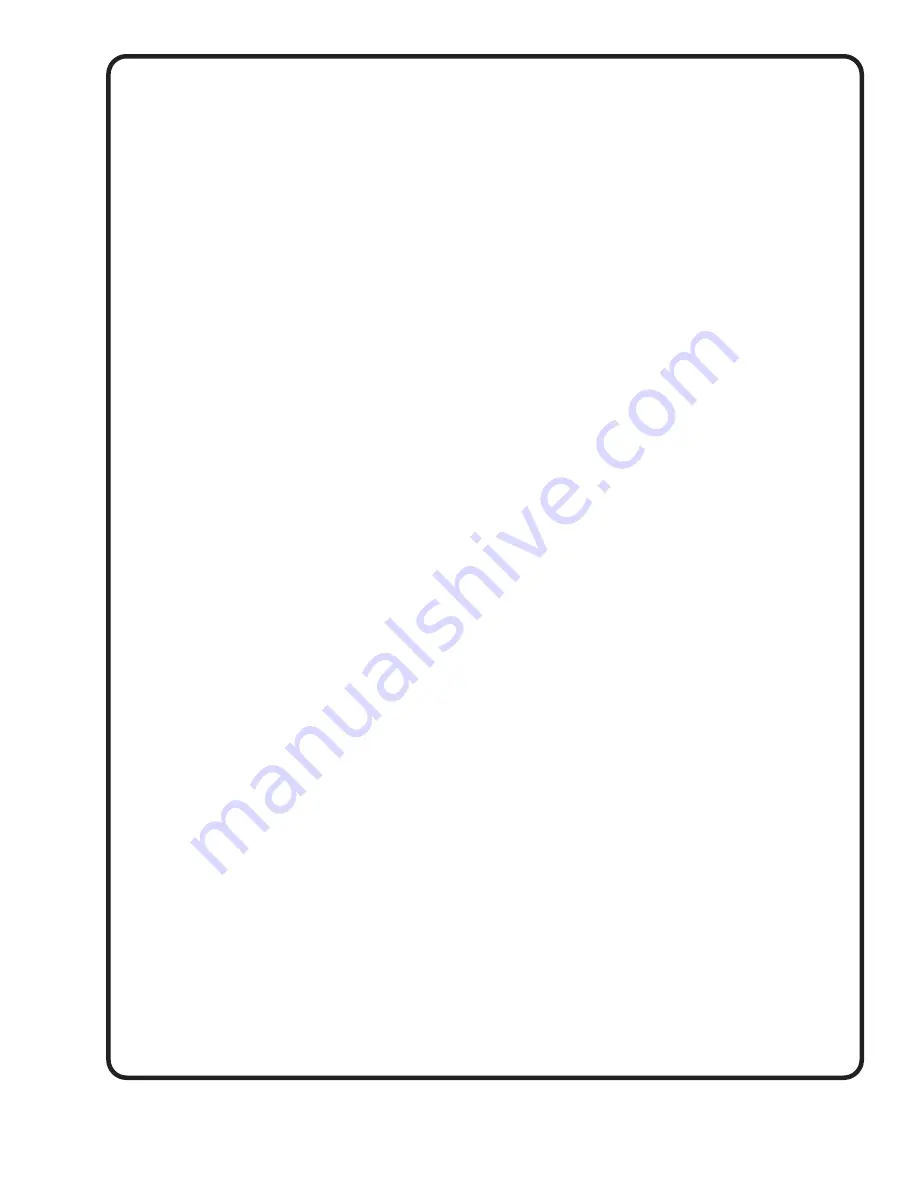
7
C - OPERATION
The following important items should be checked as pump
is started and placed in operation.
a. Pump and driver securely bolted
b. Coupling properly aligned
c. Piping complete
d. Correct pump rotation
e. Pump shaft turns freely
f. Discharge valve closed
g. Suction valve open (if used)
h. Coupling Guard installed
i. Pump fully primed
j. Pump and driver properly lubricated
k. Seal water valve open (if used)
l. Liquid drips slowly from packing gland
Only after these items have been checked should the
pump be started.
1. PRIMING
CAUTION:
Before starting the pump, the casing and
suction line must be fi lled with liquid, and air-vented
through the vent pipe plugs. The pump must not be run
until it is completely fi lled with liquid, because of danger of
injuring some of the parts of the pump which depend upon
liquid for lubrication.
Be sure the stuffi ng box packing or mechanical seal and
power frame are supplied with the proper lubrication. See
LUBRICATION.
Pump priming may be accomplished by one of the
following methods. The discharge gate valve should be
closed during priming.
PRIMING BY SUCTION PRESSURE
When operating with suction pressure (fl ooded suction),
remove the pipe plug at the top of the casing and when
pump is fi lled with liquid, replace plug.
PRIMlNG WITH FOOT VALVE AND STRAINER
A foot valve and strainer may be installed on the lower end of
the suction pipe to keep pump fi lled with liquid. Incorporate
fi ller pipe in discharge pipe between pump and check valve.
Remove pipe plug at top of casing, then fi ll suction pipe and
pump with liquid. When pump is full of liquid, replace plug
and close fi ller pipe.
CAUTION:
When a foot valve and strainer are in stalled on
the suction pipe, a spring loaded type check valve
MUST
be
installed next to the pump in the discharge piping to prevent
pump rupture from water hammer shock.
Priming by means of primer pump or ejector, attached to
the pump, will also remove air from suction pipe and pump
casing. When pump is fi lled with liquid, start motor and
slowly open discharge gate valve.
2. STARTING THE PUMP
On initial start up, the gate valve in the discharge piping
should be closed and slowly opened after pump is up to
speed and pressure developed.
DO NOT
operate pump for
any appreciable length of time against a closed discharge
valve, as this may heat trapped liquid excessively and
damage the pump or seal.
3. PUMP ADJUSTMENT
Open discharge valve as soon as operating speed has
been reached. After the pump has been started the
packing box glands should be tightened to eliminate
excessive liquid loss. (Applies only to pumps having
packed stuffi ng boxes.) Packing should not be pressed
too tight, as this may result in burning the packing and
scoring the shaft or shaft sleeve. The best adjustment will
allow the liquid to drip slowly from the packing box gland.
This will permit proper lubrication of the shaft and dissipate
generated heat.
As soon as the pump and driver have reached the normal
operating temperature, the unit should be shut down for
fi nal coupling alignment. This should be done by following
the instructions found in Section B, Part 3. If correction
is necessary, it may be accomplished by the addition or
removal of shims from under the motor mounting feet.
D. MAINTENANCE
1. INSPECTION
Periodic inspection should be made of the following
components:
a. Bearing lubrication. Make sure the proper grade and
amount of lubrication is present. Section B and
Section D.
b. Packing should be lubricated with the proper
amount and type of acid-resistant lubricant.
c. A double seal should be lubricated with light oil,
clean water, or other compatible lubricating liquid.
d. All piping connections, gasketed joints and drains
should be checked for leaks.
e. Check bearings for excessive wear or failure. Worn
bearings may result in shaft run-out requiring
frequent replacement of packing or seal
f. Coupling alignment and lubrication must be
maintained for smooth operation and long coupling
life.
2. LUBRICATION
All pump and component parts have been lubricated at the
factory except pumps with oil lubricated bearings which
must be lubricated by fi lling oil reservoir through automatic
oiler.
Subsequent lubrication depends on operating conditions.
Periodic inspection of bearing lubrication is necessary and
additional grease or oil should be added as required.
Summary of Contents for DEMING 4060 Series
Page 18: ...Notes ...