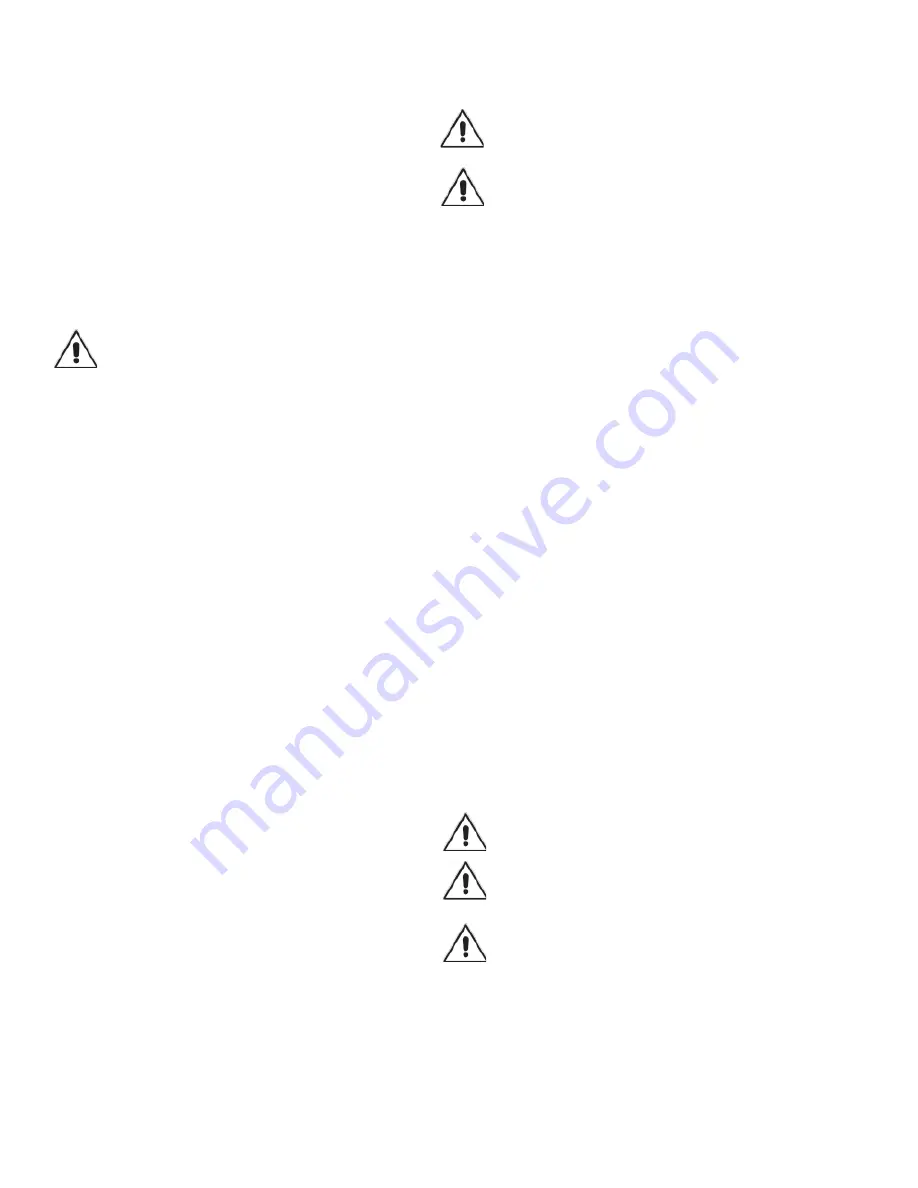
8
NOTE: When using this equipment in environmentally
sensitive areas we recommend using a bio-degradable oil
such as the Mobil EAL 224H.
NOTE: When using this equipment in high temperature
environments we recommend using Dexron Automatic
Transmission fl uid.
SECTION D: START-UP OPERATION
D-1) Power Source Connection:
Connect this pump to an open center hydraulic power source
rated at a maximum fl ow of 7 GPM (preferably 6 GPM) at 2500
PSI. If this pump is to be connected to a larger power source or
if it is to use a bi-directional control valve, a fl ow control and/or
check valve may be required. When connecting hydraulic
hoses to the pump, be sure to keep hose connections clean.
WARNING ! - Overspeeding or reversing fl ow to
this pump will cause damage to the unit and will
void warranty.
D-2) Check Pump Rotation:
Before putting pump into service for the fi rst time, the motor
rotation must be checked. To check the rotation, lay pump
on it’s side slowly and open the hydraulic supply valve until
the impeller begins to rotate. Observe the rotation. The pump
impeller should rotate counter clock wise when viewed from
the suction inlet. To reverse rotation, switch the two hydraulic
lines. Reverse rotation will not damage the pump, however, it
will result in poor pump performance.
D-3) Start-Up:
DO NOT
attempt to start a frozen pump. Instead, submerge
pump in water for twenty (20) minutes before starting.
DO NOT
attempt to thaw a frozen pump with a torch.
D-3.1) Report:
Included at the end of this manual are two start-up report
sheets, these sheets are to be completed as applicable.
Return one copy to the Crane Pumps & Systems Inc. Service
Department and store the second in the control panel or with
the pump manual if no control panel is used. It is important to
record this data at initial start-up since it will be useful to refer
to should servicing the pump be required in the future.
D-3.2) Identifi cation Plate:
Record the numbers from the pump’s identifi cation plate on
both START-UP REPORTS provided at the end of the manual
for future reference.
SECTION E: PREVENTIVE MAINTENANCE:
The only routine maintenance required under normal use is to
check oil in seal cavity in top cover (11). This oil is to be 20W
hydraulic oil (approx. 1 oz. of Pennzoil AW46 or equivalent).
Change oil every 500 hours of operation. If no oil is present or
oil is emulsifi ed, shaft seal may need replacement.
Further maintenance may be required if:
a. Pump discharge volume is inadequate.
b. Oil leakage from pump is present.
SECTION F: SERVICE AND REPAIR
NOTE:
All item numbers in ( ) refer to Figure 3.
WARNING ! - Hydraulic power to the pump must be
disconnected to prevent personnel danger, before
any service work is done to the pump.
CAUTION ! - Always wear eye protection when
working on pumps.
F-1) Disassembly:
Remove cap screws (12) from top cover (11). Remove
top cover (11) and motor assembly from volute (3). Check
condition of o-ring (10), replace o-rings showing any nicks,
cuts, cracks, or deformation. Check for debris in volute.
Check wear ring (4) and replace if there is excessive wear.
Hold impeller (7) securely and remove socket head retaining
screw (5) and cone washer (6) from impeller end. Using hex
key wrench, or hex key socket with impact wrench, unscrew
impeller (7) (right hand threads). Check impeller for wear and
replace if necessary.
Remove bolts (15) to remove handle (16). Remove seal
spring and washer. Examine all seal parts and specifi cally
contact faces. Inspect seal for signs of uneven wear pattern on
stationary members, chips and scratches on either seal face.
DO NOT
interchange seal components, replace the entire
shaft seal (9). Remove motor mounting cap screws (21) from
top cover (11) and carefully remove motor (22). Inspect o-ring
(13) and replace if necessary. Check top cover (11) for wear
and replace if necessary.
DO NOT
disassemble hydraulic motor (22). If motor needs
service, it should be sent to the factory or be replaced.
Checking Oil:
To check oil, remove pipe plug (18) from diffuser (9). With a
fl ashlight, visually inspect the oil in the seal cavity to make
sure it is clean and clear, light amber in color and free from
suspended particles. Milky white oil indicates the presence of
water. If the the oil looks milky white, pour the oil out of the oil
chamber and let it settle in a clean, dry container. If any water
settles out in the bottom of the container or if the oil is white
and thick (emulsifi ed) replace rotary shaft seals and oil.
F-2) Reassembly:
CAUTION ! - Clean all parts with solvent.
DO NOT scrape, sand or fi le aluminum parts.
CAUTION ! - Handle seal parts with extreme care.
DO NOT scratch or mar lapped surfaces.
IMPORTANT ! - It is extremely important to keep
seal faces clean during assembly. Dirt particles
lodged between these faces will cause the seal to
leak.
To reassemble, fasten motor (22) to top cover (11) making sure
that o-ring (13) is in place. Install new shaft seal (9). Screw
impeller (7) onto motor shaft and lightly tap on vane to tighten.
Install cone washer (6) and socket head screw (5) and tighten
while holding impeller fi rmly.
Summary of Contents for Prosser Hymergible 3HPV
Page 10: ...10 FIGURE 3 ...
Page 14: ...14 Notes ...