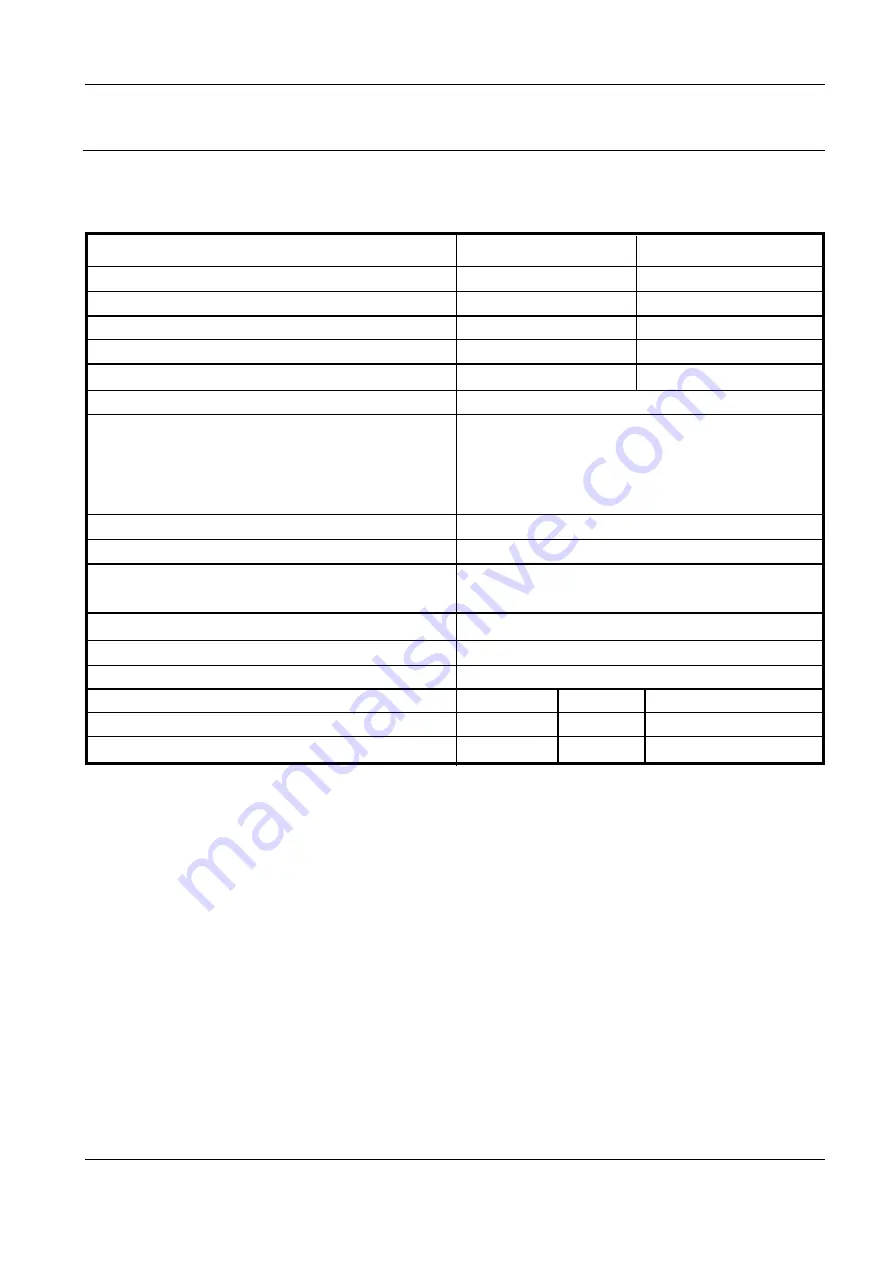
33
ELRO
®
Pumps for hazardous materials GUP 3-1,5 and GP 20/10Ex
8.0 Technical data
The specified data are mean values, measured with water under normal operating conditions
Stage II
Stage I
Nominal Delivery I/min.
300
150
Nominal pumping pressure bar
1.5
1.5
Nominal speed rpm
240
120
Motor power kW
2,75
2,1
Amperage A
6
4,8
Voltage V
380-415, three-phase current
Type of protection
Motor
EEx eII cT3
Circuit breaker
EEx deII cT6
Equipment mains plug
CEAG-GHG 531 7506 VO
Sense of rotation
Clockwise (see arrow)
Couplings
Suction side
(female)
Tapered socket DIN 11851-DN 50
Pressure side
(male)
Threaded socket DIN 11851-DN 50
Dimensions L x W x H mm
620 x 390 x 520 acc. to DIN 14427
Weight, ready for operation kg
98
Pumping hose, electr. conductive
CSM HYPALON
Stage I Stage II
Sound pressure level
Lp
A
[dB]
65
66
DIN EN ISO 3744
Sound capacity level
Lw
A
[dB]
78
79
DIN EN ISO 3744