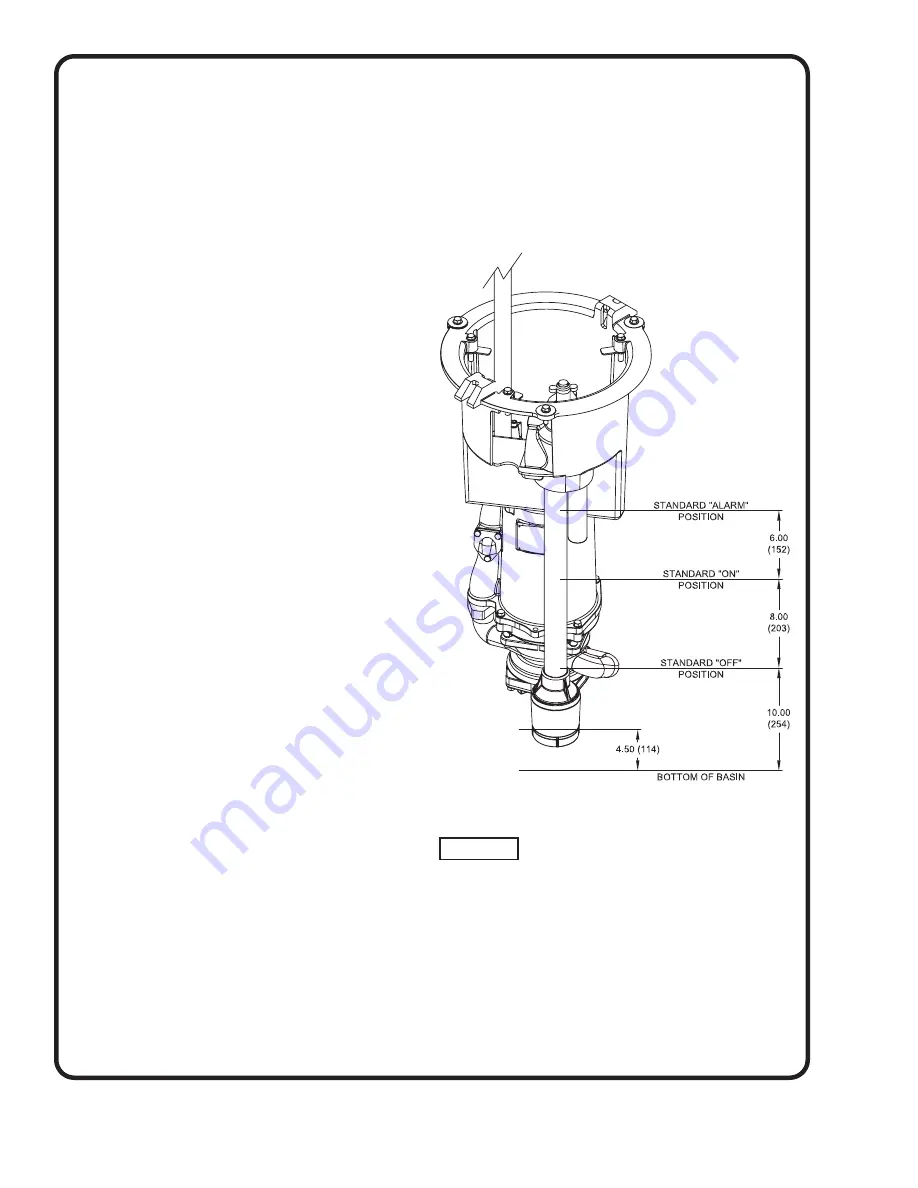
8
BEFORE YOU BEGIN
• Read this manual completely before starting your
installation
• Consult local officials for any applicable codes and
regulations.
• Make sure you have the necessary equipment and
supplies before starting your installation (see tool and
material lists).
TOOL AND MATERIAL LIST
(NOT INCLUDED)
• 1/2” Socket
• Ratchet
• Long Extension
• Wire Strippers (12 AWG to 18 AWG)
• Wire Cutters
• Multi-Meter
• Cable Lube
• Small Slotted Screw Driver
RECEIVING/UNPACKING:
Upon receiving the pump, it should be inspected for dam-
age or shortages. If damage has occurred, file a claim
immediately with the company that delivered the pump.
Unpack pump and record pump serial and model number
before installing. If the manual is removed from the pack-
aging, do not lose or misplace.
STORAGE:
Short Term-
For best results, pumps can be retained in
storage, as factory assembled, in a dry atmosphere with
constant temperatures for up to six (6) months.
Long Term-
Any length of time exceeding six (6) months,
but not more than twenty-four (24) months. The units
should be stored in a temperature controlled area, a
roofed over walled enclosure that provides protection
from the elements (rain, snow, wind-blown dust, etc.), and
whose temperature can be maintained b40 deg.
F and +120 deg. F. If extended high humidity is expected
to be a problem, all exposed parts should be inspected
before storage and all surfaces that have the paint
scratched, damaged, or worn should be recoated with a
air dry enamel paint. All surfaces should then be sprayed
with a rust-inhibiting oil.
Pump should be stored in its original shipping container.
On initial start up, rotate impeller by hand to assure seal
and impeller rotate freely. If it is required that the pump be
installed and tested before the long term storage begins,
such installation will be allowed provided:
1.) The pump is not installed under water for more than
one (1) month.
2.) Immediately upon satisfactory completion of the
test, the pump is removed, thoroughly dried,
repacked in the original shipping container, and
placed in a temperature controlled storage area.
SERVICE CENTERS:
For the location of the nearest Barnes Service Center,
check your Barnes representative or
Crane Pumps & Systems, Inc., Service Department in
Piqua, Ohio, telephone (937) 778-8947 or in Brampton,
Ontario, Canada (905) 457-6223.
INSTALLATION:
Location -
The pump is designed to fit into your basin
suspended from the support pod.
Package Systems-
Refer to manual supplied with basin
package system.
FIGURE 1
(Standard ESPS shown, SensaPRO optional)
Summary of Contents for OGP2022CO Series
Page 14: ...14 FIGURE 9 ...
Page 16: ...16 Wiring for Optional Remote Alarm Light FIGURE 11 ...
Page 20: ...20 FIGURE 16 EXPLODED VIEW FIXED DISCHARGE UPGRADE CORE ...
Page 22: ...22 FIGURE 17 EXPLODED VIEW OGP SERIES ...
Page 24: ...24 FIGURE 18 EXPLODED VIEW OGV SERIES ...
Page 27: ...Notes ...
Page 28: ...Notes ...